OEM diaphragm seal pressure gauges are pivotal tools across industries, used to measure pressure accurately in applications where fluids are involved. Understanding the complex interplay between their design and functionality can significantly affect operational efficiency and safety within any business utilizing them. Herein, we delve into the experience-backed relevance, expertise informed design intricacies, authoritative recommendations, and trust garnered from using OEM diaphragm seal pressure gauges.

In the realm of industrial applications, diaphragm seal pressure gauges have carved out their indispensable role. This stems from their unique capability to provide accurate pressure measurements without the fluid coming into contact with the measuring element. These instruments consist of a diaphragm that flexes under pressure, ensuring no corrosive or viscous media interferes with the mechanism. Industries dealing with toxic chemicals, pharmaceuticals, food processing, and petrochemicals especially benefit from these gauges, as they safeguard purity and prevent contamination.
From an expert perspective, the design of OEM diaphragm seal pressure gauges is a marvel of engineering. The choice of materials is of paramount importance; stainless steel, Teflon, and Monel are among the preferred options. Each material offers specific advantages like corrosion resistance, durability, and temperature resilience, catering to diverse industrial needs. Precision in manufacturing ensures the diaphragm remains responsive and maintains its integrity under varying pressures and temperatures. Advanced sealing techniques, such as welded or clamped designs, further enhance reliability, making them ideal for aggressive environments.
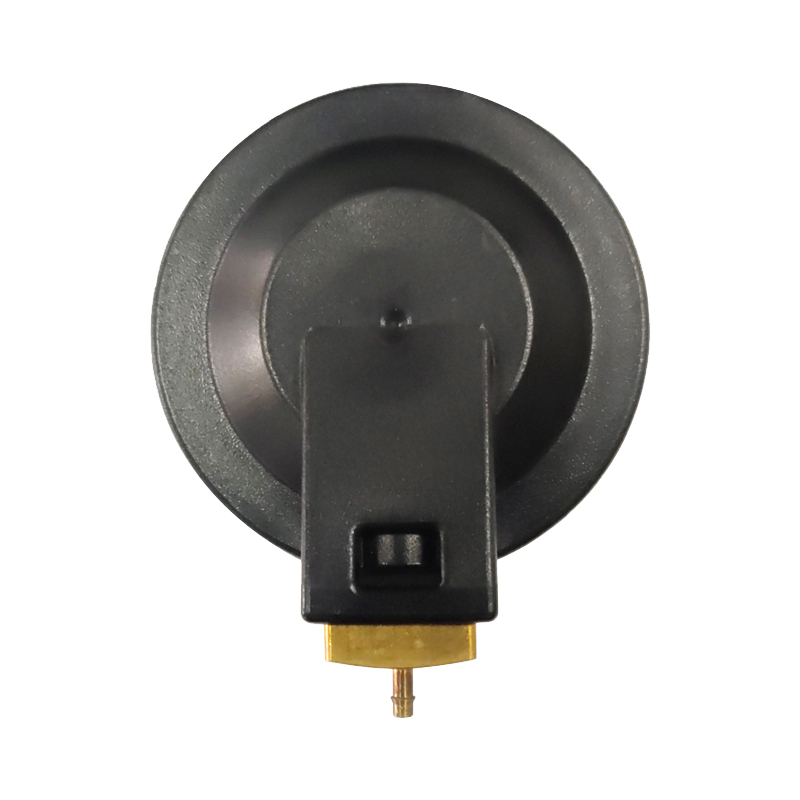
Authoritative standings in the field of instrument manufacturing and usage endorse these gauges for multiple reasons. They provide consistent readings, essential for maintaining operational consistency and meeting regulatory standards. Experts often emphasize the integration of these gauges with automated systems for real-time monitoring, reducing the risk of human error. Furthermore, authoritative bodies in sectors like pharmaceuticals and petrochemicals often demand the use of OEM-approved gauges because of their adherence to strict quality and safety standards.
oem diaphragm seal pressure gauges
Trustworthiness is a cornerstone in the adoption of OEM diaphragm seal pressure gauges. Users can rest assured that these products, having undergone rigorous testing and quality checks, deliver precise readings over prolonged periods. Maintenance of these devices is straightforward, often requiring routine checks and calibrations to ensure long-lasting performance. Testimonials from industry leaders reveal a track record of increased safety, operational efficiency, and cost-effectiveness, reinforcing the credibility of these instruments.
Choosing the right OEM diaphragm seal pressure gauge requires understanding your specific requirements. Factors like the type of media, pressure range, temperature conditions, and surrounding environment must be considered. Consulting with OEM specialists ensures that the chosen gauge is tailored to your needs, leveraging the latest technological advancements for optimal results.
In conclusion, OEM diaphragm seal pressure gauges are not only a testament to engineering precision but also a critical component in maintaining the integrity and efficiency of various industrial operations. Their expertly crafted design, backed by authoritative endorsements and a strong trust factor, make them the go-to choice for industries demanding precision and reliability. As industries evolve, these gauges will continue to adapt, driven by continuous innovations and customer-centric advancements.