When embarking on selecting a high-quality high pressure differential pressure gauge, understanding the intricacies of the product can significantly influence decision-making and operational efficiency. As a cornerstone in precision measurement within industrial settings, these gauges deserve an in-depth exploration to distinguish superior options that amalgamate performance with durability.
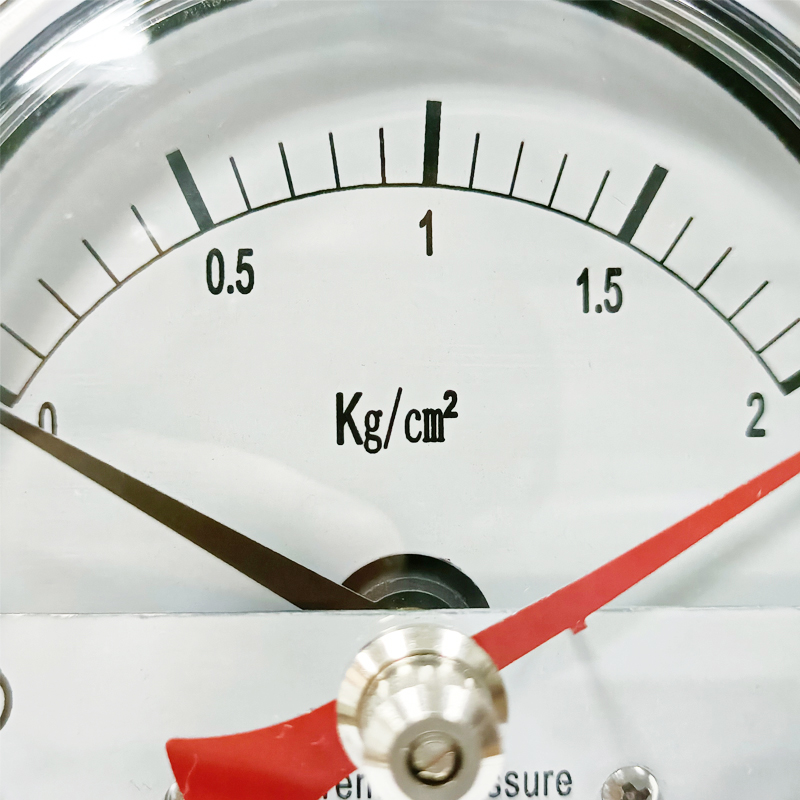
In the realm of industrial application, pressure differential gauges hold esteem for their ability to discern pressure disparities between two points. This capability is critical for systems where fluid dynamics and pressure consistency dictate operational integrity. Selecting a high-quality instrument is imperative for ensuring not only performance but also safety and longevity of the machinery involved.
Expertise in the engineering behind these gauges reveals a focus on materials that withstand harsh conditions, including corrosive environments and extreme temperatures. Typically, the casing might be constructed from robust stainless steel, designed to resist environmental degradation. The internal mechanisms often include advanced ceramics or hermetically sealed components that ensure sensitivity and accuracy even under constant exposure to operational stressors.
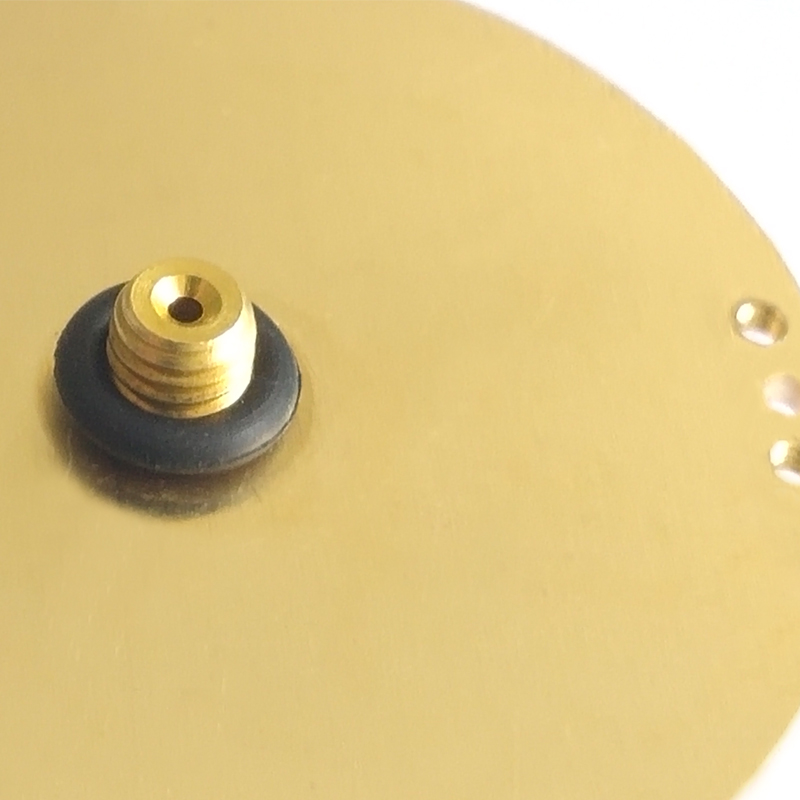
Beyond materials, the technological sophistication of sensors within these gauges enhances measurement precision. Many top-tier models incorporate micro-electromechanical systems (MEMS) technology, delivering unparalleled accuracy. These sensors can detect minute changes in pressure, which is invaluable for processes requiring exacting standards.
From an authoritative perspective, certification and adherence to international standards such as ISO 90012015 for quality management are vital identifiers of reliability. These certifications guarantee that the gauge not only meets industry norms but is also dedicated to continuous improvement.
high quality high pressure differential pressure gauge
Furthermore, trustworthiness in these products is underpinned by rigorous testing protocols.
High-quality pressure differential gauges undergo extensive calibration procedures to ensure precision from the get-go. Over time, recalibration services provided by reputable manufacturers are indicative of their commitment to maintaining gauge accuracy, reinforcing customer trust.
User experience represents another dimension of differentiation in high-quality gauges. Ease of installation, intuitive interfaces, and compatibility with existing monitoring systems simplify integration. Feedback mechanisms, such as digital outputs or user-friendly displays, can further enrich the operator's interaction with the equipment, minimizing error and maximizing efficiency.
Industry-specific insights delve deeper into sector applications; for instance, in petrochemical industries, reliability under high pressure is non-negotiable due to the high-risk environment. Alternatively, in the HVAC sector, precision gauges optimize energy efficiency and system outputs. Thus, understanding contextual applications not only highlights the gauge's versatility but also underscores its indispensable role across diverse industries.
When reviewing peer reviews and expert testimonials, consistent performance and positive operational reports bolster a gauge’s standing. A history of successful deployments and endorsements by industry veterans add a layer of credibility that can significantly influence purchase decisions.
In conclusion, the merits of a high-quality high pressure differential pressure gauge are defined by a confluence of materials science, cutting-edge technology, rigorous standards compliance, and customer-centric design. While the initial investment may be considered higher, the return through operational excellence, safety enhancements, and sustainable performance deem it a prudent choice for any forward-thinking industrial entity.