Low pressure differential pressure gauges are crucial instruments in various industries, serving as vital tools for measuring the pressure difference between two points in a system. The accurate measurement of these pressure differentials is essential in maintaining safety, efficiency, and performance in operations ranging from HVAC systems to industrial processes.
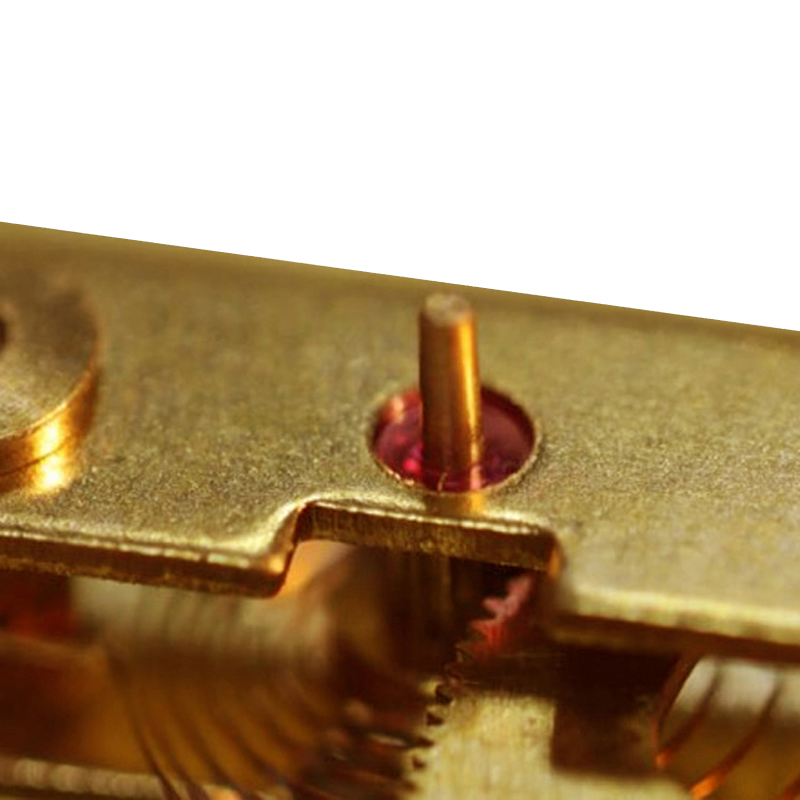
Understanding the Technical Nuances
A low pressure differential pressure gauge is engineered to provide precision in measuring minimal pressure differences that might be overlooked by standard pressure gauges. These devices are meticulously calibrated to detect pressure variations as low as a few millibars, making them indispensable in settings where slight fluctuations can critically impact system functionality.
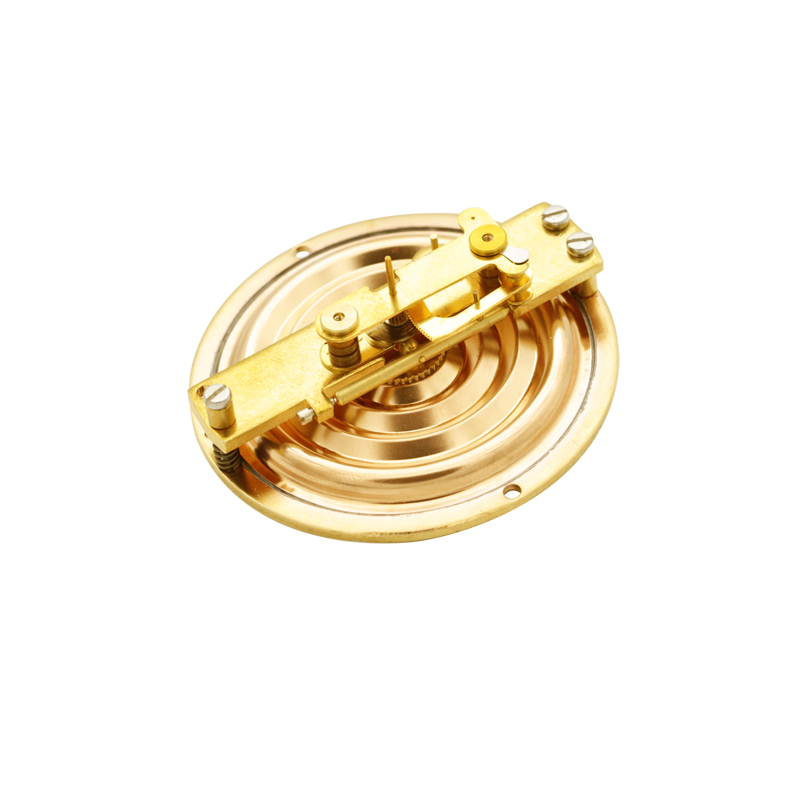
Real-World Applications
In the HVAC industry, these gauges are used to monitor and control air flow across filters, ensuring optimal performance and energy efficiency. By continually tracking the pressure differential, facilities can determine when filters are clogged and need replacement, thus avoiding unnecessary strain on the system and reducing energy consumption.
Another industry that relies heavily on low pressure differential pressure gauges is pharmaceuticals. In cleanroom environments,
maintaining specific pressure differentials is crucial to prevent contamination. These gauges help in ensuring that every section maintains the required pressure differential, thereby guaranteeing a sterile environment for the production of medicines and sensitive equipment.
The Expertise Behind the Devices
Manufacturers of low pressure differential pressure gauges bring extensive expertise to the table. These devices are crafted using advanced materials and technology to withstand harsh environmental conditions while providing precise readings. The design process involves rigorous testing to meet international standards, ensuring reliability and accuracy in various applications.
low pressure differential pressure gauge
Authoritative Insights and Innovations
Authors and industry experts regularly highlight innovations in gauge technology that enhance both functionality and reliability. Recent advancements have introduced digital differential pressure gauges that not only offer high accuracy but also include features such as data logging and remote monitoring. These smart gauges provide users with real-time data, which is invaluable for predictive maintenance and operational efficiency.
Building Trust with Quality
Trust in these instruments is built through quality assurance processes that include calibration traceability. Manufacturers often provide extensive documentation and certifications to validate the performance of their gauges. This transparency in production and testing processes ensures that users can rely on the readings and functionality of the gauges.
Why Choose the Right Gauge?
Selecting the appropriate low pressure differential pressure gauge tailored to your specific application ensures safety and efficiency. An incorrect gauge might not only result in faulty readings but could also compromise the system, leading to operational inefficiency or even hazardous situations. Therefore, consulting with experts and understanding the unique requirements of your application is paramount in gauge selection.
Conclusion
Low pressure differential pressure gauges are more than just measuring tools; they are critical components that ensure safety, efficiency, and performance across various industries. By leveraging the latest technological advancements and validating their accuracy through rigorous standards, these instruments embody the pinnacle of engineering excellence. Trust in their capabilities is cultivated through consistent quality and expert validation, making them indispensable in maintaining the operational success of diverse applications.