Differential pressure gauges stand as critical instruments in various industrial applications, where monitoring the pressure difference between two points is essential for system efficiency, safety, and reliability. Exploring the types of OEM (Original Equipment Manufacturer) differential pressure gauges reveals a world of precision tools tailored for diverse requirements across sectors like HVAC, pharmaceuticals, chemical manufacturing, and oil and gas industries.
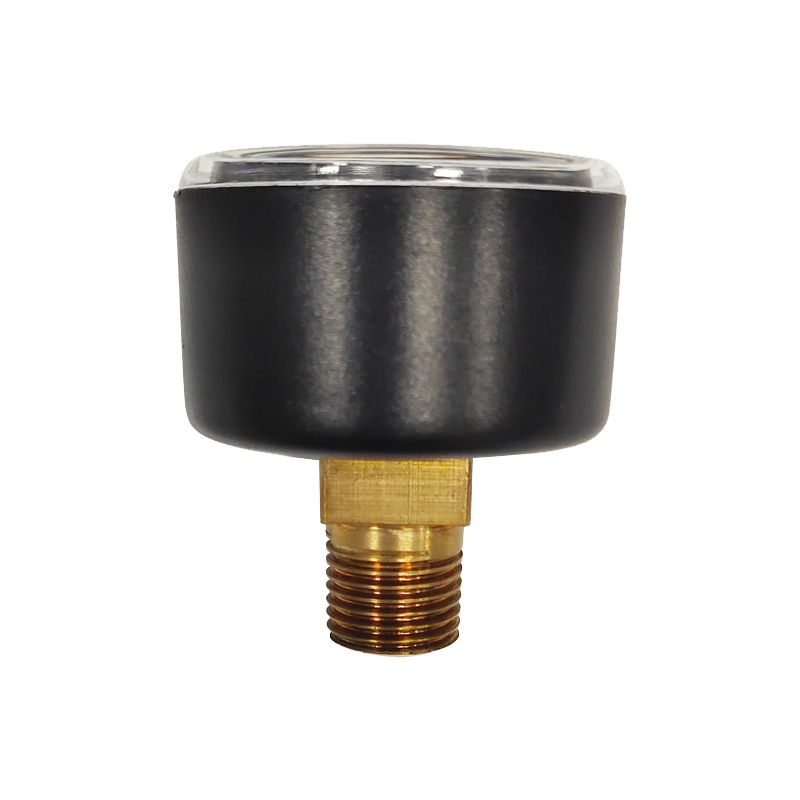
Differential pressure gauges primarily function by measuring the variance between two applied pressures, transmitting this difference into a readable output, thereby helping in analyzing system health. The selection of an appropriate gauge type depends on factors such as application, environmental conditions, accuracy needed, and media compatibility.
Diaphragm Differential Pressure Gauges
These gauges employ a diaphragm as a sensing element, which deflects in response to pressure differences between two sides. Typically used for low and medium pressure applications, diaphragm differential pressure gauges are prized for their accuracy and reliability. They are highly resistant to overpressure, offering substantial protection in processes where pressure spikes are a concern. Due to their durability and compatibility with pulsating pressures, they are prevalent in water treatment facilities and chemical industries where corrosive materials might be present.
