Diaphragm pressure gauges are a vital component in various industrial settings, offering precise and reliable measurements crucial for maintaining system integrity and safety. Unlike conventional gauges, diaphragm pressure gauges are designed to measure low-pressure ranges accurately, making them indispensable in sectors such as pharmaceuticals, food processing, and petrochemicals.
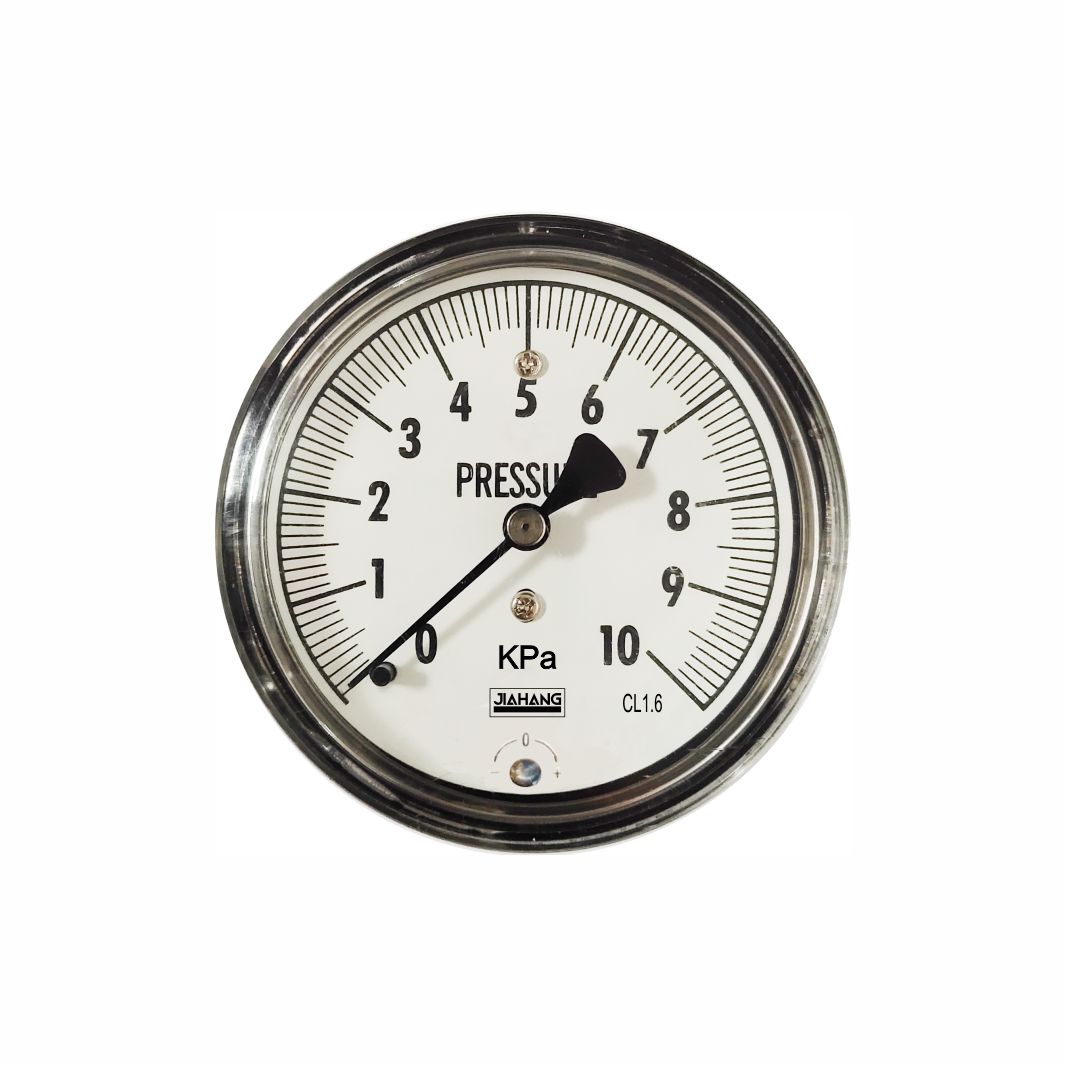
These gauges employ a diaphragm—a thin, flexible membrane—as the primary sensing element. The diaphragm is typically constructed from materials such as stainless steel, Hastelloy, or Tantalum, chosen based on their resistance to specific chemical environments or extreme temperatures. When pressure is applied, the diaphragm deflects, and this mechanical movement is transformed into a readable output via a series of mechanical linkages or electronic sensors.
