Understanding and selecting the right OEM mechanical differential pressure gauge can transform the efficiency of industrial systems. The need for accurate measurement of pressure differences in various industrial processes has never been more critical. In industries ranging from chemical processing to power generation, these gauges serve as silent sentinels, ensuring that operations run smoothly and safely without unnecessary downtimes.
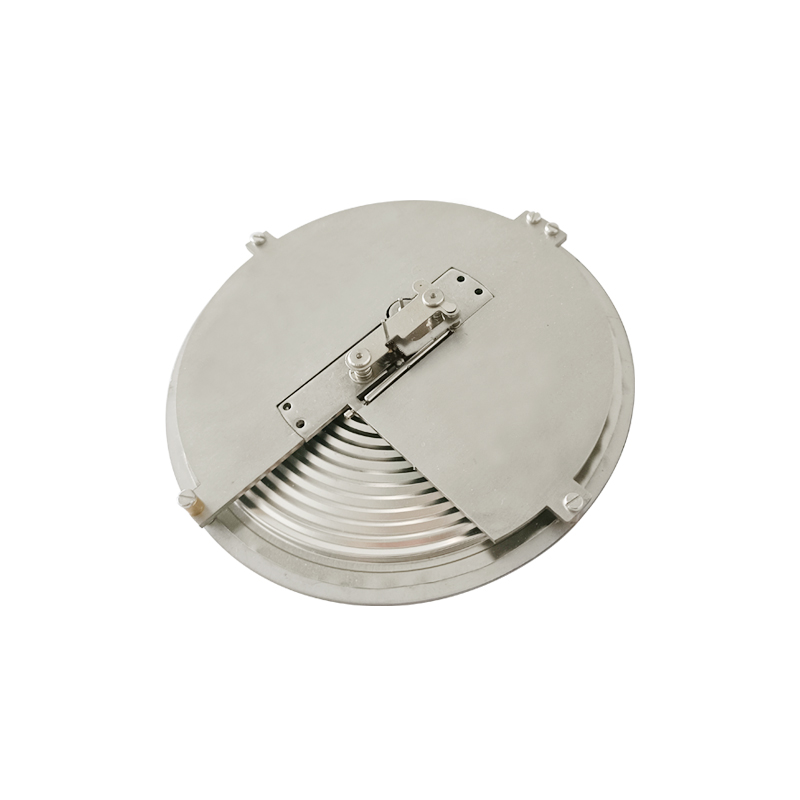
The mechanical differential pressure gauge stands out for its reliability and simplicity. Unlike more complex electronic systems, mechanical gauges operate without external power sources, making them ideal for environments where electricity is either unavailable or undesirable. Their robust construction ensures durability, even in aggressive industrial conditions.
1. How Mechanical Differential Pressure Gauges Operate

Mechanical differential pressure gauges use a differential pressure sensor design involving two separate chambers. These chambers are connected via a diaphragm or a bellows mechanism. Changes in pressure between the two chambers lead to the mechanical deformation of these elements, which, in turn, is translated to a readable output—usually a needle on a dial. This mechanical interplay is not only fascinating in its simplicity but also highly effective in providing real-time pressure readings.
2. Advantages of OEM Mechanical Differential Pressure Gauges
OEM mechanical differential pressure gauges bring in a host of advantages for industrial applications. One of the most significant benefits is their reliability. Without reliance on electrical components, these gauges promise continuous operation even amidst electrical blackouts or interference. This makes them exceptionally suitable for remote or hazardous locations where regular maintenance isn't feasible. Furthermore, since they're typically crafted from robust materials like stainless steel, their longevity is assured even in harsh environments.
Another substantial upside to using OEM versions is customization. OEMs (Original Equipment Manufacturers) can tweak design, materials, and even calibration to suit specific industrial requirements. This customizable nature ensures that industries can operate at optimal efficiency, having tools perfectly configured to their needs.
3. Applications Across Industries
The versatility of mechanical differential pressure gauges is evident in their broad application spectrum. For instance, in the HVAC industry, these gauges are used to monitor airflow and ensure that heating and cooling systems work efficiently. They play a pivotal role in filter monitoring, indicating when a filter becomes clogged and needs changing, thus maintaining system efficiency and reducing energy costs.
oem mechanical differential pressure gauge
In the oil and gas sector, these gauges help in monitoring the flow of liquids and gases, ensuring that processes are running within desired operational parameters. The chemical and pharmaceutical industries also rely on these gauges to maintain strict pressure conditions, critical for ensuring product consistency and safety. The ability to offer precise measurements under high-pressure conditions makes them indispensable in these sectors.
4. Selecting the Right Gauge
Choosing the right OEM mechanical differential pressure gauge requires understanding your specific needs. It's essential to consider the pressure range, temperature conditions, and the medium (liquid or gas) that will interact with the gauge. Calibration and accuracy are other crucial factors. An inaccurate gauge can lead to faulty readouts, resulting in inefficiencies or even catastrophic system failures.
Equally important is the gauge's compatibility with existing systems. It is essential to ensure that the gauge can be seamlessly integrated into current setups or workflow processes without extensive modifications.
5. Maintenance and Trust
Even though mechanical gauges are renowned for their durability, regular maintenance checks are advisable to ensure continual accuracy and performance. Look for any signs of wear and replace parts as necessary. Calibration might need checking periodically, especially if the gauges have been subjected to extreme conditions.
In choosing an OEM for mechanical differential pressure gauges, consider companies with a proven track record of reliability and quality. Reviews from existing users, certifications, and adherence to industry standards are vital indicators of a manufacturer's credibility. A trusted OEM not only provides quality gauges but also offers ongoing support and guidance, ensuring that industries can count on their products for the long haul.
In conclusion, OEM mechanical differential pressure gauges are not just vital tools for pressure measurement; they are integral components that contribute significantly to operational efficiency and safety across various industries. Balancing reliability with innovation, they provide industries with the assurance of consistent performance, making them an indispensable asset in the ever-demanding industrial landscape.