Selecting the right OEM pressure gauge, specifically the diaphragm type, requires an in-depth understanding of the product’s application, performance, and reliability. As an industry expert, comprehending these elements ensures the best fit for any given application.
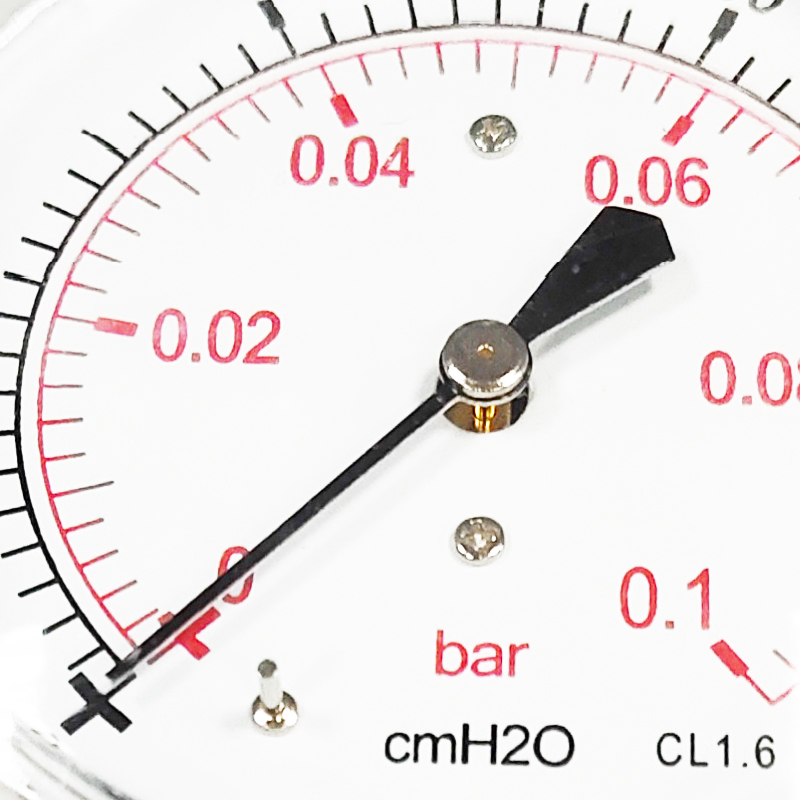
The diaphragm-type pressure gauge distinguishes itself through its robust design and exceptional sensitivity, particularly suitable for applications involving aggressive, corrosive, or viscous media. Unlike traditional pressure gauges, diaphragm variants offer superior protection against environmental factors, ensuring long-term durability and precise measurements.
The diaphragm mechanism uses a flexible membrane, typically made from materials such as stainless steel, Hastelloy, or Tantalum, to convert pressure into readable metrics. This flexibility allows the diaphragm to accommodate pressure fluctuations while maintaining consistent accuracy.
When the pressure is exerted on the diaphragm, it deflects. This deflection is translated into a rotary motion driving the gauge pointer, providing a reading of the pressure level.
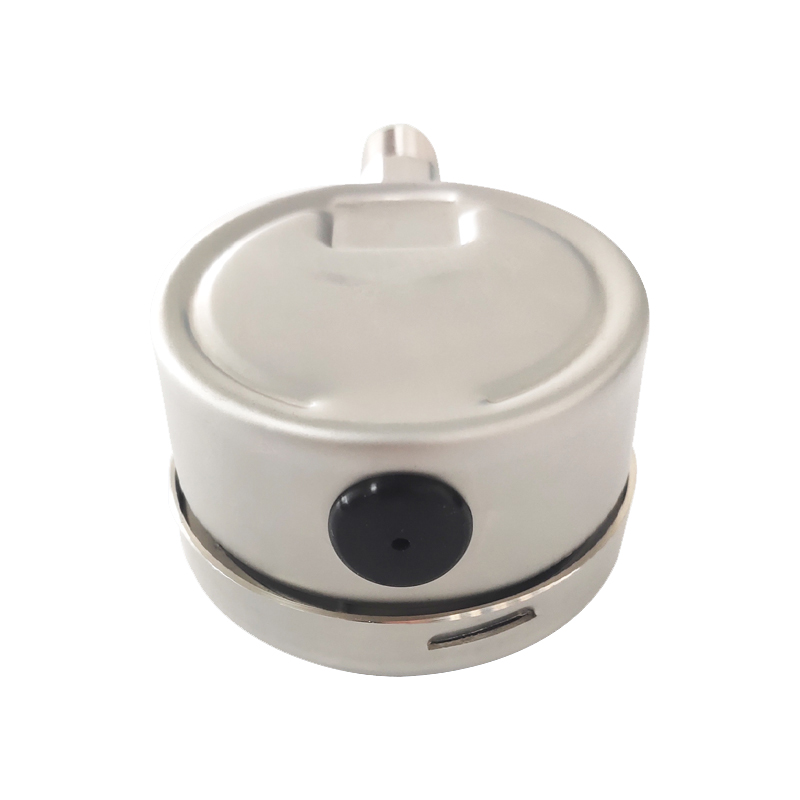
Key to its performance is the material choice for the diaphragm. High-grade materials result in enhanced resistance to chemical exposure and temperature variations, making it a versatile choice for industries like pharmaceuticals, food and beverage, and petrochemicals, where sterile and hygienic conditions are mandatory.
In practice, selecting the appropriate diaphragm-type gauge involves a thorough assessment of several parameters
1. Media Compatibility Ensuring the diaphragm material is compatible with the media in use is imperative. In situations involving highly corrosive substances, a diaphragm made of Tantalum or PTFE may be necessary to avoid degradation and ensure continued accuracy.
2. Pressure Range Gauges must be selected according to the operational pressure range of the application. Choosing a gauge with an inappropriate range can compromise both accuracy and safety.
oem pressure gauge diaphragm type
3. Temperature Considerations Diaphragm pressure gauges should be matched to the thermal conditions of the application environment. High temperatures require diaphragms that can withstand thermal expansion without losing integrity or precision.
4. Mounting Configurations Various mounting options like direct, remote, or panel mounting are available. The choice here depends on the specific application requirements, including space limitations and visibility needs.
5. Regulatory Standards Compliance with industry standards such as ANSI, ASME, or ISO is vital to ensure accuracy, safety, and reliability. A gauge that meets these standards is a testament to its quality and trustworthiness.
End-users and specifiers should also consider factors like maintenance needs and calibration intervals. A diaphragm-type pressure gauge, due to its design, often requires less maintenance compared to its counterparts, ensuring reduced downtime and longer service intervals.
Establishing a strong partnership with the OEM supplier also plays a crucial role in the selection process. A reputable manufacturer provides not only a high-quality product but also supports it with technical advice and after-sales service, further enhancing the reliability and trustworthiness of the gauge in its operational environment.
OEM pressure gauge diaphragm types, with their specialized designs and reliable performance characteristics, are indispensable in situations where precision and durability cannot be compromised. By focusing on these attributes, industries can achieve superior process control, leading to improved operational efficiency and safety across the board.