Selecting a reliable pressure gauge for industrial applications is crucial to maintaining efficiency and safety. Among the myriad of options available, the OEM Rueger diaphragm pressure gauge stands out as a hallmark of precision and durability. This article will delve into the intricacies of this pressure measurement device, highlighting its unique features, the technology that underpins its functionality, and why it is a preferred choice for professionals worldwide.

The OEM Rueger diaphragm pressure gauge is not just another instrument in the pressure measurement arena; it embodies a commitment to engineering excellence. Its design is tailored to handle strenuous environments, making it ideal for sectors like chemical processing, pharmaceuticals, and food manufacturing. These industries demand equipment that can withstand harsh conditions while delivering accurate readings, and the Rueger gauge excels in this regard.
One of the defining characteristics of this diaphragm pressure gauge is its ability to isolate the sensing mechanism from the process fluid. This is achieved through its advanced diaphragm seal system, which serves as a protective barrier preventing corrosive or viscous media from coming into contact with the sensitive internal components. The diaphragm is crafted from materials like stainless steel, Hastelloy, or Tantalum, offering versatility to suit different media conditions. This smart design not only extends the lifespan of the gauge but also enhances its reliability for critical applications, thereby embodying expertise and authority in its design.
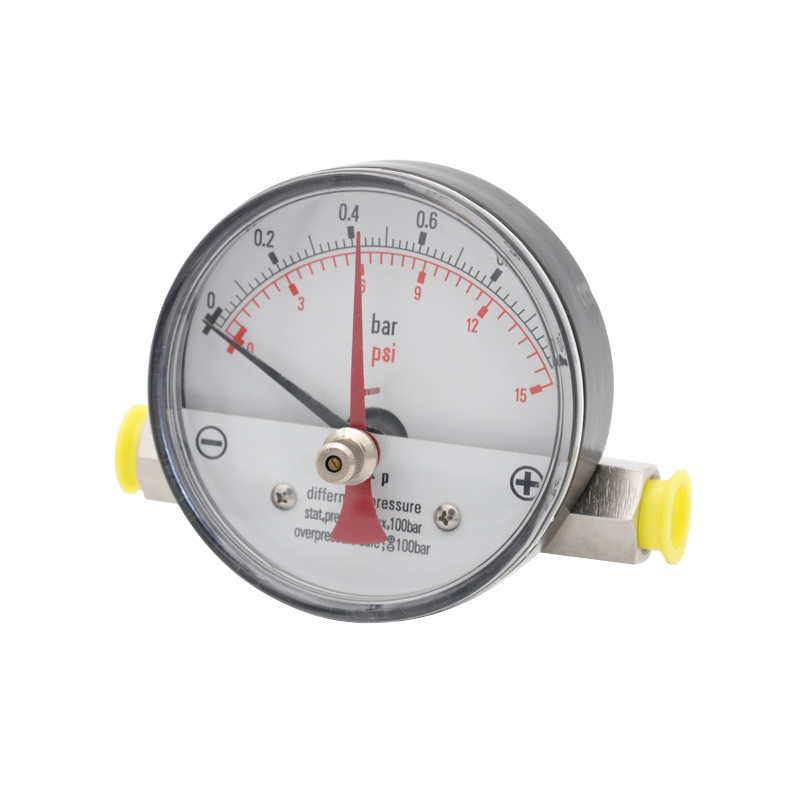
In the realm of accuracy, the OEM Rueger gauge stands unchallenged. The device utilizes micro-electromechanical systems (MEMS) technology, known for its high precision and stability. This innovation allows users to achieve readings with minimal deviation, which is paramount in processes where even the slightest variance can lead to significant complications. Furthermore, the gauge is engineered to offer a zero-leakage advantage, a vital feature for environmentally sensitive operations.
Adopting a diaphragm pressure gauge requires understanding its trustworthiness. The OEM Rueger gauge undergoes rigorous testing and calibration procedures to ensure it meets international standards. It operates efficiently within a broad range of temperatures and pressures, exemplifying its robustness and capacity to deliver trustworthy measurements consistently. Such stringent quality controls and certifications, including ISO and CE, establish its credibility and foster user confidence.
oem rueger diaphragm pressure gauge
Professional users appreciate the gauge's ergonomic design, which facilitates straightforward installation and minimal maintenance. The user-centric focus extends to its readability, with a clear dial and marked scale, ensuring that operators can quickly and accurately interpret readings. This practicality is essential in high-paced environments where time is of the essence.
From an experience standpoint, those who have integrated the OEM Rueger diaphragm pressure gauge into their systems report higher operational efficiency and reduced downtime. By ensuring accurate pressure monitoring, these gauges help prevent equipment damage and optimize process control, thus reducing maintenance costs and enhancing overall productivity.
In essence, the OEM Rueger diaphragm pressure gauge exemplifies a harmonious blend of innovation, quality, and reliability, making it a staple for industries that cannot compromise on precision. Its engineered designs align perfectly with the demanding nature of modern-day applications, affirming its place as an indispensable tool for engineers and technicians alike.
Choosing an OEM Rueger diaphragm pressure gauge equates to investing in a product backed by scientific rigor and trusted by industry experts. Its unmatched precision, durable construction, and user-friendly attributes make it a superior choice for those seeking a dependable solution in pressure measurement. As technology continues to advance, the OEM Rueger pressure gauge remains at the forefront, consistently adapting to meet the evolving needs of industrial applications.