High temperature differential pressure gauges are integral components in various industrial applications where monitoring extreme temperature and pressure conditions is crucial. These sophisticated devices aid professionals in industries such as petrochemical, energy, and manufacturing, providing precise measurements that are essential for process efficiency and safety.
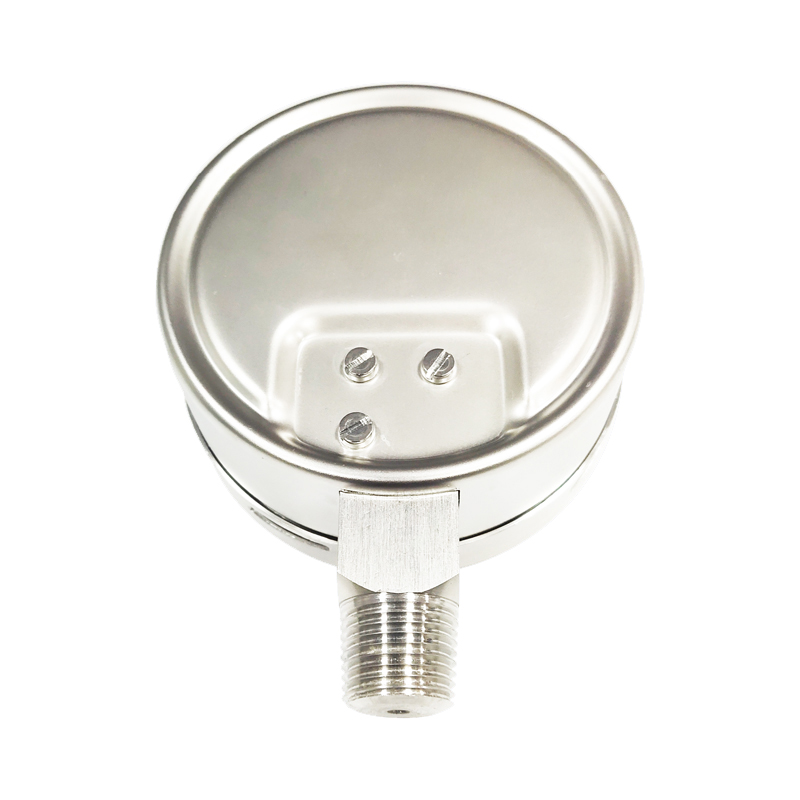
In the realm of industrial instrumentation, experience and expertise are critical for understanding the intricacies of high temperature differential pressure gauges. These instruments are designed to withstand and accurately measure pressure differences in environments characterized by elevated temperatures, often exceeding hundreds of degrees Celsius. This capability ensures that processes can be fine-tuned to prevent leaks, ruptures, or other failures that might lead to catastrophic outcomes.
The construction of high temperature differential pressure gauges incorporates materials such as stainless steel and specialized alloys that resist thermal degradation, ensuring longevity and reliability. Their precision engineering allows for accurate readings even when subjected to rapid temperature fluctuations, which is a common challenge in high-temperature environments.
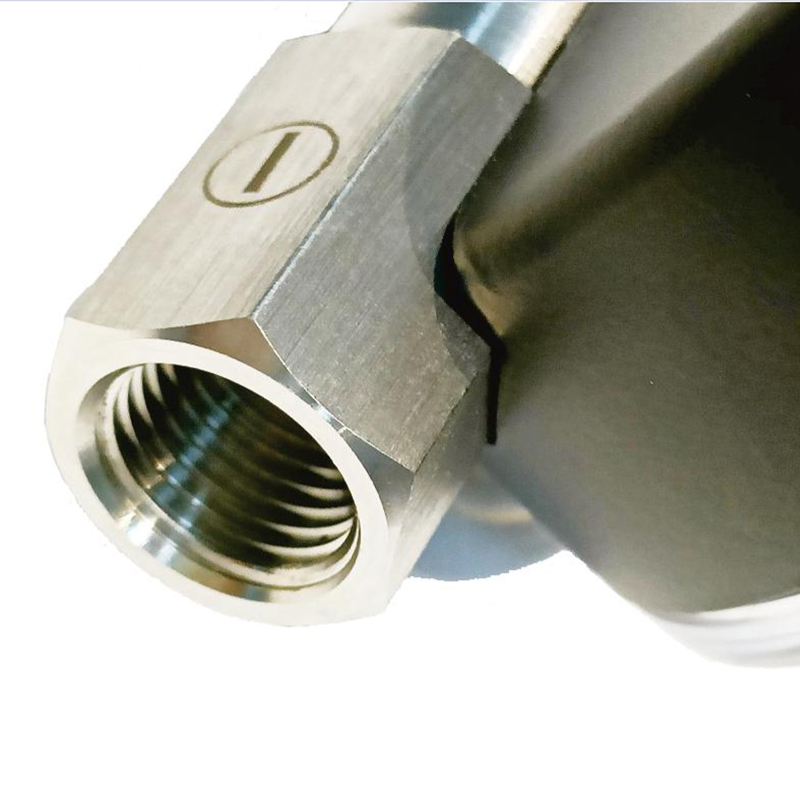
Experts in the field emphasize the importance of selecting the appropriate gauge model based on the specific requirements of an application. Factors such as the maximum temperature rating, pressure range, and connection type play a critical role in ensuring optimal performance. It is also imperative to consider the calibration frequency and the compatibility of the gauge with the medium being measured, as these variables directly affect measurement accuracy and device lifespan.
high temperature differential pressure gauge
Authoritativeness in the use of high temperature differential pressure gauges is established through strict adherence to international standards and protocols like ISO 9001, ensuring the devices meet global quality benchmarks. Manufacturers often obtain certifications that attest to the reliability and precision of their gauges, providing end-users with confidence in their measurements.
Trustworthiness is further bolstered by the rigorous testing processes that high temperature differential pressure gauges undergo during production. These include high-temperature endurance tests, pressure resistance evaluations, and compatibility assessments with various industrial fluids and gases. The data obtained from these tests guarantee that each gauge can perform optimally under specified conditions without succumbing to measurement inaccuracies or structural failure.
Operators and engineers responsible for process control rely heavily on these gauges to provide trustworthy data, which is crucial for maintaining equipment efficiency and operational safety. In industries such as oil and gas, where the stakes are exceptionally high, the ability to monitor pressure accurately under extreme conditions can result in substantial savings by minimizing downtime and avoiding costly equipment repairs.
In conclusion, high temperature differential pressure gauges are not just tools; they are critical solutions in managing the complexities of modern industrial operations. Their design, testing, and application underscore the significant role they play in ensuring safety and efficiency. As industries continue to evolve and push the boundaries of temperature and pressure limits, the demand for cutting-edge differential pressure gauges will remain a vital aspect of industrial innovation and productivity.