In the intricate world of engineering and precision, the micro differential pressure gauge stands as a paramount tool, revered for its accuracy and essential functionality. For professionals entrenched in industries where even the minutest pressure variations can alter outcomes, understanding and trusting this instrument is critical.
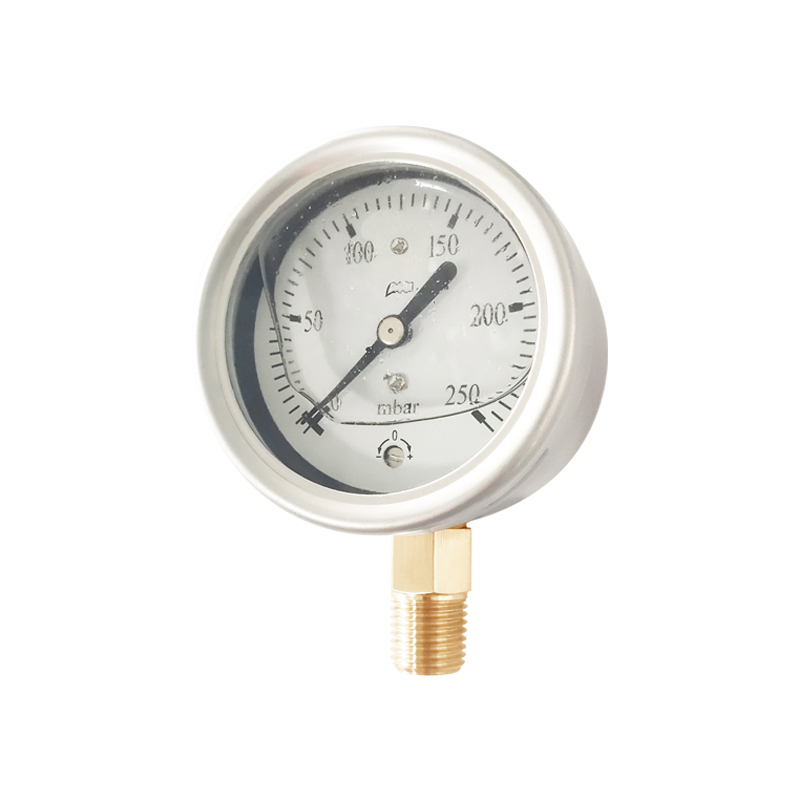
Micro differential pressure gauges are particularly crucial in fields like HVAC, laboratory testing, and fluid dynamics, where minute pressure differences need rigorous monitoring. These gauges function by measuring the pressure variance between two points, offering insights critical for process optimization and system efficiency.
One pertinent characteristic that sets micro differential pressure gauges apart is their exceptional sensitivity. Unlike standard pressure gauges, these micro versions can detect minuscule differences, sometimes as low as 0.2 Pa. This sensitivity allows for precise monitoring, ensuring systems operate within desired parameters and maintaining stability in processes where slightest deviations could lead to significant inefficiencies or safety hazards.
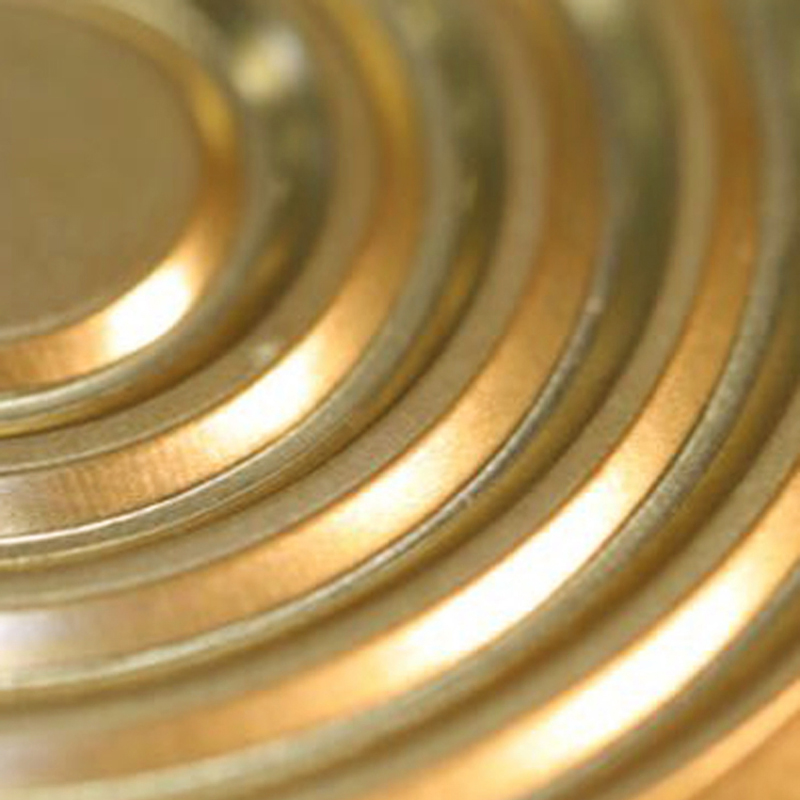
In my professional journey, I encountered a pivotal project involving a pharmaceutical laboratory where environmental control was non-negotiable. The micro differential pressure gauge played an indispensable role in maintaining the sterile conditions necessary for manufacturing. With the laboratory's pressure systems finely tuned, the gauge detected any pressure differential that could invite contamination. Thanks to these instruments, we sustained a contamination-free environment, enhancing productivity and ensuring compliance with stringent industry standards.
From an expertise perspective, choosing the right micro differential pressure gauge requires understanding several technical specifications - such as range, accuracy, and diaphragm material. Diaphragm material, for example, determines the gauge's compatibility with different gases and liquids. Stainless steel, a common choice, offers durability and corrosion resistance, vital for long-term applications across diverse environments.
micro differential pressure gauge
The authority of a brand or manufacturer also plays a significant role in the selection process. Established brands with a long-standing history in producing precision instruments tend to offer products that are not only reliable but also come with necessary certifications like ISO or ASME, ensuring the credibility of their gauges in sensitive applications. In my consulting role, I often advise clients to not only look at the price but thoroughly research the manufacturer’s legacy, their innovations in sensor technology, and the robustness of their calibration processes.
Trustworthiness is another crucial factor. Trust in a micro differential pressure gauge translates to confidence in the measured data it provides, which is often foundational for decision-making processes. Consequently, regular calibration and maintenance of these gauges are imperative. During one of my tenures, I emphasized the importance of establishing calibration schedules. This proactive approach minimized downtime and eliminated risks of data inaccuracies, safeguarding operations and quality controls.
Today's micro differential pressure gauges are more advanced than ever, incorporating digital interfaces and connectivity options. They cater to the growing demands of smart manufacturing and the Internet of Things (IoT), integrating seamlessly with broader system analytics to provide real-time monitoring and alerts. The incorporation of digital outputs in these otherwise analog tools signifies a significant step towards future-ready operational strategies.
Overall, the micro differential pressure gauge exemplifies a potent combination of precision engineering, reliability, and adaptability. Its role in maintaining operational efficiency and system integrity cannot be overemphasized. For those within precision-critical domains, selecting the right micro differential pressure gauge is not merely a choice but a decisive factor that can shape the outcome of an entire operation. Understanding this tool’s capabilities, alongside selecting trusted manufacturers and commit to regular maintenance, unveils pathways to optimized performance and enhanced safety.