Differential pressure gauges are critical instruments in various industries, playing a pivotal role in monitoring and ensuring safe and efficient operations. Understanding the different types of differential pressure gauges is paramount for selecting the right one for your specific application. Here, we delve into the major types of differential pressure gauges, providing industry insights based on hands-on experience, expert knowledge, and authoritative information.
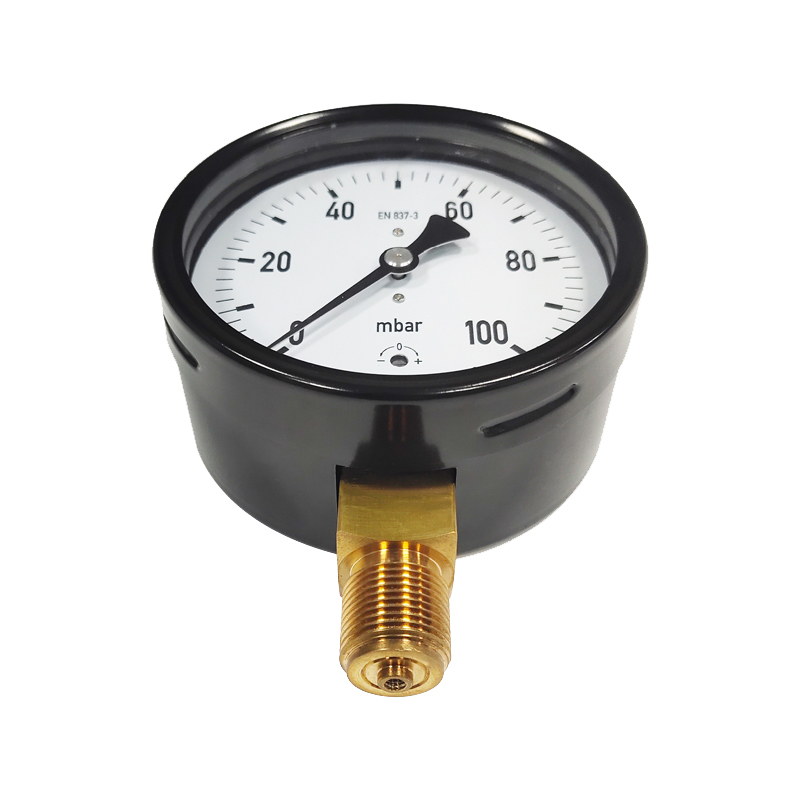
Differential Pressure Gauges An In-Depth Exploration
Differential pressure gauges measure the difference in pressure between two points within a system. This measurement is crucial in applications ranging from HVAC systems to industrial process controls. By knowing the pressure difference, operators can monitor system performance and diagnose potential issues effectively.
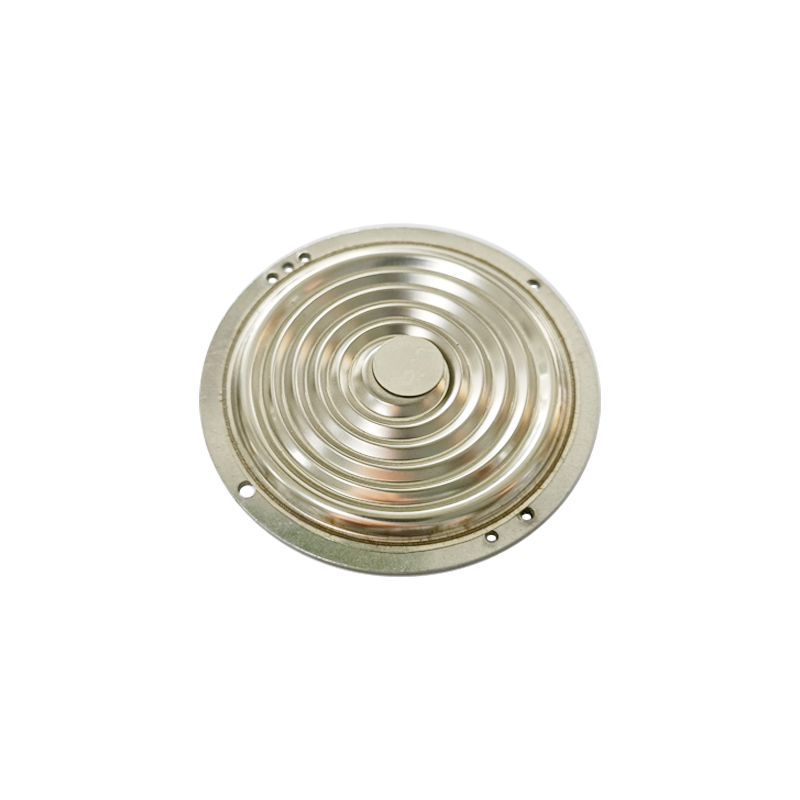
1. Piston Differential Pressure Gauges
Piston differential pressure gauges are renowned for their rugged design and reliability. Widely used in hydraulic and pneumatic systems, these gauges employ a sealed piston that moves in response to pressure differences. This movement is translated into a readable measurement. Known for their durability, piston gauges handle harsh environments and high-pressure scenarios, providing reliable data over long periods.
2. Diaphragm Differential Pressure Gauges
Diaphragm gauges use a flexible membrane to separate two pressure chambers. Changes in pressure cause the diaphragm to deflect, and this movement is captured mechanically or electronically. These gauges are ideal for applications requiring high sensitivity and the capacity to handle small pressure differences, like in laboratory environments and low-pressure filtration systems. Diaphragm materials can be tailored to resist corrosion and chemical exposure, enhancing their versatility across industries.
3. Bellows Differential Pressure Gauges
Bellows gauges feature a series of flexible, accordioned tubes that expand and contract in response to pressure changes. Valued for their precision and robustness, they are commonly employed in industrial settings where precise measurements are necessary. Bellows gauges are excellent options when the pressure elements need tight sensitivity due to low differential pressures. Their design allows for accurate readings even in fluctuating temperatures and processes.
