In the vast realm of industrial instrumentation, the OEM differential pressure gauge stands out as a crucial component, especially when precision and reliability are at stake. Industries such as oil and gas, pharmaceuticals, and manufacturing often hinge on these devices to provide precise measurements that ensure operational efficiency and safety. Yet, the accuracy of an OEM differential pressure gauge can significantly influence the outcome of various processes. Understanding how to evaluate and enhance this accuracy is pivotal for both manufacturers and end-users.

Differential pressure gauges serve a critical role by measuring the difference in pressure between two points within a system. This function is essential for applications such as filtration systems, flow measurement, and liquid level monitoring. The performance of these gauges often dictates the efficiency of the systems they are integrated into. Accuracy in this context is not just about providing correct readings; it's about consistency, reliability, and repeatability under varying conditions.
Firstly,
the design and material choice of an OEM differential pressure gauge are fundamental to its accuracy. Selecting high-grade materials that withstand environmental hazards, such as corrosive elements or extreme temperatures, ensures longevity and precision. For instance, stainless steel is a popular choice due to its resistance to corrosion and ability to maintain integrity under pressure. Alongside materials, the gauge design affects how internal components move in response to pressure changes, impacting the precision of readings.
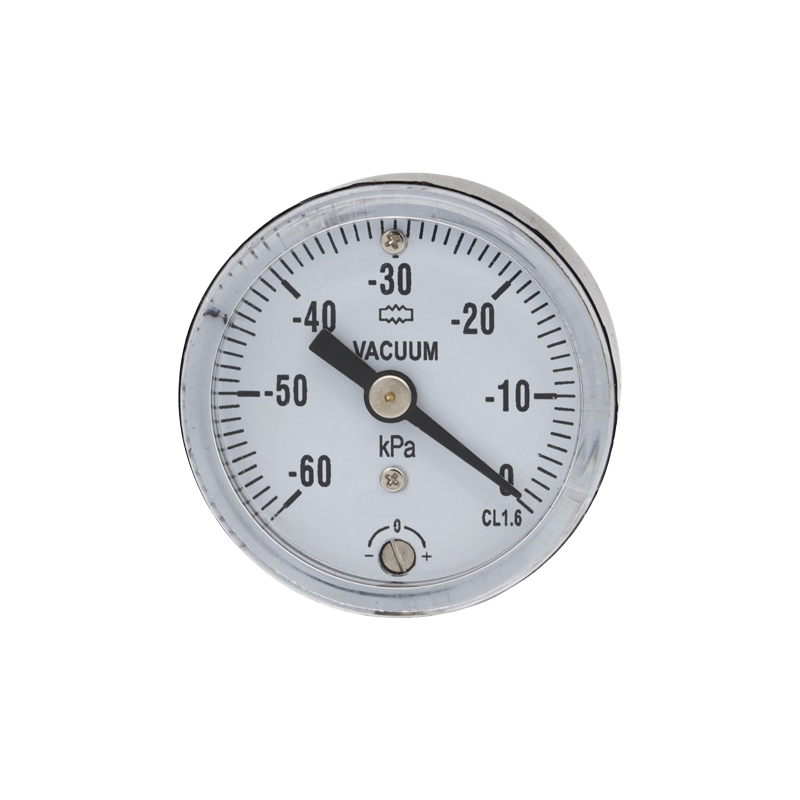
Calibration is another critical factor influencing the accuracy of differential pressure gauges. Regular and precise calibration adjusts a gauge's readings to match known standards, crucial in industries where minuscule deviations can lead to significant errors. Ideally, calibration should be performed in controlled conditions, using traceable standards that align with international benchmarks.
Furthermore, manufacturers must consider the gauge's operational environment. For example, in high-vibration settings, inaccuracies can arise due to mechanical disturbances. In such cases, opting for gauges equipped with dampening features can mitigate the impact of vibrations, preserving measurement accuracy. Similarly, exposure to temperature extremes can cause thermal expansion or contraction in gauge materials, leading to erroneous readings. Hence, integrating temperature compensation mechanisms ensures that gauges provide reliable measurements regardless of thermal fluctuations.
oem differential pressure gauge accuracy
The experience garnered from field use often provides invaluable insights into improving gauge accuracy. Operators can identify recurring issues that may arise in specific applications, such as clogging in filtration systems affecting pressure readings. Incorporating user feedback into design upgrades or maintenance protocols can refine the performance of these gauges.
Trust in OEM differential pressure gauges often stems from rigorous testing and quality assurance processes adhered to by manufacturers. Conducting life-cycle testing under real-world conditions ensures gauges not only meet but exceed accuracy standards over prolonged periods. Quality certifications and adherence to industry-specific standards further bolster user confidence in these devices, indicating a commitment to excellence and reliability.
Lastly, education plays a crucial role in enhancing the trustworthiness and authority of differential pressure gauges. Offering training programs for technicians and operators in the proper installation, maintenance, and troubleshooting of these gauges can substantially reduce errors and enhance measurement accuracy.
In summary, the accuracy of OEM differential pressure gauges is a multifaceted aspect shaped by materials, design, calibration processes, and operational contexts. By prioritizing these elements and committing to quality, manufacturers can provide instruments that not only meet the technical demands of their applications but also earn the trust and reliance of industries worldwide.