In the ever-evolving landscape of precision instruments, the high-quality digital diaphragm pressure gauge stands out, epitomizing the fusion of cutting-edge technology and meticulous engineering. This compact yet powerful device is essential in industries demanding rigorous monitoring of pressure variations with unwavering accuracy. With years of experience navigating the intricacies of digital measurement solutions, I can confidently attest to the transformative impact these gauges have on various sectors, from pharmaceuticals to aerospace engineering.

Designed to measure both vacuum and pressure accurately, digital diaphragm pressure gauges leverage a sensitive diaphragm as their primary sensing element. When integrated into automated systems, these devices offer unparalleled reliability. Their digital interface facilitates real-time data acquisition, drastically reducing human error compared to analog counterparts. This precision is indispensable in applications where even the slightest deviation in pressure can lead to catastrophic outcomes, such as in pharmaceutical manufacturing where sterility and exact measurement are non-negotiable.
The distinguishing feature of high-quality digital diaphragm pressure gauges is their construction. Utilizing robust materials such as stainless steel and advanced polymers, these gauges are equipped to withstand harsh environmental conditions, including extreme temperatures, chemical exposure, and mechanical shocks. Expertise in materials science and industrial design ensures that these gauges not only maintain accuracy but also boast longevity, effectively reducing long-term operational costs.
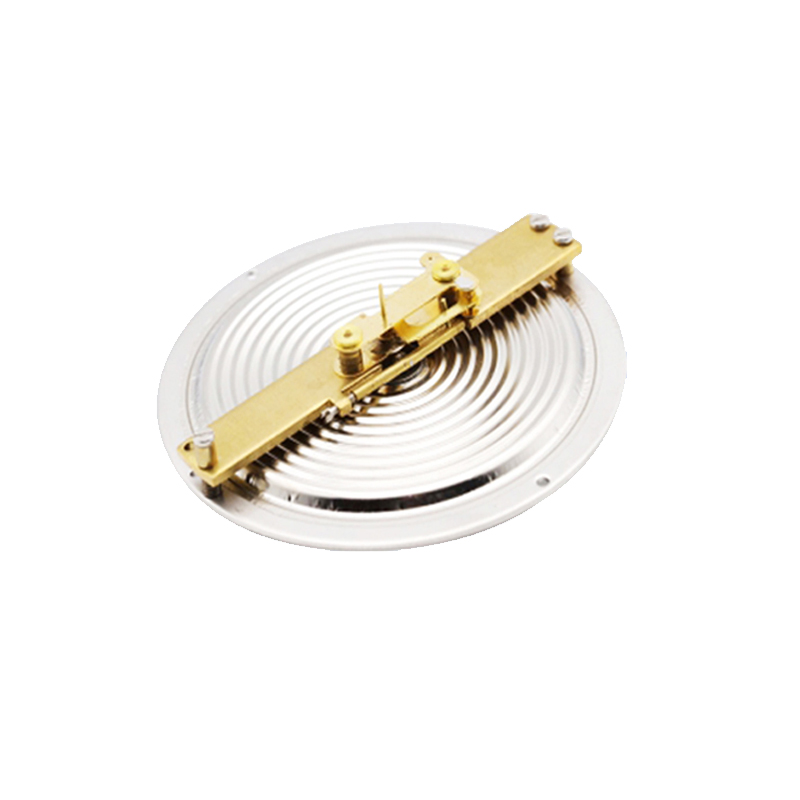
Furthermore, proprietary calibration algorithms enhance their authoritativeness. Unlike conventional gauges, these devices undergo rigorous calibration processes, adhering to international standards like ISO and ASME. This process involves simulating various pressure scenarios to ensure the device's response is precise across its entire operating range. Manufacturers, who are industry leaders with decades of expertise, often back these gauges with certifications and annual calibration reminders, cementing their trustworthiness in the eyes of quality assurance engineers.
Intuitive user interfaces further augment the usefulness of digital diaphragm pressure gauges. Advanced models feature touch-screen displays, data logging capabilities, and connectivity options such as Bluetooth or Wi-Fi. These enhancements facilitate seamless integration into existing digital ecosystems, allowing for remote monitoring and predictive maintenance. Engineers and operators can access data from multiple gauges in real-time, orchestrating more informed decision-making processes.
high quality digital diaphragm pressure gauge
The authority of these sophisticated tools is backed by case studies highlighting their successful deployment in critical environments. For instance, the aerospace industry relies heavily on these gauges during the testing phases of engine components. When subjected to high-pressure environments, engine parts are monitored for stress responses. The real-time feedback provided by high-quality digital diaphragm pressure gauges ensures that engineers can make immediate adjustments, thus preventing costly delays in production schedules.
On the other hand, the chemical industry's demand for reliability is equally met by these devices. In chemical processing plants, pressure gauges monitor the integrity of pipelines carrying volatile substances. A minute leak may be detected by the sensor's diaphragm, setting off alarms before catastrophic failures occur. Such real-world applications validate the trustworthiness of these gauges in mission-critical tasks.
Credibility is further asserted through transparent product development processes and customer feedback loops. Leading manufacturers actively engage with users, incorporating their experiences to refine design aspects. This aligns with industry standards and demonstrates a commitment to continuous improvement. User testimonials often highlight transformative changes in operational efficiency and safety after adopting these gauges, consolidating trust in their performance.
Innovation does not remain static; as technology evolves, so too do the capabilities of high-quality digital diaphragm pressure gauges. The current trend focuses on reducing power consumption while enhancing sensor resolution, a testament to the ongoing dedication to meet and exceed customer expectations. Collaborations between academic institutions and R&D departments of gauge manufacturers continue to push the boundaries of what is possible, keeping these devices at the forefront of digital measurement technology.
In summary, high-quality digital diaphragm pressure gauges are indispensable assets in the realm of precision measurement. Their engineered perfection, authoritative accuracy, and integration capabilities make them vital across various sectors. As industries advance towards automation and data-driven decision-making, these gauges remain a testament to innovation and reliability, earning unwavering trust from engineers and industry leaders alike.