Cryogenic differential pressure gauges are specialized instruments designed to measure pressure differences in extremely low-temperature environments. These environments are crucial in industries such as liquefied natural gas (LNG) processing, aerospace, and scientific research. Based on extensive experience with OEM cryogenic differential pressure gauges, their design must prioritize both precision and durability to ensure accurate readings and longevity in challenging settings.
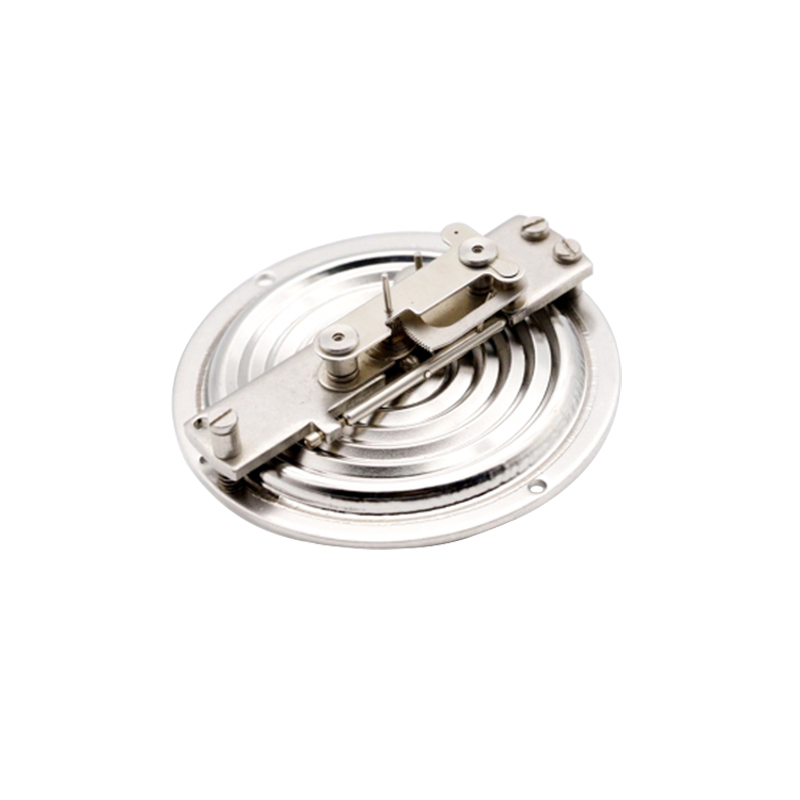
In the cryogenic sphere, precision is paramount. Accurate readings can mean the difference between safe operation and catastrophic failure in systems relying on LNG or other cryogenic substances. OEM manufacturers bring a level of expertise in developing these gauges by incorporating materials that withstand the extreme contraction caused by sub-zero temperatures. Stainless steel and specialized alloys are often used for their resilience and minimal reaction to temperature variations, ensuring that the differential pressure gauges maintain their integrity and performance.
Authoritativeness in this niche market is grounded in rigorous testing and industry credentials. Leading OEMs invest heavily in research and development, often collaborating with academic institutions and industry leaders to push the boundaries of what cryogenic pressure measurement can achieve. Their commitment to innovation is evident in the continuous evolution of their products which offer enhanced features such as digital readouts, remote monitoring capabilities, and improved response times.
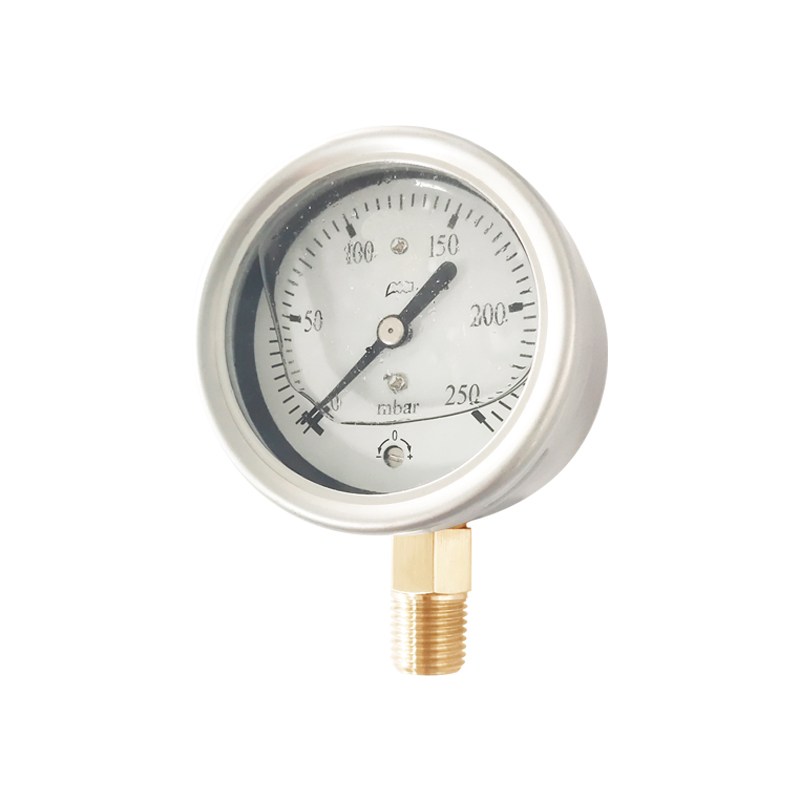
Trustworthiness in OEM cryogenic differential pressure gauges cannot be understated. In industries where these gauges are utilized, the stakes are high, and there is little room for error. Established OEMs provide comprehensive certification and compliance with international standards such as ISO 9001 and ASME, as well as specific industry regulations, to ensure users can rely on their gauges for critical applications. Furthermore, their dedication to post-sales support, including training, field services, and technical support, reinforces trust, offering peace of mind to operators and managers alike.
oem cryogenic differential pressure gauges
In practice, the application of a high-quality OEM cryogenic differential pressure gauge can transform operational efficiency and safety standards. For instance, in LNG plants, these gauges enable the precise control of pressure levels in storage tanks and pipelines, ensuring that the contained gases remain in their liquid state without risk of evaporation or containment failure. Such precision not only maximizes safety but also optimizes energy efficiency and cost-effectiveness.
Additionally, the aerospace industry benefits significantly from these gauges in propulsion and spacecraft systems. The ability to accurately measure differential pressure at cryogenic levels is crucial for liquid oxygen and hydrogen storage, which are used as rocket fuel. OEMs with expertise in this sector understand the critical nature of reliability and precision, and therefore they design their gauges to perform under the unique conditions present in high-altitude and space environments.
In summary, OEM cryogenic differential pressure gauges stand at the intersection of cutting-edge technology and essential industrial application. Their role in maintaining safety and efficiency in cryogenic processes cannot be overstated. Companies dedicated to producing these gauges provide indispensable expertise and authoritative solutions that bolster trust across industries fundamentally reliant on cryogenic measurements. With continuous innovation and unwavering commitment to quality and compliance, these OEMs lead the way in offering tools that are not only necessary but transformative in how we understand and harness cryogenic environments.