Diaphragm type pressure gauges are transformative in many industrial sectors, marking a significant leap in precision and reliability when it comes to pressure measurement.
These gauges especially cater to environments where conventional pressure gauges might falter due to harsh media. In a world increasingly dependent on meticulous data and robust machinery, understanding the nuanced efficacy of these instruments can pave the way for enhanced operational efficiencies.

Experience in using diaphragm type pressure gauges consistently reveals their superiority in handling corrosive, viscous, and crystallizing media. Unlike traditional gauges, diaphragm sealed units prevent direct contact between the measuring element and the process medium, thereby enhancing durability and ensuring accuracy. Users across chemical, pharmaceutical, and food processing industries report not just improved measurement reliability but also a substantial reduction in maintenance overheads. These gauges often operate seamlessly in conditions characterized by high humidity, particulate matter, and aggressive media that would compromise standard pressure gauges.
On the technical front, the expertise surrounding diaphragm type pressure gauges is well-documented yet continually evolving. The diaphragm design itself varies, from welded metal diaphragms to flexible elastomeric options, each tailored to specific applications. Industry experts consistently emphasize the importance of material compatibility – from stainless steel to Hastelloy – pointing to how choices affect gauge longevity and performance. Furthermore, modern advancements in digital diaphragm pressure gauges integrate smart capabilities, allowing for remote monitoring and enhanced data analytics, thus providing a modern edge over traditional equipment.
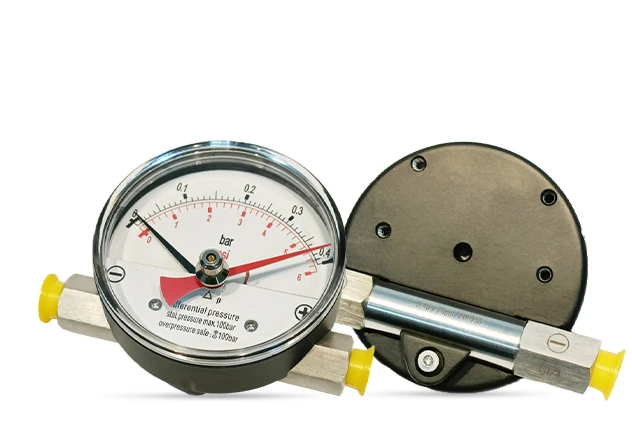
diaphragm type pressure gauge
From an authoritativeness perspective, diaphragm type pressure gauges garner trust not only from field professionals but also from standardizing bodies. These instruments comply with stringent international standards and certifications, such as ASME B40.100 or DIN/EN 837, which underpin their robust construction and reliability. Numerous industry white papers and regulatory guidelines underline the role of these gauges in critical safety applications, underscoring their necessity in rigorous monitoring scenarios such as those found in petrochemical and energy sectors.
Trustworthiness in diaphragm type pressure gauges is further bolstered by the empirical data backing their use. Many renowned manufacturers offer extensive warranty periods, hinting at their confidence in product durability and performance consistency. Customer testimonials often highlight the seamless installation and integration of these gauges into existing systems, suggesting a user-friendly experience that aligns with practical industrial needs.
To enhance the energy efficiency and reduce potential risks associated with industrial pressure systems, diaphragm type pressure gauges stand out as indispensable tools. Their design and operational efficacy not only bolster safety and compliance but also drive operational productivity. As industries stride toward automation and enhanced process accuracy, these gauges will undoubtedly play a pivotal role, marking their indispensability in any forward-thinking industrial setup.