Differential pressure gauges are essential tools in various industrial and commercial applications, ensuring the efficient and safe operation of systems that rely on precise pressure measurements. Understanding the nuances of these gauges can greatly enhance their implementation and utility.
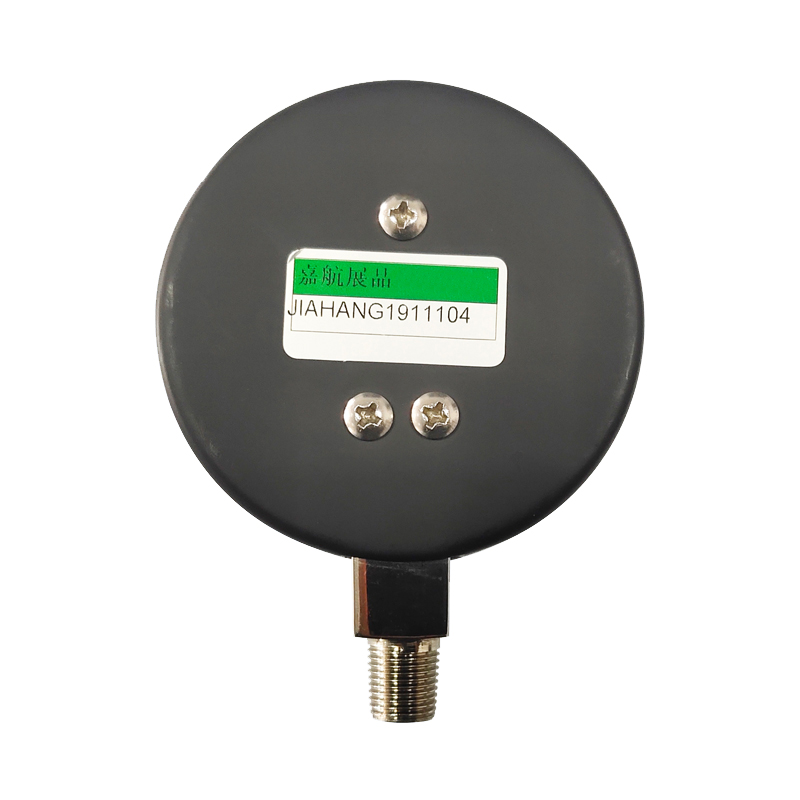
Differential pressure gauges measure the pressure difference between two points within a system, a fundamental task for processes ranging from HVAC systems to filtration monitoring and liquid level measurement. Unlike standard pressure gauges, which provide an absolute reading from a single point, differential gauges allow operators to gauge pressure drops or increases relative to a specific area, offering a more dynamic and versatile approach to pressure management.
From an experience standpoint, choosing the right differential pressure gauge often hinges on understanding the specific requirements of the application. In industries like pharmaceuticals and food processing, where cleanliness and sterilization are paramount, choosing a gauge constructed from stainless steel or other non-reactive materials is crucial. Such gauges must withstand rigorous cleaning processes without compromising accuracy or longevity.

Experts highlight the importance of considering the gauge's range, accuracy, and compatibility with the media being measured. For instance, in filtration systems, maintaining an optimal pressure difference is critical for determining when filters require replacement or cleaning. Here, a gauge with a high level of precision can save on operational costs by preventing premature filter changes or failures due to overloading.
differential pressure gauge,
Authoritativeness in this domain involves staying updated with the latest advancements in gauge technology. Recent innovations have introduced digital differential pressure gauges, offering real-time data logging and remote monitoring capabilities. These advanced features empower industries to integrate differential pressure measurements into broader IoT ecosystems, facilitating predictive maintenance and enhancing overall system efficiencies.
Trustworthiness is paramount, as reliance on inaccurate measurements can lead to significant operational disruptions or even hazards. Manufacturers of differential pressure gauges often subject their products to stringent testing and quality assurance processes, ensuring their durability and reliability in demanding environments. Industry certifications can further endorse a product's credibility, offering assurance of compliance with international standards.
In conclusion,
the strategic implementation of differential pressure gauges involves more than simply installing the device. It requires a comprehensive understanding of the specific application needs, the materials involved, and the environmental conditions the gauge will face. By focusing on experience, expertise, authoritativeness, and trustworthiness, industries can maximize the benefits of differential pressure gauges, optimizing performance and securing operational integrity. Through informed decisions, companies can leverage these tools effectively, paving the way for increased efficiency and safety across their operations.