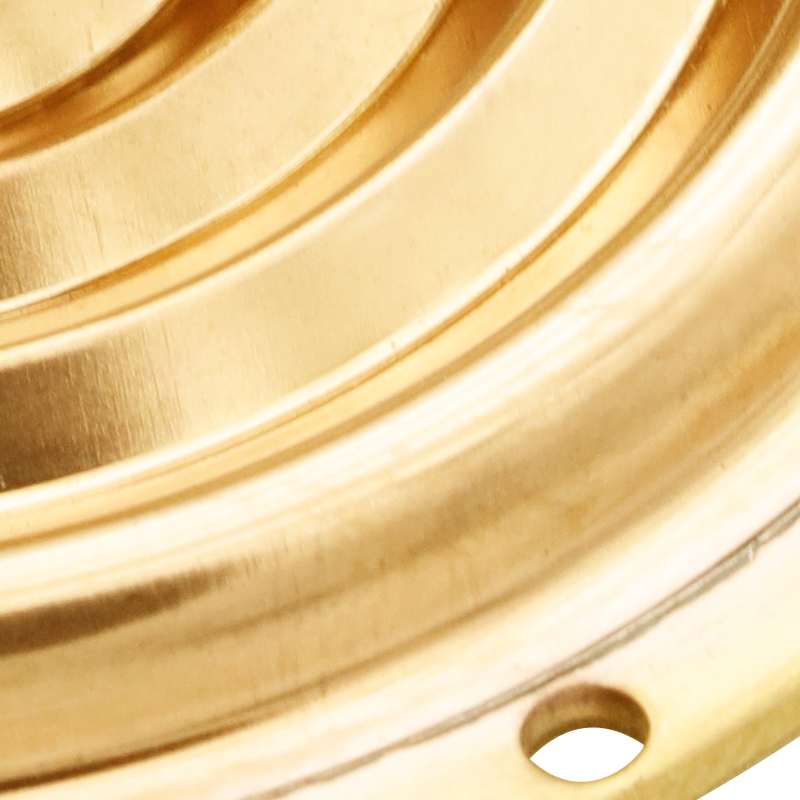
Piston-Type Differential Pressure Gauges
Renowned for their ruggedness, piston-type differential pressure gauges utilize a piston to measure pressure difference. These are particularly suitable for high-pressure applications and are commonly employed in the oil and gas industry. The design can accommodate large overpressure without damaging the instrument, a crucial feature for environments where pressures can vary widely. The piston movement offers good visibility and makes them relatively easy to maintain and calibrate, bolstering their trustworthiness in harsh conditions.
Bellows Differential Pressure Gauges
Bellows gauges contain one or two bellows that extend or contract based on pressure variations. They offer high sensitivity and are ideal for applications requiring fine measurement and control. Bellows gauges are often used in HVAC systems for air flow measurement, ensuring that ventilation systems operate efficiently. Their ability to handle a wide range of pressure makes them versatile, while their intricate mechanism requires precision manufacturing, enhancing their authoritativeness.
oem differential pressure gauge types
Bourdon Tube Differential Pressure Gauges
These operate using the principle of a Bourdon tube changing shape as pressure changes, which translates into a mechanical movement displayed on a dial. While more commonly used for measuring single pressures, they can be adapted for differential pressure tasks. Their robust nature and straightforward construction render them a cost-effective choice for various industrial applications. However, they require regular calibration to maintain accuracy, reflecting the necessity of expertise in their use.
Electronic Differential Pressure Gauges
Integrating advanced electronics, these gauges offer enhanced accuracy and digital output, often interfacing with management systems for real-time data analysis and decision-making. Suitable for applications demanding high precision, like pharmaceuticals or semiconductor manufacturing, electronic differential pressure gauges are becoming increasingly popular. They provide multiple output signals and are capable of interfacing with digital control systems, allowing for seamless integration into complex processes. These instruments exemplify the cutting edge in OEM offerings, promising outstanding expertise and reliability.
Capsule Differential Pressure Gauges
A capsule design includes two metallic diaphragms sealed at their edges. These gauges are particularly beneficial for measuring low-pressure differences and are appreciated for their compactness and affordability. They are often chosen for filter monitoring in clean room applications where space and sensitivity are significant constraints. Their design simplicity provides long-term stability and low hysteresis error, crucial in maintaining the trustworthiness of measurements.
Choosing the right OEM differential pressure gauge is vital to ensure process efficiency and safety. Factors such as media compatibility, temperature range, pressure conditions, and desired accuracy must be thoughtfully considered. OEMs offer customized solutions to meet specific needs, emphasizing the importance of professional consultation and expertise in selecting the right product. This comprehensive understanding not only bolsters authoritativeness but also speaks to the trustworthiness and reliability needed in mission-critical applications across industries.