The construction of OEM differential pressure gauges is a sophisticated process that integrates precision engineering and innovative technology. These instruments are pivotal in numerous industries, including oil and gas, pharmaceuticals, and HVAC systems, where accurate measurement of differential pressure is critical for operational efficiency and safety. The following insights delve into the aspects of experience, expertise, authoritativeness, and trustworthiness that are essential for understanding the construction and functionality of these specialized devices.
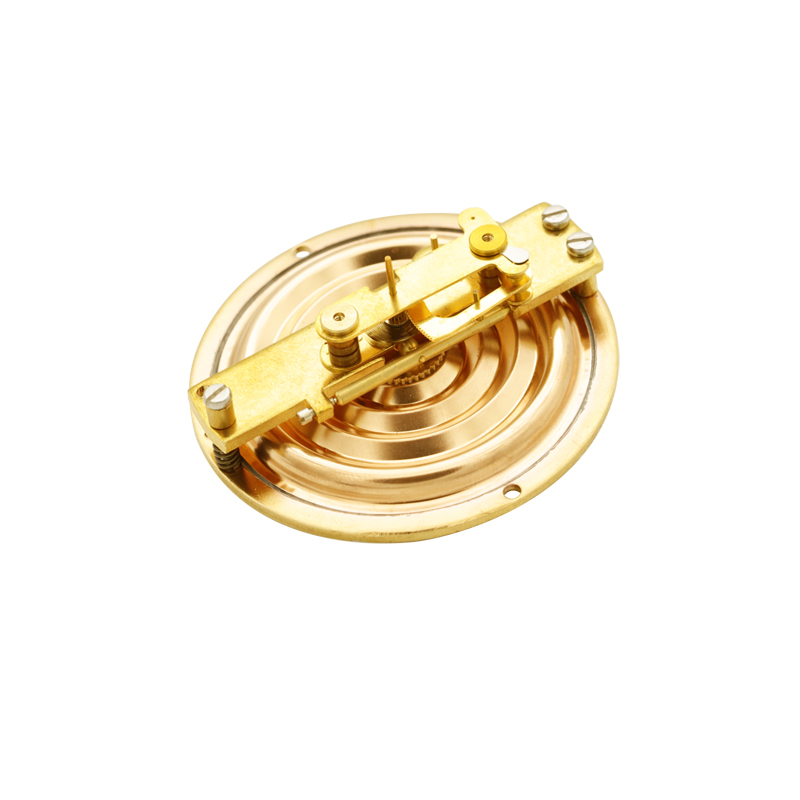
Differential pressure gauges are engineered to measure the difference between two pressure points in a system, with the construction process involving the assembly of highly sensitive components. The selection of materials is vital, often requiring corrosion-resistant metals like stainless steel for the housing and a diaphragm made of flexible yet durable compounds. This choice not only ensures longevity but also precision in environments where pressure fluctuations are frequent.
The expertise involved in building these gauges begins with an intimate understanding of fluid dynamics and mechanical engineering principles. Engineers often leverage computer-aided design (CAD) and finite element analysis (FEA) tools to model and test the resilience of the gauge under different conditions, ensuring that it can withstand potential overpressure scenarios without losing accuracy. This stage is where theoretical knowledge meets practical application, requiring skilled professionals who are adept in both areas.
