The selection of a high-quality diaphragm material is crucial for optimizing the performance of pressure gauges in various industrial applications. Understanding the intrinsic properties and advantages of superior diaphragm materials can significantly enhance the accuracy, durability, and reliability of pressure measurement systems.
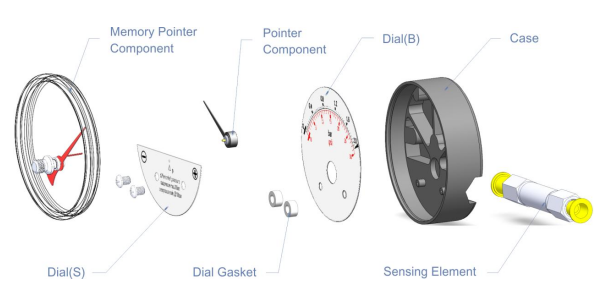
Pressure gauges are indispensable tools in industries such as oil and gas, pharmaceuticals, and food processing. These devices are used to monitor and manage system pressures, ensuring optimal operations and safety. The diaphragm, a key component of these gauges, acts as a barrier between the fluid medium and the pressure measurement component. It must be resilient and efficient in transmitting pressure without deformation or degradation.
A standout diaphragm material used in high-quality pressure gauges is Hastelloy. Known for its exceptional corrosion resistance, Hastelloy is often employed in environments characterized by aggressive chemical compounds. This nickel-based alloy withstands extreme temperatures and maintains its structural integrity, making it an ideal choice for the harshest industrial conditions. Its application in pressure gauges ensures accurate readings and prolonged lifespan of the instruments, thereby reducing maintenance costs and downtime.
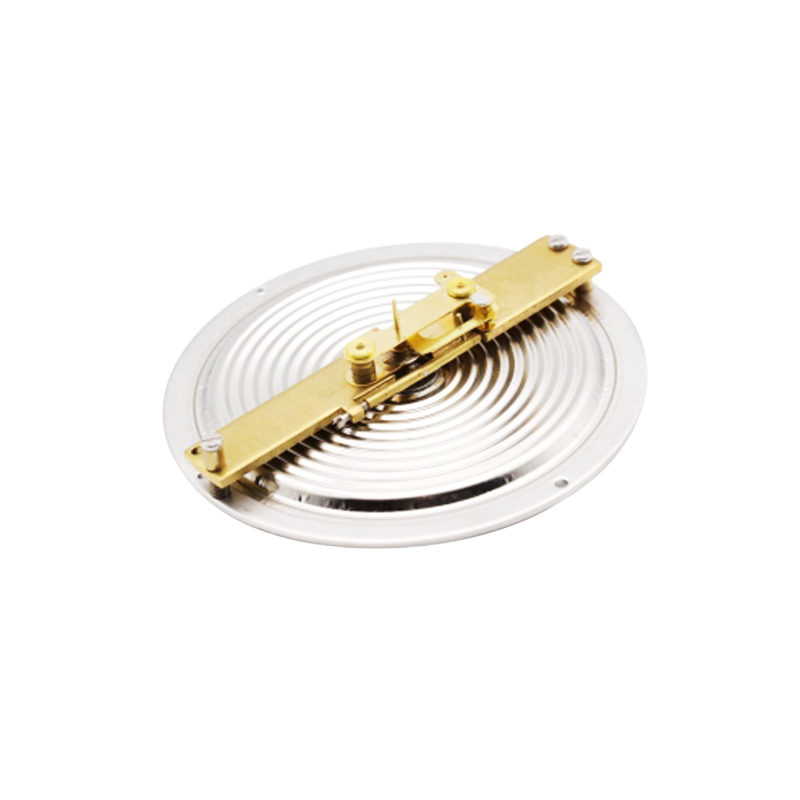
In addition to Hastelloy, PTFE (Polytetrafluoroethylene) is another exemplary diaphragm material. It exhibits remarkable chemical inertness, which is crucial for processes involving reactive or hazardous substances. PTFE possesses a low friction coefficient and can operate effectively across a wide temperature range. This material choice not only protects the pressure gauge from corrosive substances but also minimizes the risk of contamination, making it highly suitable for pharmaceutical and food processing industries.
Correct diaphragm material selection hinges upon understanding the specific requirements of the application. Each material offers distinct characteristics that cater to different operational needs. For example, stainless steel diaphragms are favored in applications that demand mechanical strength under high-pressure conditions, whereas Monel, an alloy of nickel and copper, is preferred in maritime environments due to its resistance to seawater.
high quality diaphragm material pressure gauge
From a long-term operational perspective, investing in pressure gauges with high-quality diaphragms translates to enhanced performance and safety. Products designed with such materials reflect a manufacturer’s expertise and commitment to quality. Companies that consistently utilize top-tier materials enhance their authority and credibility in the marketplace, fostering greater trust with clients and stakeholders.
Moreover, the choice of high-quality diaphragm materials underscores an important aspect of corporate social responsibility. By selecting materials that extend the lifespan of industrial equipment, businesses contribute to environmental sustainability. Lesser need for replacements or repairs reduces resource consumption and waste, aligning with global sustainability goals.
For professionals tasked with selecting pressure measurement systems, a deep dive into diaphragm material technologies can vastly improve decision-making processes. Engaging with manufacturers who prioritize material innovations serves not only to ensure technical superiority but also to forge partnerships grounded in reliability and shared values.
In summary, the intersection of material science and product design plays a pivotal role in the development of pressure gauges that meet contemporary industrial demands. The focus on high-quality diaphragm materials, such as Hastelloy and PTFE, underscores a broader commitment to performance excellence, safety, and sustainability. This approach not only addresses immediate operational needs but also bolsters brand reputation and client trust over the long term. High-quality diaphragms are not mere components but critical factors that elevate the whole pressure measurement system, reflecting a true commitment to engineering excellence.