In the realm of industrial instrumentation, the diaphragm capsule pressure gauge stands out as a precise and reliable tool crucial for various applications. Its design and functionality cater primarily to environments where safety, accuracy, and consistency are paramount. This article explores the indispensable features and empirical insights associated with using diaphragm capsule pressure gauges, emphasizing their relevance across diverse sectors.
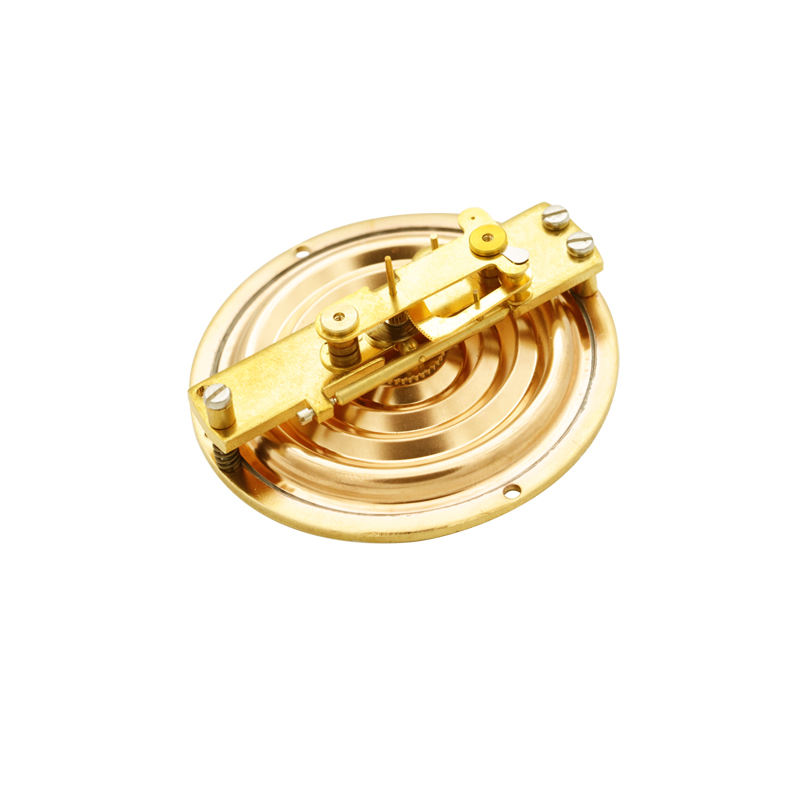
The diaphragm capsule pressure gauge emanates authority in measuring low-pressure ranges, essential in industries like chemical processing, pharmaceuticals, and food and beverage. Unlike conventional pressure gauges, the diaphragm capsule variant is engineered to handle lower pressures with heightened sensitivity. This specialized capability is attributable to the flexible diaphragm connected to a capsule. When pressure is applied, the diaphragm deforms, and this displacement is translated into a proportional movement on the gauge, providing an accurate reading.
Understanding the technical advantages of a diaphragm capsule pressure gauge highlights its expertise. It features a robust construction, typically using materials such as stainless steel, Inconel, or Hastelloy, which ensures resilience in corrosive environments. The choice of material is crucial, as it upholds the device's longevity and reliability. These gauges are also designed to meet stringent industry standards, underpinning their credibility in high-stakes applications.
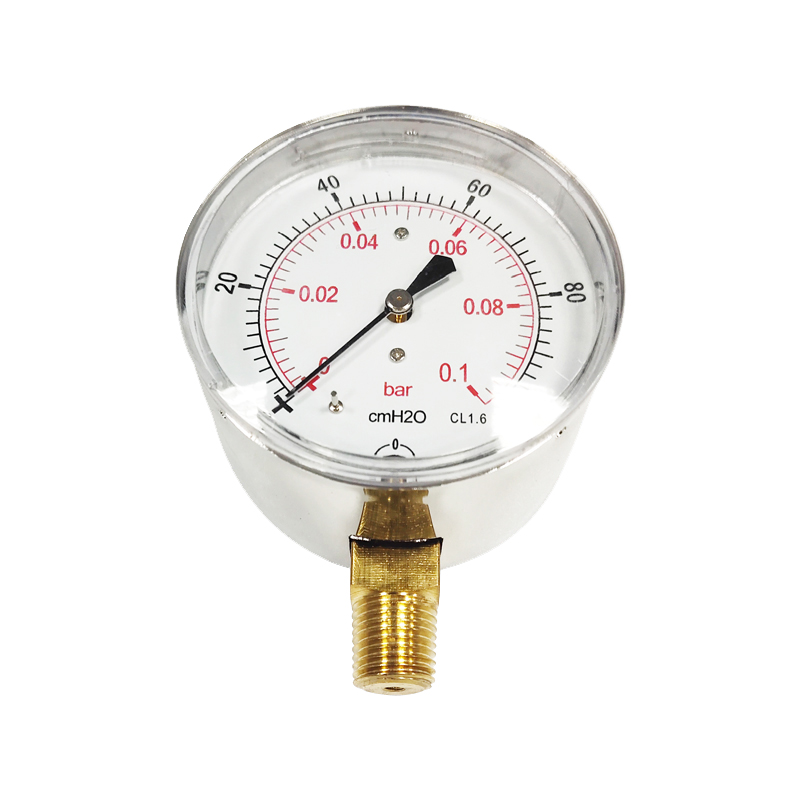
Real-world experience suggests that employing diaphragm capsule pressure gauges can significantly mitigate risk. In chemical plants, for example, where pressure measurements can prevent hazardous leaks, these gauges offer peace of mind. Operators report reduced downtime and maintenance costs, attributing this to the gauge’s non-invasive nature and resistance to contamination. The diaphragm serves as a barrier protecting the measuring element from the process media, ensuring both precision and the integrity of the measurement.
diaphragm capsule pressure gauge,
Moreover, for operations involving hygienic processes in food and beverage sectors, these gauges ensure that there is no cross-contamination. The simplicity of cleaning the diaphragm further enhances their suitability in these environments, where strict adherence to cleanliness standards is mandated.
From an expertise perspective, proper installation and calibration of diaphragm capsule pressure gauges are critical. Professionals emphasize the importance of positioning the gauge correctly to avoid errors due to gravity or improper alignment. Calibration should be routinely done, aligning the gauge's readings with known pressure standards to maintain its accuracy over time. Expert technicians recommend partnering with certified providers for these services, ensuring that the equipment functions optimally within the expected parameters.
Acknowledged by industry leaders for their trustworthiness, diaphragm capsule pressure gauges are staples in sectors where precision is not just desired but essential. They convey authenticity through their consistent performance record and are venerated for their robustness in challenging scenarios. Integrating these gauges into operational processes represents a commitment to quality and safety, aligning with industry best practices and regulatory compliance.
In conclusion, whether in handling delicate chemical reactions or guaranteeing the purity of consumable products, the diaphragm capsule pressure gauge is revered for its unparalleled reliability and accuracy. Its application not only underscores operational excellence but also embodies a commitment to safety, efficiency, and best practices in measurement technology. As industries evolve, the continued reliance on diaphragm capsule pressure gauges reaffirms their indispensable role in modern industrial operations.