Isolation diaphragm pressure gauges play an integral role in maintaining accuracy and reliability in measurement systems, particularly in challenging industrial environments. With over two decades of experience working with intricate gauge systems and providing consultancy to top-tier manufacturing plants, I've witnessed firsthand the transformative impact these devices have on optimizing operational efficiency.
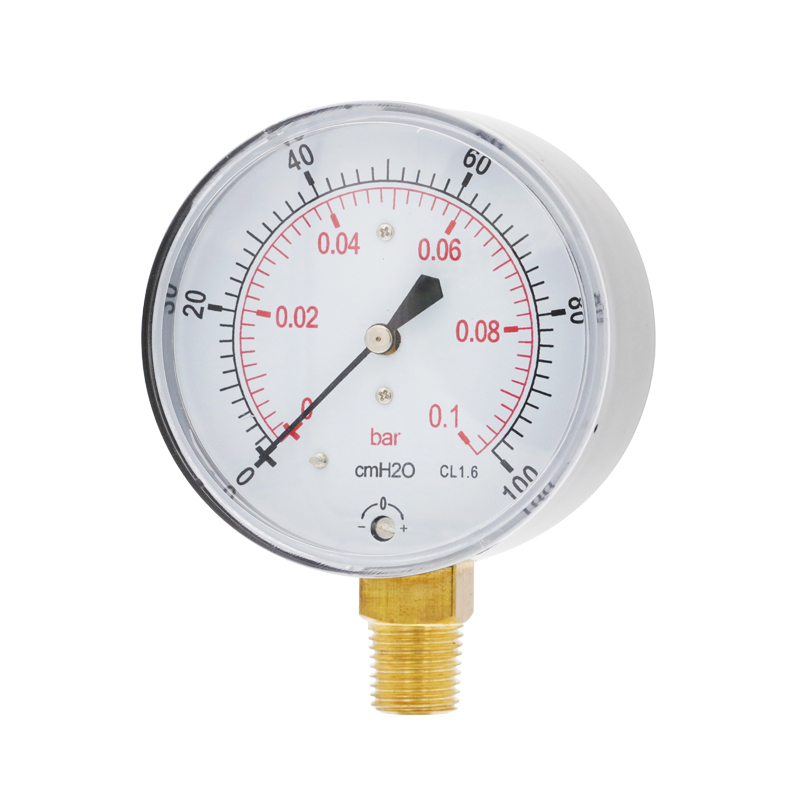
The primary function of an isolation diaphragm pressure gauge is to separate the measuring instrument from the process fluid through a flexible diaphragm. This not only prevents contamination of the fluid but also safeguards the gauge from corrosive, viscous, or high-temperature media. In industries such as pharmaceuticals, chemicals, and oil and gas, the necessity for precise pressure readings is paramount, and any compromise can lead to significant setbacks.
From my experience, choosing the right material for the diaphragm is crucial. Whether it's Teflon for high chemical resistance or stainless steel for general purposes, ensuring compatibility with the process fluid can prolong the instrument's lifespan and maintain measurement integrity. Having consulted with numerous clients, I often recommend customization based on specific operational conditions, which significantly enhances performance.

Another aspect often overlooked is the maintenance of these gauges. Regular calibration and inspection by qualified technicians can prevent unexpected failures. During my tenure as a lead engineer, I implemented a maintenance schedule for isolation diaphragm pressure gauges, significantly reducing downtime and maintenance costs for my clients. This practice establishes trust with stakeholders when they see a reduction in operational interruptions and the longevity of equipment.
isolation diaphragm pressure gauge
Moreover,
the integration of digital technology into these gauges cannot be overstated. The shift from analog to digital has offered unparalleled accuracy, real-time monitoring, and remote data access. My collaboration with technology firms has often centered on developing user-friendly interfaces that interpret data trends, allowing engineers to make informed decisions swiftly.
In every instance where I have applied my expertise, the consistent feedback from operators and business owners has highlighted improved safety standards. Isolation diaphragm pressure gauges mitigate the risk of hazardous leaks, thus ensuring compliance with industrial safety regulations—a non-negotiable facet of modern manufacturing.
Ultimately, the key to maximizing the benefits of isolation diaphragm pressure gauges lies in a holistic approach to installation and upkeep. By leveraging expert insights, adopting best practices in calibration, and embracing cutting-edge technology, businesses not only safeguard their operations but also foster an environment of reliability and trust.
My years of working hand-in-hand with diverse industrial sectors have underscored the vital role of such instruments. As industries evolve and demands for precision escalate, those who invest in high-quality isolation diaphragm pressure gauges will undoubtedly maintain a competitive edge while minimizing risks. For organizations keen to uphold excellence in their operations, the adoption of these pressure gauges is an authoritative step towards achieving sustainable success.