Navigating the vast array of pressure measurement tools can be daunting, but isolating diaphragm pressure gauges stand out for their exceptional precision and versatility in industrial applications. These gauges have been ingeniously designed to measure pressure accurately, even in the harshest environments where media could be corrosive or extremely viscous.
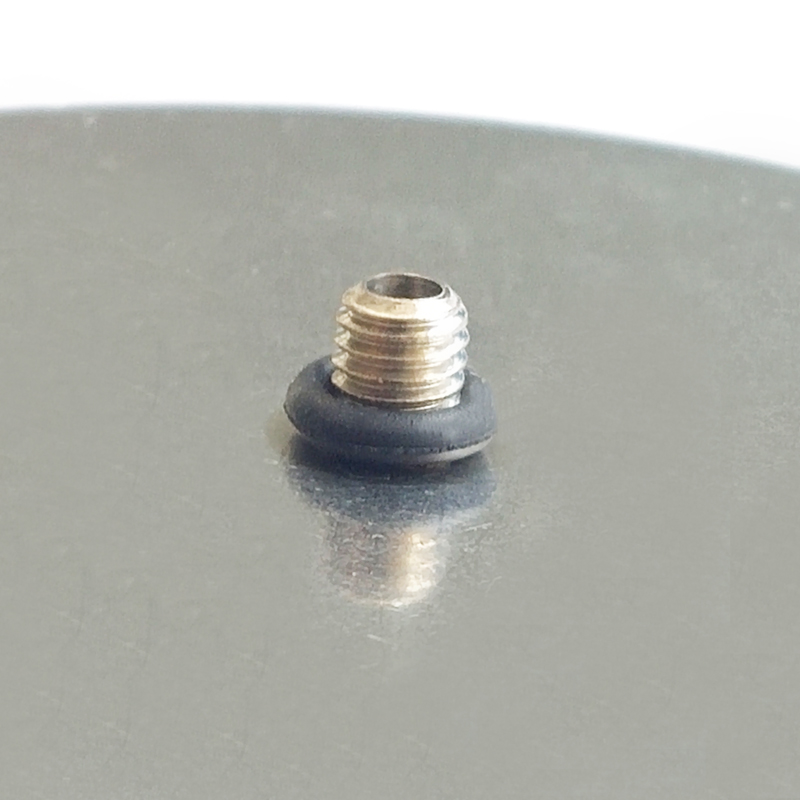
The cornerstone of the isolating diaphragm pressure gauge's effectiveness is its unique design, which incorporates a diaphragm to separate the medium from the measuring instrument. This design not only protects the gauge from aggressive materials but also ensures high accuracy,
as the diaphragm transmits pressure changes to the gauge's sensor fluidly. Experts in the field of pressure measurement often emphasize the importance of this feature, highlighting its role in extending the lifespan of the gauge and ensuring consistent performance across varied applications.
In terms of expertise, identifying the right isolating diaphragm pressure gauge involves understanding specific industrial needs. For example, industries such as petrochemical, food processing, and pharmaceuticals benefit significantly from these gauges due to their ability to handle sterile processes and resist contamination. By selecting a gauge with the appropriate material—stainless steel, Hastelloy, Tantalum, or even PTFE—the gauge can effectively resist the corrosive nature of the medium, thereby enhancing accuracy and reliability. This is where the expertise of suppliers and manufacturers becomes invaluable. They provide guidance on selecting materials that will endure the specific nature of the media encountered, ensuring that your pressure gauge remains trustworthy and effective.
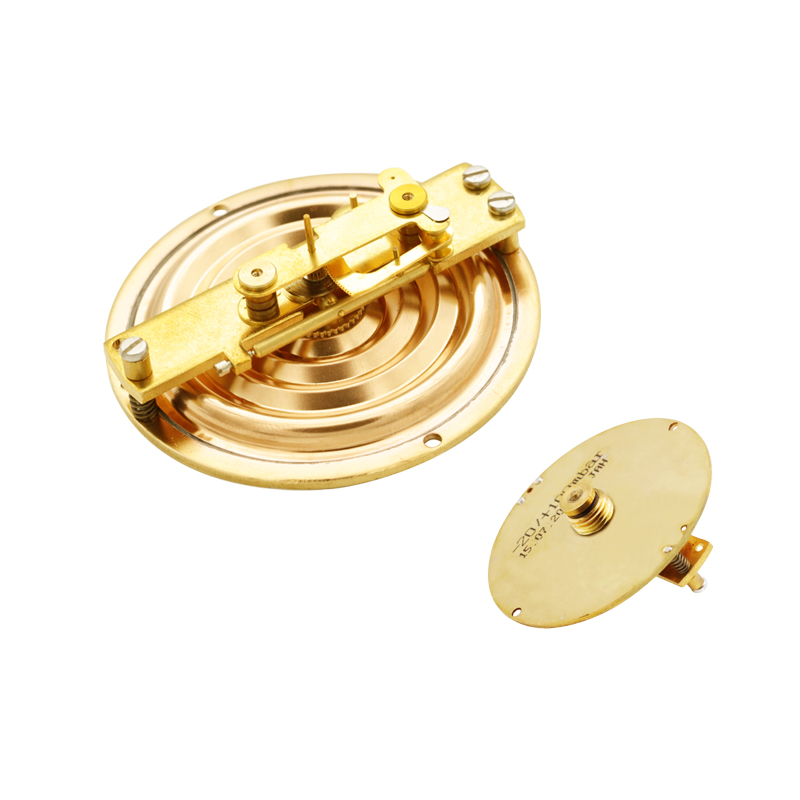
isolating diaphragm pressure gauge
Authority in the field of pressure measurement is often amassed through rigorous testing and certification, demonstrating that an isolating diaphragm pressure gauge meets or exceeds industry standards. Reputable manufacturers adhere to stringent standards such as ASME B40.100, ensuring that their gauges are both reliable and safe to use. Furthermore, acquiring certifications like ISO 9001 or ATEX can assure consumers that the gauges are manufactured under strict quality management systems and can be used safely in explosive environments, respectively.
Trustworthiness with isolating diaphragm pressure gauges is also built through sustained performance and adaptability. A pressure gauge that consistently provides accurate readings boosts operational efficiency and safety, reducing the risk of process failures or accidents. Users often share experiences in which a dependable gauge prevented costly downtime, underscoring the importance of investing in high-quality instruments. Additionally, many gauges are now equipped with digital interfaces and remote monitoring capabilities, allowing for real-time data tracking and diagnostics, further enhancing their trustworthiness.
In conclusion, isolating diaphragm pressure gauges represent a pinnacle of precision and resilience in pressure measurement solutions. By leveraging professional expertise and adhering to authority-led standards, these gauges provide reliable, accurate, and long-lasting performance. Industries around the globe trust these instruments not only for their immediate measurement needs but also for their ability to operate effectively within demanding environments, ultimately safeguarding processes and productivity. As technology evolves, we can expect these gauges to become even more integral to sophisticated industrial operations, pushing the boundaries of what is possible in pressure measurement.