Differential pressure gauges play a pivotal role in hydraulic systems, ensuring efficiency and reliability. With technological advancements, these gauges have become indispensable tools for engineers and technicians alike. Their ability to measure pressure differential across components in a hydraulic system allows for optimization and error detection, contributing significantly to system upkeep and performance.

Why are differential pressure gauges essential in hydraulics? At the core, hydraulic systems rely on fluid flow and pressure to function. Any disruptions, whether caused by clogging or component failure, can drastically affect operational efficiency. Differential pressure gauges provide real-time data that can signal potential issues long before they lead to catastrophic failures. This capability enhances system reliability by enabling timely maintenance, reducing downtime, and ultimately saving costs.
From an expert standpoint, selecting the right differential pressure gauge is crucial. The wide variety of available gauges caters to distinct system requirements. Key factors to consider include the range of pressure the system operates within, the fluid type, and the environmental conditions it will face. For instance, a system exposed to corrosive environments may require a gauge with special material coatings to withstand degradation, ensuring longevity and accurate readings.
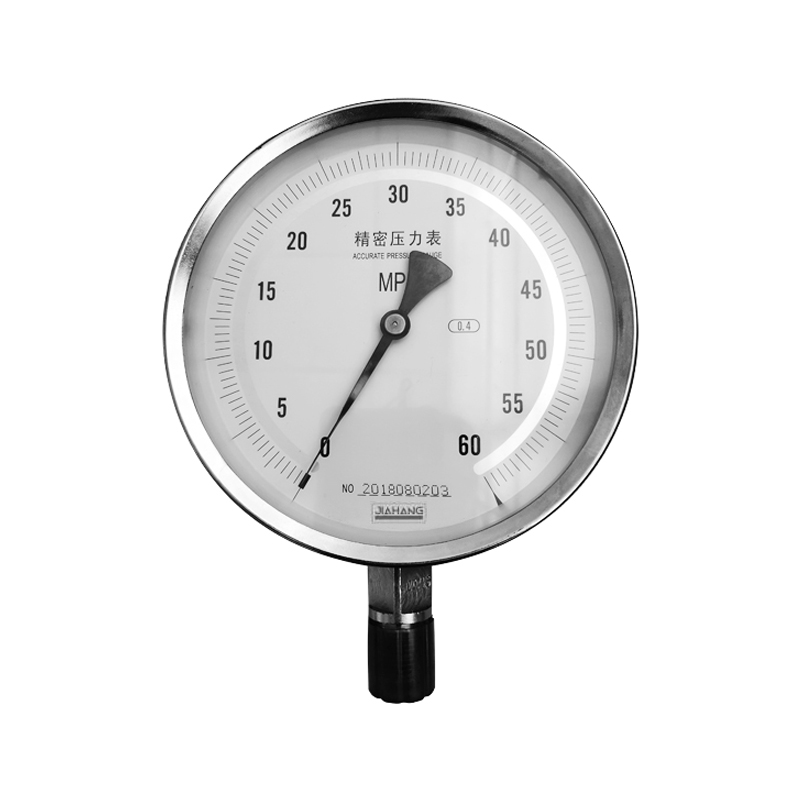
Authoritative insights also highlight the importance of gauge placement within a hydraulic system. Proper positioning ensures that accurate pressure differentials are recorded, allowing for effective monitoring and diagnostics. Placing a gauge directly across filters, for example, can instantly inform operators about filter condition, determining whether it's clean or nearing the end of its life cycle. This kind of monitoring is essential for maintaining optimal fluid cleanliness, which is critical for the longevity of pumps and other components.
differential pressure gauge hydraulic
Moreover, from a trustworthiness angle, the integration of digital and smart differential pressure gauges into hydraulic systems has transformed monitoring capabilities. These digital variants offer greater precision and can be integrated into broader automated systems for real-time condition monitoring. Entrepreneurial companies leading innovation in this sector have developed gauges with wireless communication capabilities, allowing remote monitoring and analysis that can further enhance system oversight and maintenance efficiency.
User experiences consistently affirm the value of high-quality differential pressure gauges. By providing peace of mind and actionable insights, these tools empower technicians to make informed maintenance decisions with a high degree of accuracy. Users have noted that a dependable differential pressure gauge often results in fewer system failures, better overall system health, and significant long-term savings.
In closing, the differential pressure gauge is not just a component but rather an essential instrument for maintaining hydraulic systems' health and efficiency. Leveraging real-world experience, authoritative engineering advice, and cutting-edge innovations ensures that any hydraulic system under your care operates at peak performance. As hydraulic systems continue to evolve with new technologies and capabilities, the adaptable nature of differential pressure gauges will undoubtedly play a significant role in shaping the future of hydraulic engineering.