High quality diaphragm type pressure gauges are essential tools in a wide range of industries, providing reliable and precise measurements of fluid and gas pressures in various environments. Their design and construction cater to both standard and highly corrosive applications, making them indispensable in sectors such as pharmaceuticals, petrochemicals, food and beverage processing, and water treatment.
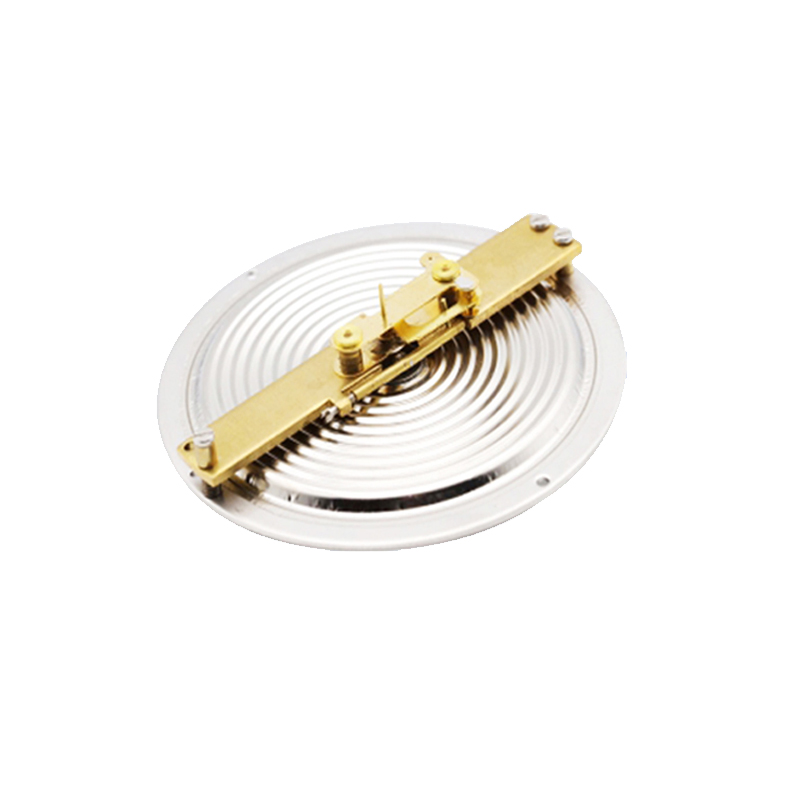
Experience plays a pivotal role in understanding the effectiveness of diaphragm type pressure gauges. Many industries rely on these instruments for their resilience against harsh chemical environments and mechanical stress. For instance, in the pharmaceutical industry, diaphragm pressure gauges ensure that equipment maintains optimal pressure levels during critical processes such as filtration and liquid transfer. The high-quality construction of these gauges, often featuring materials such as stainless steel and PTFE, contributes to their reliability in maintaining accuracy over extended periods. This durability results in lower maintenance costs and ensures consistent performance, which is critical in environments where precision is non-negotiable.
From an expertise standpoint, diaphragm type pressure gauges distinguish themselves through their unique construction features. Unlike their counterparts, these gauges separate the measured media from sensitive mechanical components, effectively preventing contamination and damage. This separation is achieved through a flexible diaphragm, which is crucial when dealing with aggressive chemicals or viscous fluids. The expertise involved in manufacturing these devices ensures compatibility with various process conditions, including temperature fluctuations and pressure differentials, keeping them operational in extreme environments.
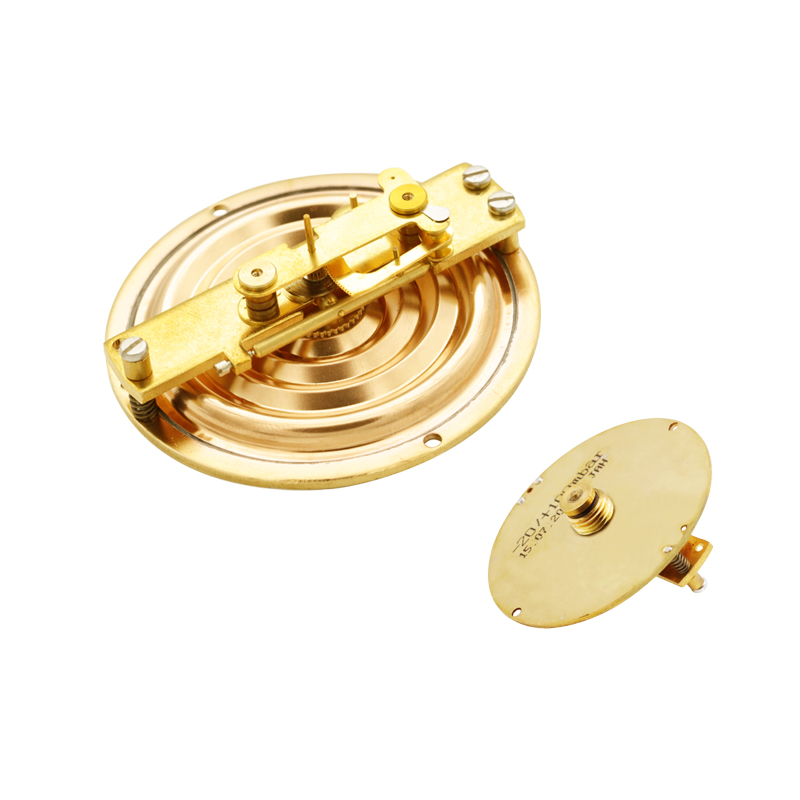
Authoritativeness in the field of pressure measurement is greatly enhanced by the presence of well-designed diaphragm type pressure gauges. Experts often endorse these gauges due to their proven track record in delivering reliable measurements even in challenging settings. Industry leaders recommend them for applications where media incompatibility could lead to measurement inaccuracies or equipment damage. Pressure gauge manufacturers, certified to ISO standards, further establish the credibility of these instruments by ensuring that each gauge meets stringent quality assurance processes. Additionally, many of these gauges come with calibration certificates, building trust through verified performance metrics.
high quality diaphragm type pressure gauges
Trustworthiness is significant in the ongoing operation of high quality diaphragm type pressure gauges. Customers place considerable trust in these devices, as they often serve as a crucial component in safety systems. For example, chemical processing facilities depend on the fail-safes provided by accurately measured and monitored pressure levels to prevent catastrophic system failures. The robustness of these gauges, combined with their ability to deliver consistent and accurate results, reinforces operational safety and product integrity, highlighting why they are a trusted choice for industry professionals.
Incorporating diaphragm type pressure gauges into industrial processes offers significant advantages, not only in terms of operational accuracy but also in long-term cost efficiency. Their capability to endure against aggressive media and harsh conditions significantly reduces the frequency of replacements, assuring users of their investment's durability. Selecting high quality diaphragm type pressure gauges can directly impact the operational efficacy of industrial processes, making them a sound choice for businesses looking to enhance reliability and safety in their operations.
In conclusion, high quality diaphragm type pressure gauges are unparalleled in their ability to offer precision and reliability across various demanding environments. Their exceptional design tailored to withstand the most challenging conditions, combined with their proven track record for durability and accuracy, ensures they remain a cornerstone in the toolkit of any industry reliant on precise pressure measurement. As industries evolve and processes become more advanced, the role of these sophisticated instruments continues to grow, cementing their status as indispensable tools in modern industrial applications.