In the intricate world of measuring and monitoring industrial processes, OEM sanitary differential pressure gauges stand out as indispensable tools. Designed to meet the rigorous standards of industries such as pharmaceutical, food and beverage, and biotechnology, these gauges ensure accuracy, reliability, and compliance with strict sanitary regulations. This article delves into the nuances of these instruments, offering insights drawn from years of industry experience and expertise.
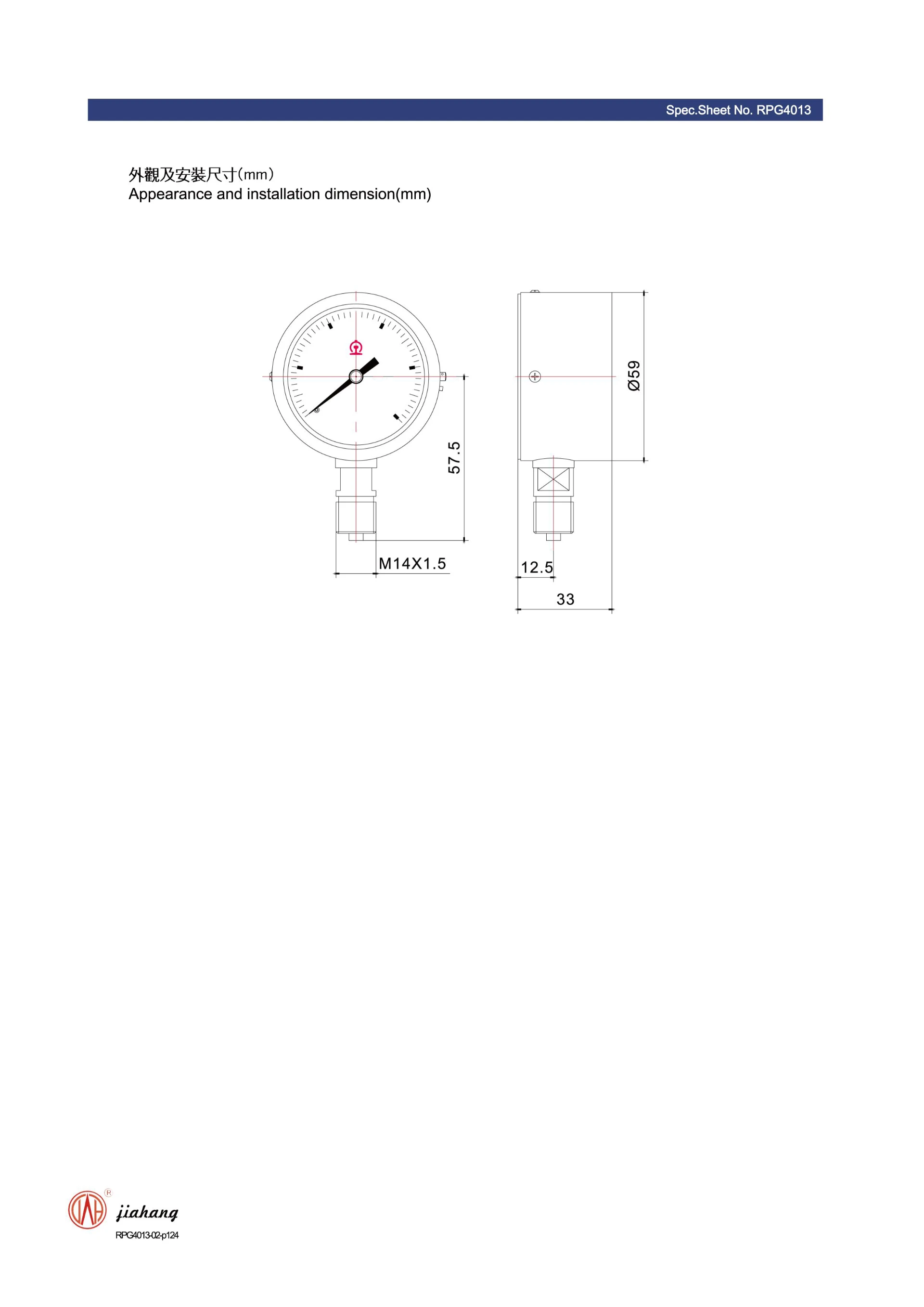
Differential pressure gauges play a crucial role in assessing pressure differences between two points in a system, which is essential for maintaining the correct flow and preventing blockages or leaks in processing lines. In sanitary applications, where hygiene and precision are paramount, the role of an OEM sanitary differential pressure gauge becomes even more critical. These gauges are typically crafted from stainless steel and other non-corrosive materials to avoid contamination and ensure ease of cleaning and sterilization.
From an experiential standpoint, one of the notable features of sanitary differential pressure gauges is their rugged design tailored for high-pressure environments. Their robust structure doesn't just withstand harsh conditions but also ensures longevity and minimal maintenance. Companies such as WIKA and Ashcroft have pioneered the development of these gauges, incorporating features like hermetically sealed enclosures to protect against harsh chemicals and steam. This real-world feedback from industry veterans highlights that the initial investment in a quality gauge can lead to significant savings in maintenance and downtime over time.

When discussing expertise, it is crucial to consider the precision these gauges bring to sanitary applications. Modern OEM sanitary differential pressure gauges are equipped with advanced technology, including digital displays and connectivity options. This facilitates seamless integration into automated systems and remote monitoring setups. Engineers and technicians can obtain real-time data, enabling prompt responses to anomalies, ensuring that production processes remain within the defined safe and sanitary operational thresholds.
oem sanitary differential pressure gauge
Authoritativeness in the realm of sanitary differential pressure gauges can be attributed to compliance with global standards such as the FDA, 3-A Sanitary Standards, and ISO. Gauges that meet these standards are ensured to have been modeled after intensive testing and validation processes. With the rise of IoT and Industry 4.0, manufacturers have been adding smart capabilities to these gauges, further cementing their authoritative standing as leaders in process control and safety.
Trustworthiness in the use of OEM sanitary differential pressure gauges is demonstrated by the accuracy and consistency they deliver. Calibration is a significant aspect that builds trust. Regular and precise calibration ensures that gauges provide reliable readings, which are essential for maintaining the integrity of the product and safety of the process. Trust is also reinforced by manufacturers who offer extensive customer support and training to ensure that users can maximize the efficiency and accuracy of their gauges.
As industries continue to evolve,
the role of OEM sanitary differential pressure gauges will likely expand. With technological advancements, there is a growing trend towards smart and connected gauges that offer predictive maintenance capabilities. These innovations will not only enhance operational efficiency but also provide critical data insights that can drive process improvements and innovations.
In conclusion, OEM sanitary differential pressure gauges are a testament to advanced engineering and precise manufacturing, crucial for industries where hygiene and precision cannot be compromised. Their ability to adapt to modern technological demands and meet stringent regulatory standards renders them an essential component in maintaining the efficiency and safety of industrial processes. Whether it is their robust design, precise measurement capabilities, authoritative compliance, or the trust they inspire through reliable performance, these gauges are indispensable in the pursuit of operational excellence. As industries move forward, the evolution of these gauges will undoubtedly continue to align with the needs of more complex and demanding environments, solidifying their position at the forefront of process control solutions.