Magnehelic differential pressure gauges represent a critical tool in various industries, offering precision and reliability for ensuring optimal system performance. These gauges play a pivotal role in HVAC systems, cleanrooms, and industrial operations. Their purpose is to provide clear, accurate readings of differential pressure, which can impact the functionality and safety of equipment and processes.
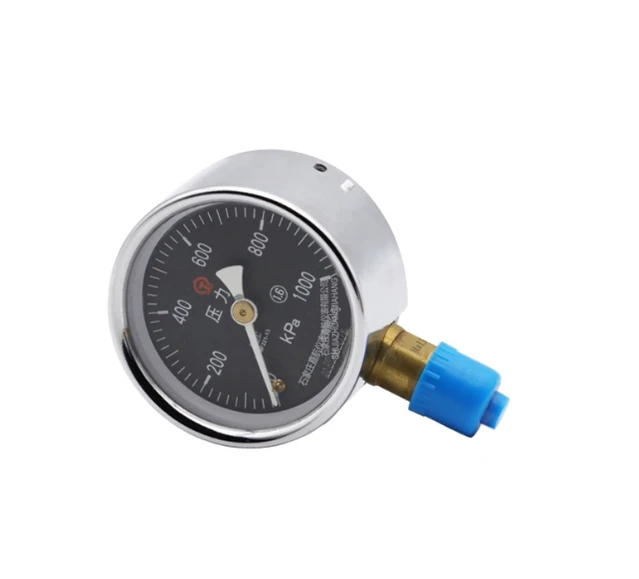
The primary value of magnehelic differential pressure gauges lies in their simplicity and accuracy. With no electronic components, these gauges rely on a magnetic helix to translate pressure differences into mechanical movement without the need for external power sources. This simplicity not only enhances their reliability but also minimizes maintenance requirements, making them a cost-effective choice for long-term use.
When selecting a magnehelic differential pressure gauge, it is crucial to consider the specific application and environment. For instance, gauges used in cleanrooms demand exceptional precision and must be resistant to contamination. In contrast, those used in industrial settings may require robust construction to withstand harsh conditions such as dust, moisture, and physical impacts. Understanding these needs ensures the right gauge is selected for the task, enhancing both safety and efficiency.
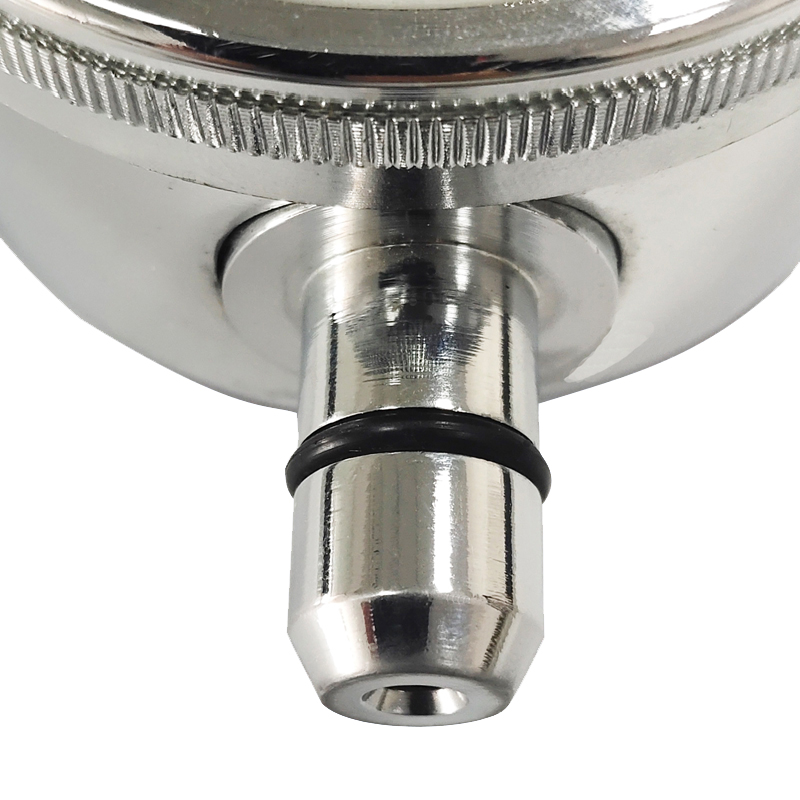
From a professional standpoint, expertise in installing and calibrating magnehelic gauges is crucial. Proper calibration ensures that readings remain accurate, which is essential for maintaining the specified conditions of a system. Technicians should be trained in understanding the implications of pressure variations and competent in adjusting gauges according to the system's specific requirements. Such expertise not only ensures operational efficiency but also prolongs the lifespan of the equipment involved.
Authoritative knowledge in the field of differential pressure measurement is vital to address potential challenges that may arise. This includes recognizing telltale signs of gauge malfunction, understanding the impact of sudden environmental changes, or knowing when to recalibrate. Being proactive in dealing with these issues maintains system integrity and prevents costly downtime or repairs.
magnehelic differential pressure gauges
Trustworthiness in dealing with magnehelic differential pressure gauges stems from using high-quality, certified products and adhering to standard industry practices. It is important to procure these instruments from reputable manufacturers known for their commitment to quality and innovation. This trust extends to the transparency in the documentation provided, detailing the specifications, compatibility, and proper handling of the gauges.
Real-world experience illustrates the tangible benefits of magnehelic differential pressure gauges. Companies have reported improved control over their systems, leading to reduced energy costs and optimized resource allocation. In cleanrooms, for example, accurate pressure control ensures that air quality remains uncontaminated, which is critical in pharmaceutical and biotechnology sectors. Similarly, in HVAC systems, maintaining correct pressure differentials can prevent malfunctions and extend the life of air filters, reducing maintenance costs and improving air quality.
Furthermore, magnehelic differential pressure gauges contribute to safety by alerting personnel to potential hazards. In ventilation systems, sudden changes in pressure can indicate blockages or leaks, allowing for timely interventions. This preemptive approach helps avoid situations that could lead to equipment damage or hazardous working conditions.
In summary, magnehelic differential pressure gauges are indispensable tools in maintaining efficiency, safety, and reliability across various industrial applications. Their non-reliance on digital technology makes them a durable and dependable choice for environments where electronic devices might fail. Implementing these gauges with a thorough understanding of their function and potential applications ensures they meet the highest standards of performance. By investing in quality gauges and fostering technical expertise, facilities can maximize their operational capacity, maintain safety, and ensure regulatory compliance.