In the world of industrial monitoring, cryogenic differential pressure gauges stand out as essential tools for maintaining safety and efficiency in low-temperature environments. These devices are engineered to withstand exceptionally cold conditions, and their precision is unmatched when it comes to measuring pressure differences in cryogenic processes. Drawing insights from industry experts, real-life applications, and extensive research, we delve into the nuances that make cryogenic differential pressure gauges indispensable.

Cryogenic differential pressure gauges are specifically designed for environments where standard pressure measurement tools fail due to extreme temperatures. The cryogenic range typically falls below -150°C (-238°F), where liquid gases like nitrogen, oxygen, and helium are commonly encountered. These extreme conditions present unique challenges, such as material brittleness and instrument malfunction, which are adeptly handled by cryogenic differential pressure gauges.
Experience plays a crucial role in understanding the operational dynamics of these instruments. Industries involved in the production and storage of liquefied gases rely heavily on these gauges. Real-world applications highlight their versatility in processes like gas purification, liquefaction, and transport. Engineers and technicians with hands-on experience endorse cryogenic differential pressure gauges for their robust construction and ability to deliver consistent readings, even amidst severe temperature fluctuations.
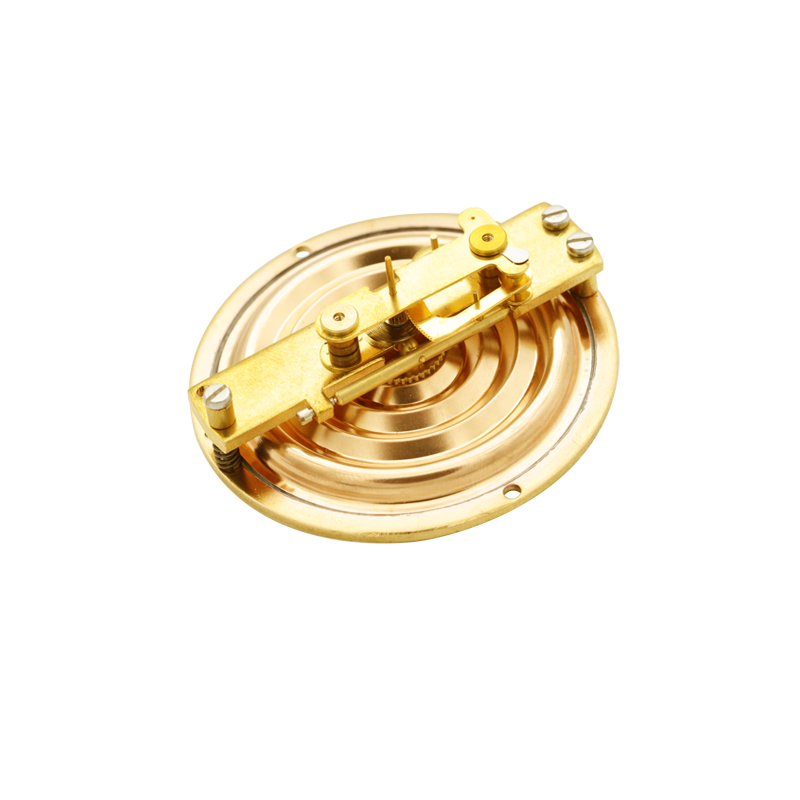
From an expertise standpoint, the functionality of cryogenic differential pressure gauges hinges on their intricate design. They are often manufactured using special materials, such as stainless steel or advanced alloys, capable of preserving structural integrity at low temperatures. The gauges incorporate sensitive diaphragms and advanced sealing technologies to ensure accuracy. These components are carefully calibrated to prevent any condensation or icing, a common issue in cryogenics, which can lead to false readings or equipment damage.
cryogenic differential pressure gauge
Moreover, the authoritative nature of cryogenic differential pressure gauges is underscored by their widespread adoption in critical industries. Aerospace, pharmaceuticals, and food production sectors frequently utilize these instruments to maintain safety and quality. For instance, in the aerospace field, they are instrumental in fuel management systems where precise pressure measurements are vital for optimal performance and safety compliance. Various industry standards and certifications back their usage, further instilling confidence in their reliability.
The trustworthiness of cryogenic differential pressure gauges is reinforced by thorough testing and continuous improvements based on advancements in material science and technology. Manufacturers invest in rigorous testing protocols, often simulating extreme environments, to guarantee that each gauge meets stringent performance criteria. Additionally, ongoing feedback from industrial users drives enhancements and innovations in design, ensuring these tools remain at the forefront of precision measurement.
Choosing the right cryogenic differential pressure gauge involves understanding specific operational requirements and environmental conditions. Key considerations include the temperature range, pressure ratings, and material compatibility with the gases involved. Consulting with manufacturers or industry experts can provide tailored solutions that match the unique needs of any cryogenic application, ensuring optimum performance and safety.
In conclusion, cryogenic differential pressure gauges exemplify a blend of engineering prowess, industry expertise, and proven reliability. Their role in facilitating safe and efficient operations in extreme environments is irreplaceable. As technology continues to evolve, these instruments will undoubtedly emerge more robust and precise, further solidifying their essential position in cryogenic applications. Harnessing the full potential of cryogenic differential pressure gauges not only enhances process efficiency but also safeguards against the inherent risks associated with low-temperature operations.