Understanding and Utilizing Differential Pressure Gauges for Optimal Performance
A differential pressure gauge is an essential tool in various industries, from HVAC systems to oil and gas, chemical processing, and even water treatment facilities. It measures the difference between two pressure points within a system, providing critical information that ensures efficient operation and safety.
Differential pressure gauges work on a simple principle they compare the pressure at two different points in a process line, displaying the variance as a numerical value. This reading can be used to monitor flow rates, filter clogging, level measurement, and pressure drop across valves or other equipment, making them indispensable in process control.
The design of these gauges typically features a Bourdon tube, diaphragm, or capsule element that deforms according to the pressure difference, which is then translated into a readable scale. Digital versions, while more expensive, offer additional features like data logging, remote monitoring, and alarm settings, enhancing their usability and versatility.
In the field of HVAC, differential pressure gauges help maintain optimal airflow by indicating when filters need changing or ducts require cleaning. In the oil and gas sector, they monitor wellhead pressures and ensure safe extraction processes. Chemical plants rely on them to monitor pressure drops across reactors or pipelines, preventing potential leaks or failures.
Choosing the right differential pressure gauge depends on factors such as pressure range, accuracy requirements, and environmental conditions
Choosing the right differential pressure gauge depends on factors such as pressure range, accuracy requirements, and environmental conditions
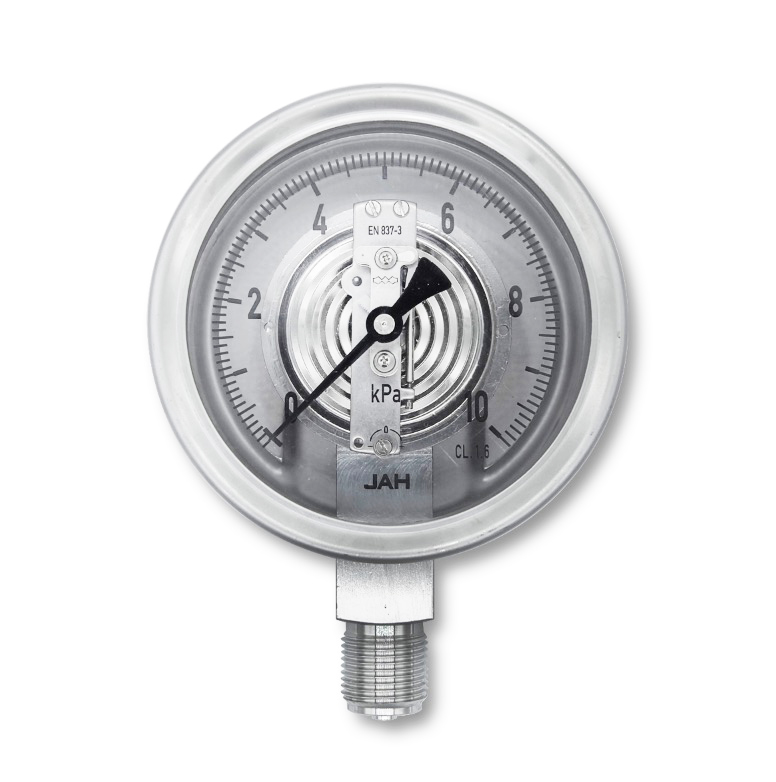
Choosing the right differential pressure gauge depends on factors such as pressure range, accuracy requirements, and environmental conditions
Choosing the right differential pressure gauge depends on factors such as pressure range, accuracy requirements, and environmental conditions
differential presure gauge product. Low-pressure gauges are suitable for applications like air conditioning systems, while high-pressure models are needed for more intense processes like hydraulic systems.
Maintenance of differential pressure gauges is equally important. Regular calibration ensures accurate readings, while proper installation and protection from harsh environments prolong their lifespan. It's also crucial to choose gauges with appropriate materials to withstand corrosive fluids or extreme temperatures.
In conclusion, differential pressure gauges are more than just measuring instruments; they are vital components in maintaining operational efficiency and safety in numerous industries. By understanding their function, selecting the correct type, and implementing regular maintenance, users can harness their full potential and ensure reliable performance. Whether it's monitoring a complex industrial process or a simple household appliance, the humble differential pressure gauge remains an unsung hero in the world of pressure measurement.