High-quality bellow type differential pressure gauges are instrumental in various industries where precise pressure measurements are essential. These gauges stand out due to their exceptional ability to measure small pressure differences in systems that require high levels of accuracy and reliability. Utilizing advanced technology, they can make a significant difference in both efficiency and safety for industries such as HVAC, oil and gas, chemical processing, and water treatment facilities.

Experience in using bellow type differential pressure gauges reveals their unparalleled accuracy and durability. Unlike other types of pressure measurement devices, these gauges leverage a bellow design that allows them to detect pressure changes with extreme precision. This precision is crucial in applications where even the slightest deviation in pressure can lead to significant operational disruptions or safety hazards.
The expertise involved in manufacturing these gauges is evident in their design and functionality. Made from high-grade materials such as stainless steel, the bellow structure offers both flexibility and strength, enabling it to withstand harsh environmental conditions without compromising on accuracy. The use of robust materials ensures the gauge's longevity and reliability, even under rigorous usage. Furthermore, manufacturers incorporate state-of-the-art technology in the design process, often involving computer-aided design (CAD) and sophisticated engineering assessments, to optimize the performance of these gauges.
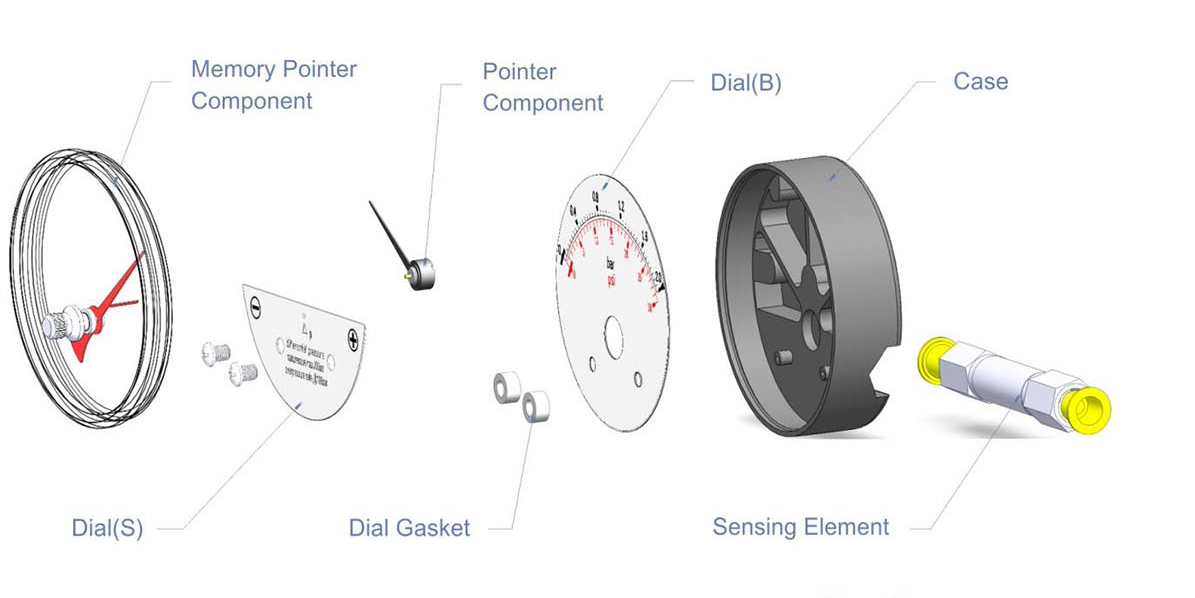
An aspect highlighting the authoritativeness of these bellow type differential pressure gauges is their compliance with international standards such as ISO 9001 and ASME. This compliance assures users of their adherence to high-quality manufacturing processes, attesting to their reliability and precision in various industrial applications. Some models are designed to meet specific industry standards, providing additional assurance of their suitability for particular applications.
high quality bellow type differential pressure gauge
Trustworthiness in these gauges is further established through empirical data and testing. Manufacturers conduct rigorous testing procedures to ensure their products perform reliably under specified conditions. This includes endurance testing, accuracy verification, and environmental testing to simulate extreme operating conditions. These tests are critical as they build confidence among users, knowing that the equipment they rely on meets stringent quality controls.
One of the significant benefits of using high-quality bellow type differential pressure gauges is their versatility. They can be used in a variety of setups ranging from simple installations to complex systems, giving engineers and operators flexibility in their application. This adaptability is particularly advantageous in industries where systems are frequently updated or expanded, requiring instrumentation that can accommodate such changes without the need for constant replacements.
In practical applications, bellow type differential pressure gauges contribute to optimizing processes by providing precise measurements that inform operational decisions. For instance, in HVAC systems, accurate pressure readings can guide adjustments that improve energy efficiency, ensuring systems operate within optimal parameters while reducing energy consumption. In the oil and gas industry, these gauges help monitor pressure levels in pipelines, preventing leaks and ensuring the safe transport of materials.
In conclusion, the high quality bellow type differential pressure gauge is an indispensable tool in precision-driven industries. Its design reflects deep domain expertise, from the materials selected to the manufacturing processes employed, ensuring it meets the highest standards of accuracy and reliability. By choosing these gauges, industries not only comply with standards and ensure operational efficiency but also invest in instruments that enhance safety and longevity of their systems. Their ability to perform reliably in diverse conditions makes them a trusted component, critical to the successful and safe operation of various applications worldwide.