4.
Bourdon Tube Differential Pressure Gauges
Bourdon tube gauges are well-known for their robustness and simplicity. A curved tube straightens with pressure changes, creating movement that is translated to a dial reading. These gauges offer high reliability and are suitable for applications where rugged operation and durability are essential, such as in chemical and petrochemical industries. Bourdon tubes are less sensitive to shock and vibration, making them suitable for challenging environments.
differential pressure gauge types
5. Electronic Differential Pressure Gauges
With advancements in technology, electronic differential pressure gauges have gained popularity due to their precision and versatility. Instead of mechanical means, these gauges use pressure sensors to convert differential pressure into an electronic signal. This data can be easily integrated into automated systems for real-time monitoring and control, making them indispensable in modern industrial automation, HVAC systems, and environmental monitoring.
Choosing the Right Differential Pressure Gauge
Selecting the appropriate differential pressure gauge demands a clear understanding of the application's requirements. Key considerations include
- Pressure Range Ensure the gauge can measure the required minimum and maximum pressures.
- Media Compatibility The gauge materials should withstand exposure to the media being measured.
- Accuracy Higher accuracy may be necessary for critical operations requiring precise control.
- Environmental Conditions Consider the operating environment, including temperature extremes and potential for mechanical shock or vibration.
- Output Requirements Determine if a mechanical readout is sufficient or if electronic integration is necessary.
Trust and Expertise in Decision Making
When selecting a differential pressure gauge, expert advice and trusted recommendations play crucial roles. Partnering with reputable suppliers and manufacturers ensures access to high-quality, reliable instruments backed by industry knowledge and robust support.
In conclusion, understanding the types of differential pressure gauges and selecting one that aligns with your operational needs enhances system efficiency and safety. With the right expertise and insights, these critical instruments can provide lasting value, ensuring optimal performance across applications and industries.