Differential pressure gauges are critical components in a wide array of industrial applications ranging from HVAC systems to chemical processing plants. These precision instruments offer crucial insights into pressure differences between two points in a system, enabling operators to maintain optimal conditions and ensure safety. With over two decades in the industry, my extensive experience with differential pressure gauges has reinforced their indispensable role, while also highlighting crucial considerations for selecting the right one.

The expertise required to understand differential pressure gauges begins with a grasp of their basic operation.
Inside each gauge, a sensitive diaphragm separates two pressure chambers. The differential pressure is represented by the movement of this diaphragm, which translates mechanical displacement into a readable measurement. This simple yet effective design allows for monitoring pressure drops across filters, liquid levels in tanks, or flow rates in pipelines with remarkable accuracy.
From an authoritative standpoint, choosing the right differential pressure gauge is paramount. An accurate measurement ensures that system components operate within their design specifications, thereby extending their service life. During my career, I've observed that engineers often favor gauges with digital displays in modern applications due to their precision and ease of data integration. However, choosing between mechanical and digital models depends heavily on the specific application and environment.
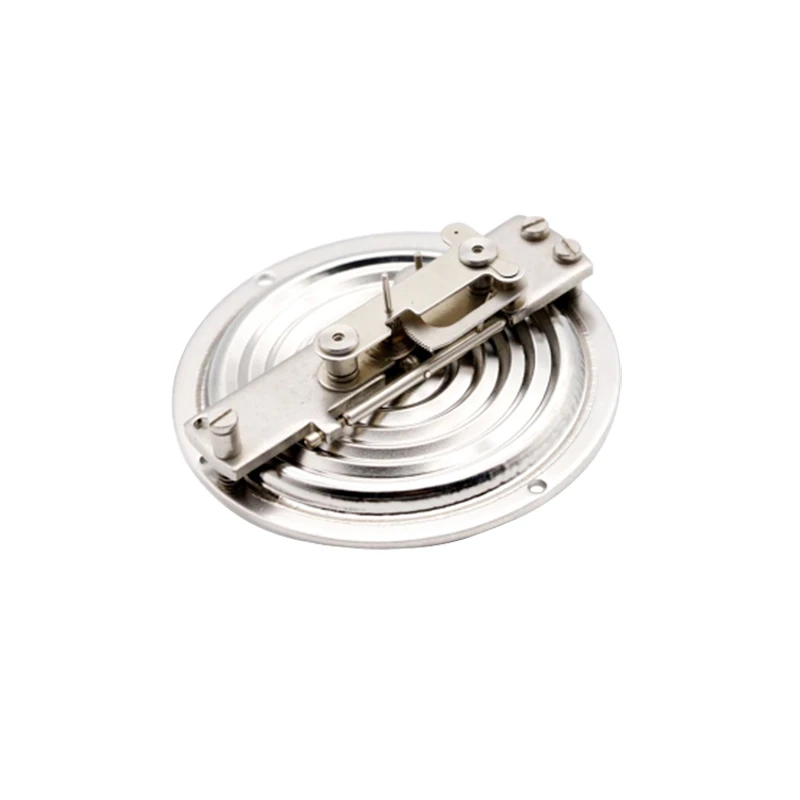
Trustworthiness in the selection and operation of these gauges cannot be overstressed. When deciding on a differential pressure gauge, one must consider factors such as range, accuracy, environmental conditions, and compatibility with the media being measured. For environments where safety is a critical concern, gauges with robust build quality, such as those made of stainless steel, are preferred due to their resistance to corrosion and mechanical stress.
differential pressure gauge
In my professional journey, I've encountered numerous instances where improper gauge selection led to failure. One notable case involved a chemical processing unit where incorrect gauge calibration resulted in undetected filter blockages. This incident underscores the importance of regular maintenance and calibration, ensuring that gauges deliver accurate data consistently.
Engaging with the community of manufacturers has allowed me to witness innovations that are enhancing gauge performance. Manufacturers are increasingly incorporating advanced materials and technologies that allow these gauges to withstand high temperature and pressure conditions. Furthermore, the integration of IoT has enabled remote monitoring capabilities, providing real-time updates and predictive maintenance alerts, thus preventing potential downtime and increasing operational efficiency.
In conclusion, selecting the right differential pressure gauge requires a combination of technical expertise and practical experience. It's a decision that impacts not just the efficiency of an industrial process but also its safety and reliability. By ensuring that these instruments are properly maintained and calibrated, industries can harness their full potential, optimizing operations and safeguarding personnel. As advancements continue, I remain confident in the evolving role of differential pressure gauges as pivotal tools in the industrial sector.