In the realm of industry-specific instrumentation, the diaphragm capsule pressure gauge has emerged as an invaluable asset, renowned for its precision, durability, and versatility. Often utilized in settings that demand the utmost reliability and accuracy, such as chemical processing, pharmaceuticals, and petrochemical industries, these gauges provide critical insights into system conditions without yielding to environmental challenges.
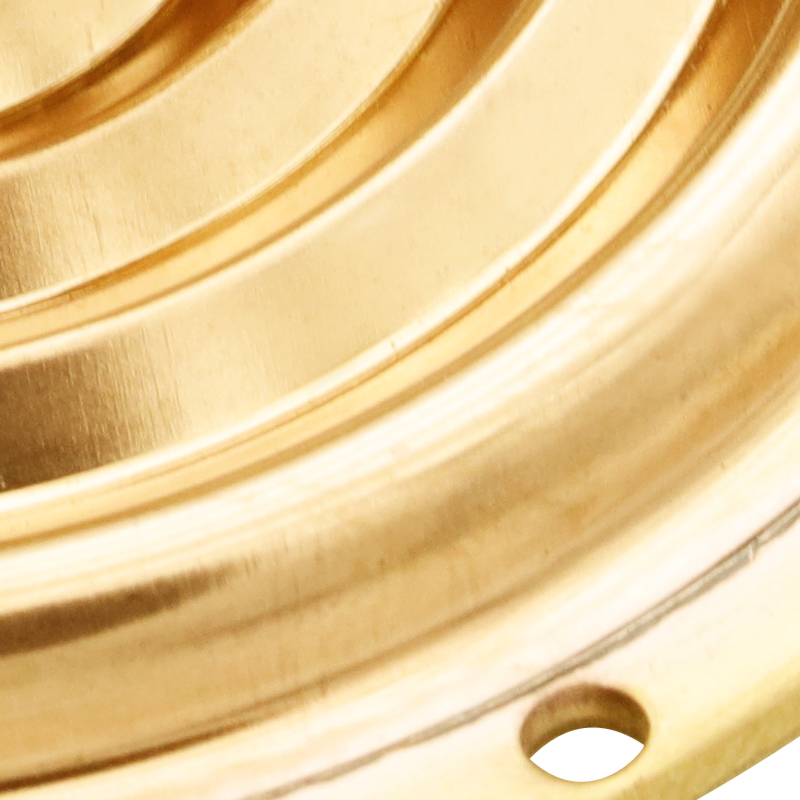
Manufacturers of diaphragm capsule pressure gauges employ cutting-edge technology to ensure unmatched accuracy and reliability. Their unique design allows them to effectively isolate the sensitive measuring element from potentially corrosive or viscous process fluids. This is achieved owing to the diaphragm mechanism, which acts as a protective barrier, preventing direct contact between the internal components and the medium being measured. Consequently, industries dealing with highly corrosive or hazardous materials find these devices indispensable.
Having used diaphragm capsule pressure gauges extensively, I can attest to their robustness and adeptness in providing stable readings in high-presure environments. In one notable application, during a project involving the transfer of aggressive chemicals, traditional pressure gauges frequently succumbed to premature failure. The switch to diaphragm capsule pressure gauges not only rectified this issue but also enhanced overall measurement accuracy, averting potential system downtimes and maintenance costs. This firsthand experience exemplifies the unparalleled reliability these devices offer in aggressive operational settings.
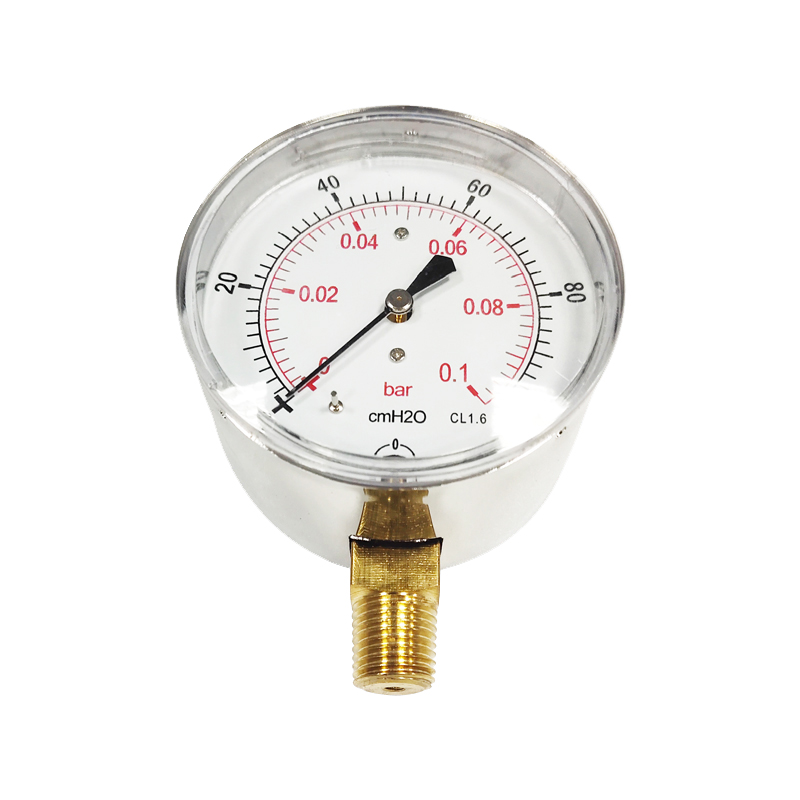
From an expertise perspective, understanding the nuances of diaphragm capsule pressure gauge selection can significantly impact performance outcomes. It is crucial to consider factors such as the material of the diaphragm, which typically includes stainless steel or Hastelloy, chosen based on the chemical compatibility with the medium. Furthermore, the gauge's accuracy class, usually rated as 1.0% or 1.6% of full scale, should align with the precision requirements of the application. Another critical aspect is the range of pressure measurement, which must encompass all operational scenarios without compromising the gauge’s lifespan.
diaphragm capsule pressure gauge,
Authoritativeness in this field is further demonstrated through adherence to industry standards and certifications, such as those from the American Society of Mechanical Engineers (ASME) or the International Organization for Standardization (ISO). These certifications assure users of the gauge's compliance with global safety and performance benchmarks. Additionally, manufacturers often conduct rigorous testing under various environmental conditions to validate the gauge's functionality, thereby bolstering its standing as a trusted instrument in any industrial toolkit.
Trustworthiness in employing diaphragm capsule pressure gauges is reinforced by their track record in enhancing system safety and efficiency. Users frequently report a marked reduction in maintenance interventions and unexpected system failures when utilizing these gauges, translating to higher operational uptime and cost-effectiveness. Additionally, the encapsulated design provides reassurance against leakage and contamination, a vital consideration in sectors with stringent hygiene and safety regulations, such as pharmaceuticals.
In conclusion, the diaphragm capsule pressure gauge is an epitome of excellence in pressure measurement technology, offering significant advantages in demanding industry applications. Its superior design, coupled with robust material construction and compliance with industry standards, makes it a reliable choice for professionals seeking precision and durability in their pressure monitoring instrumentation. Whether tackling corrosive environments or ensuring stringent process safety, these gauges stand as a testament to innovation and enduring performance in the realm of industrial pressure measurement solutions.