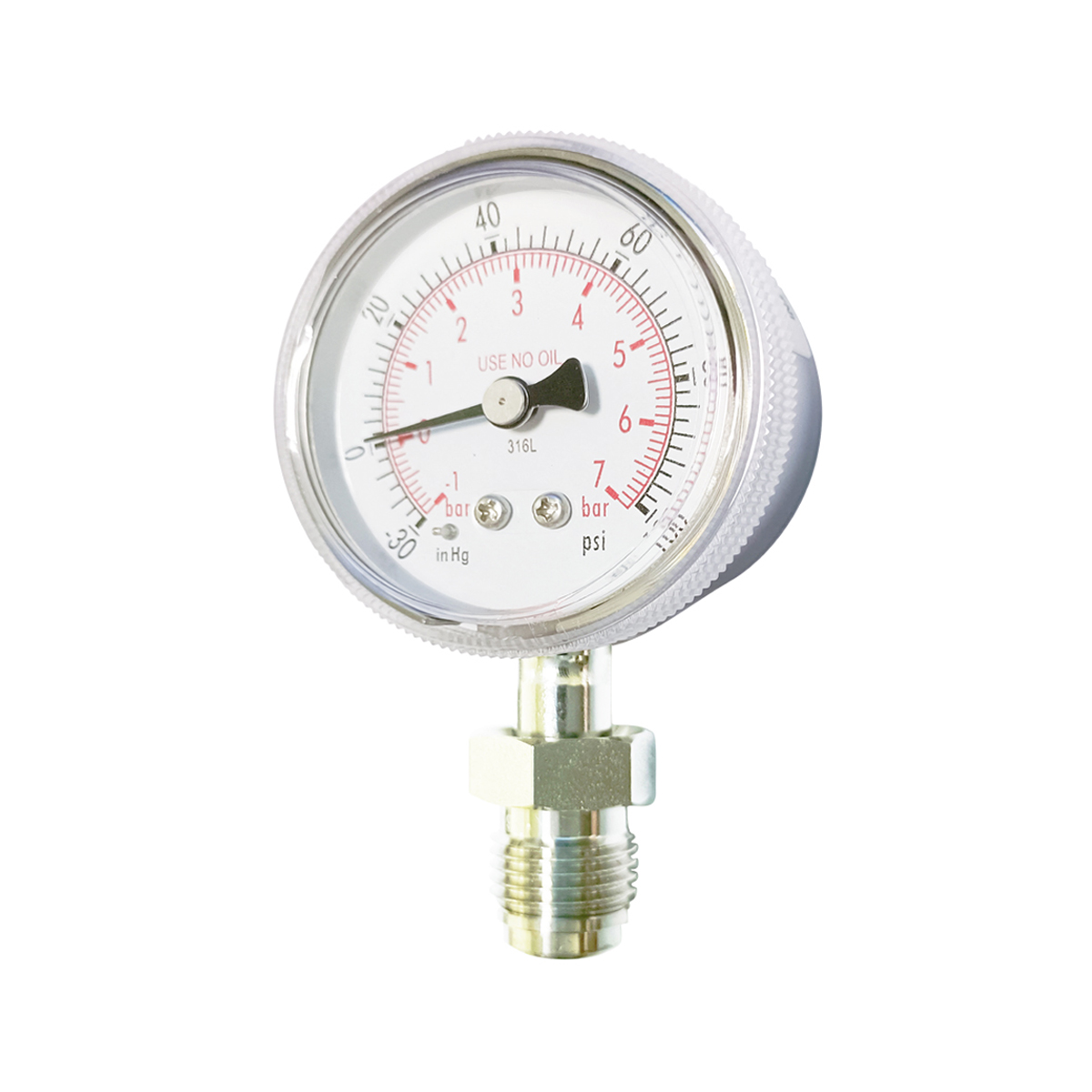
Authoritativeness in the field of OEM differential pressure gauge construction arises from adherence to international standards and industry certifications. Reputable manufacturers develop these instruments in compliance with ISO, ASME, and other relevant standards, which guide the design and performance benchmarks. Such conformity is not merely procedural but is essential in establishing the gauge's reliability and acceptance in global markets.
oem differential pressure gauge construction
Trustworthiness is further reinforced through rigorous testing and quality assurance processes. Each gauge undergoes comprehensive calibration using high-precision equipment to ensure it delivers accurate readings across its operating range. Manufacturers often provide detailed documentation and traceability records, which add an additional layer of confidence for customers. These include calibration certificates, material traceability reports, and quality compliance certificates that verify the gauge's credibility.
Another aspect of trust is the feedback loop from field performance data. Leading firms in the sector engage with clients post-deployment to gather performance statistics and user insights. This approach not only aids in refining future models but also strengthens relationships with stakeholders by showing a commitment to continuous improvement and customer satisfaction.
In summary, the construction of OEM differential pressure gauges is an intricate process that balances experiential learning, engineering expertise, authoritative compliance, and reliable trust-building practices. Companies dedicated to these principles not only produce superior instruments but also ensure these devices meet the demanding needs of critical industry applications. This dedication to quality and precision underscores the importance of selecting a well-established and reputable manufacturer when purchasing OEM differential pressure gauges.