The standout feature of diaphragm pressure gauges is their ability to measure both absolute and differential pressures with high precision. This makes them ideally suited for applications where even the slightest pressure variance can have significant implications, such as in cleanrooms or when handling corrosive substances.
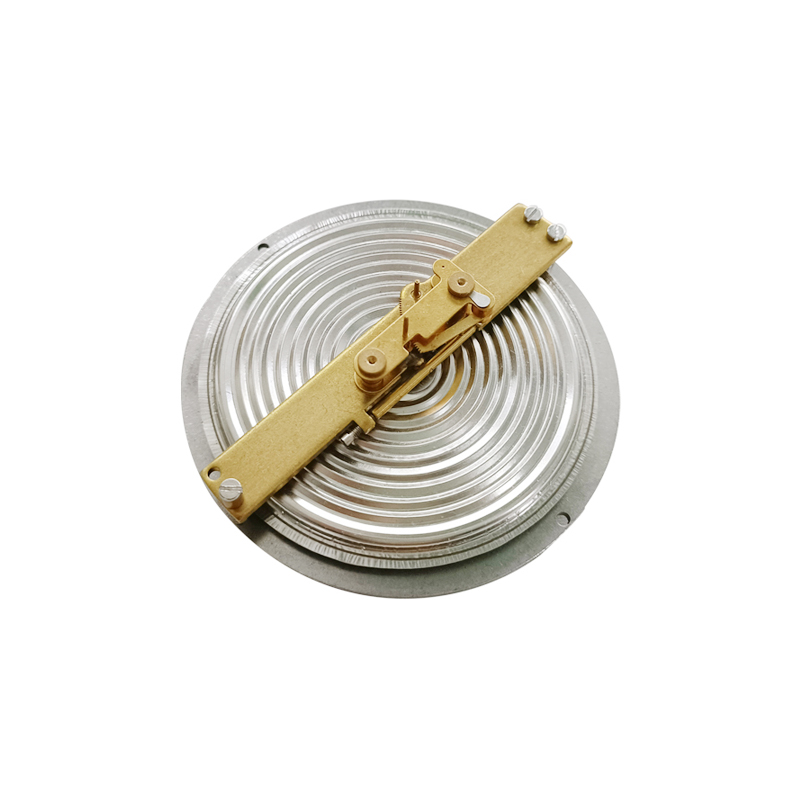
From an expert perspective, selecting the right diaphragm material is crucial to ensure longevity and accuracy. For instance, in a corrosive environment, a diaphragm made of Hastelloy, known for its superior corrosion resistance, might be ideal. On the other hand, for food-grade applications, a stainless steel diaphragm, compliant with hygienic standards, may be more appropriate. Each material has distinct properties that make it suitable for specific conditions, underscoring the importance of tailored solutions in pressure measurement.
pengertian diaphragm pressure gauge
Reliability and accuracy remain at the foreground for professionals utilizing diaphragm pressure gauges. A well-calibrated diaphragm gauge minimizes the risk of equipment failure or process downtime, ensuring that systems operate within their safe parameters. Regular maintenance and calibration, adhering to the manufacturer's guidelines, further boost the credibility and trustworthiness of the readings obtained from these devices.
Moreover, the authority of diaphragm pressure gauges in the industry extends beyond their technical specifications. Manufacturers are often certified by recognized bodies, and adherence to international standards such as ISO or ASME can greatly enhance a gauge's credibility. This certification process not only vouches for the product's quality but also assures users of its reliable performance over time.
From an experiential standpoint, users have reported significant improvements in operational efficiency and safety when employing diaphragm pressure gauges in their processes. The ease of integration and the low maintenance nature of these gauges contribute to their widespread adoption. Users appreciate their robustness and durability, particularly in harsh environments, further cementing their position as a trusted choice in critical applications.
In conclusion, diaphragm pressure gauges represent a harmonious blend of precision, reliability, and adaptability. Whether applied in meticulous laboratory conditions or rugged industrial environments, these gauges offer professionals a dependable tool for maintaining optimal operational standards. Their design evolution, rooted in material science and engineering excellence, continues to empower industries to achieve greater efficiency and safety.