Precision in measuring differential pressure is pivotal across numerous industries, including manufacturing, aerospace, and chemical processing. OEMs tasked with producing differential pressure gauges that meet stringent standards often navigate through myriad challenges to ensure accuracy, reliability, and durability. This article delves into the intricacies of OEM calibrating differential pressure gauges, emphasizing the essential blend of expertise and authority required to stand out in the market.
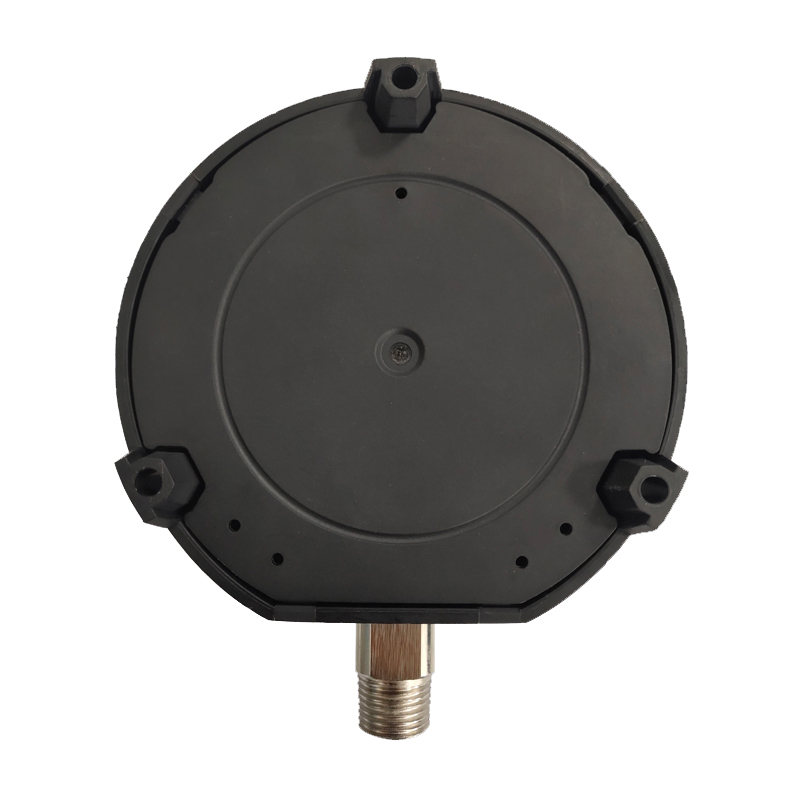
Differential pressure gauges are not merely devices; they are intricate tools that demand exceptional precision. The calibration process begins long before the manufacturing phase. It involves a comprehensive understanding of the gauge's operational environment, the substances it will measure, and the specific conditions under which it will function. This foundational knowledge allows OEMs to design gauges that not only meet industry standards but also exceed them.
The next phase in calibrating these gauges is the meticulous design and engineering process. Expertise here cannot be understated. Engineers must possess in-depth knowledge of fluid dynamics and material sciences, ensuring the gauge’s internal mechanisms can withstand the pressures and temperatures of its intended application. Choosing the right materials is critical; whether it's selecting metals that resist corrosion or elastomers that maintain their elasticity under extreme conditions, every decision impacts the gauge's performance.
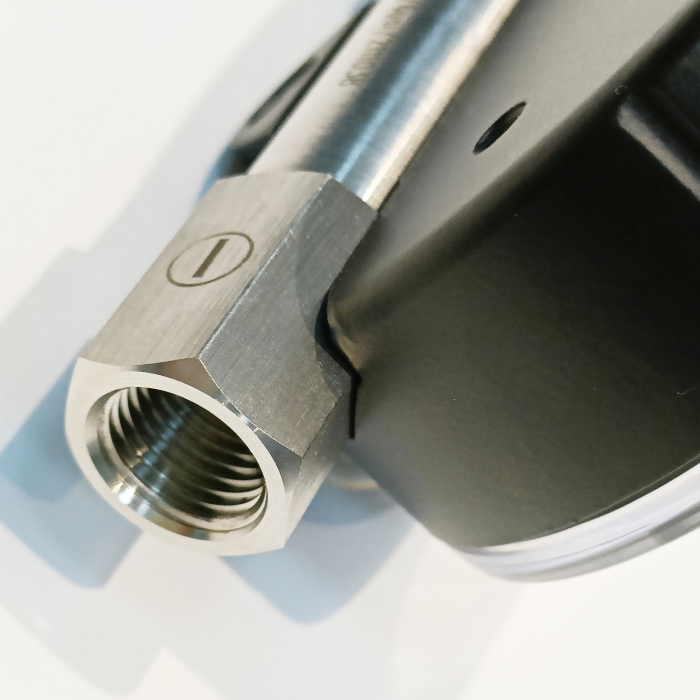
However, design and material choice are only parts of the calibration puzzle. The manufacturing process itself is an exercise in precision and consistency. Adhering to rigorous quality control protocols, OEMs employ advanced automation and robotics technologies to maintain uniformity across their production lines. These technologies, guided by expert operators, are capable of identifying and correcting potential discrepancies that could affect a gauge's performance.
oem calibrating differential pressure gauge
Post-production, a critical phase in calibration involves comprehensive testing. Authoritative testing methods are applied hydrostatic testing, leak testing, and environmental testing under simulated real-world conditions. These tests validate the gauge’s accuracy and durability, offering customers assurance of the product’s reliability. Furthermore, employing state-of-the-art calibration labs equipped with the latest technology presents an opportunity to document and certify each gauge's compliance with global standards, enhancing the gauge's credibility in the market.
Once testing and verification are complete, trustworthiness becomes the focal point. Building trust encompasses transparency and ongoing support. OEMs must provide clear documentation that details the calibration procedures, materials used, and testing results, facilitating an understanding of the gauge’s capabilities and limitations. Additionally, offering continuous customer support and service reassures clients that their equipment will remain precise and functional over its lifespan.
In conclusion,
OEM calibrating differential pressure gauges is far more than a technical obligation; it's a declaration of expertise and authority in the field. By embedding precision from the design phase through to customer support, OEMs position themselves as dependable partners in the industries they serve. They ensure their products not only fulfill but anticipate needs, adapting seamlessly to evolving industrial demands—reaffirming their status as leaders in the realm of differential pressure measurement.