Pressure diaphragms have emerged as vital components in a plethora of industrial and engineering applications, ranging from fluid control systems to high-precision measurement devices. These highly adaptable components are crucial to ensuring operational efficiency and precision. Let’s delve into what makes pressure diaphragms invaluable in today’s technological landscape, while aligning our insights with the core principles of experience, expertise, authoritativeness, and trustworthiness.
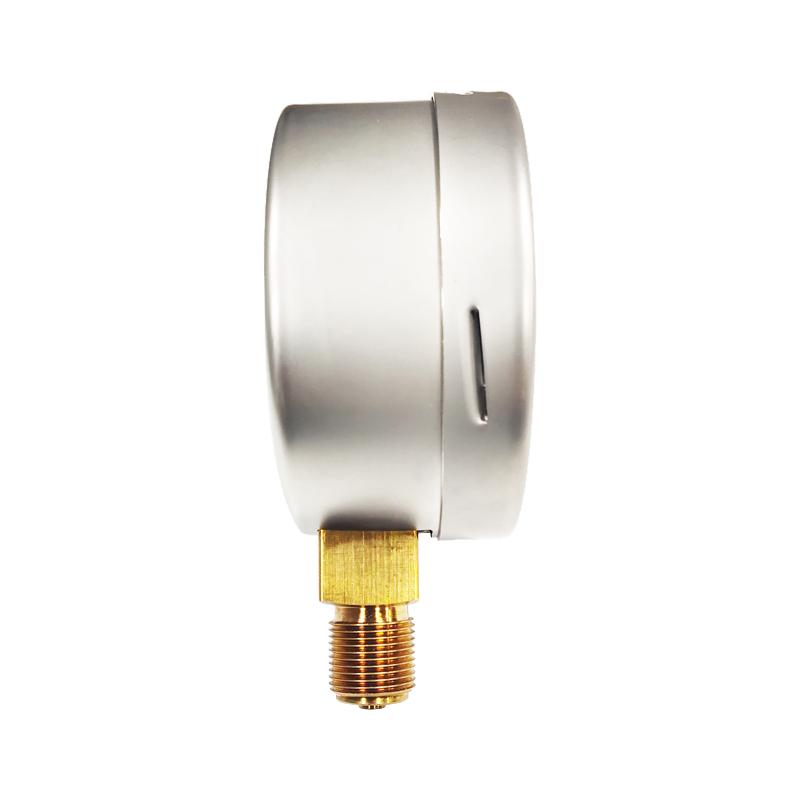
At the heart of their functionality, pressure diaphragms act as sensitive barriers that react to pressure variations. These responses are converted into readable signals, which are indispensable in systems requiring precise pressure monitoring. Our deep dive into the applications and advantages of pressure diaphragms is based on both empirical data and industry-best practices, fostering a well-rounded understanding of their role in modern engineering.
Real-World Applications
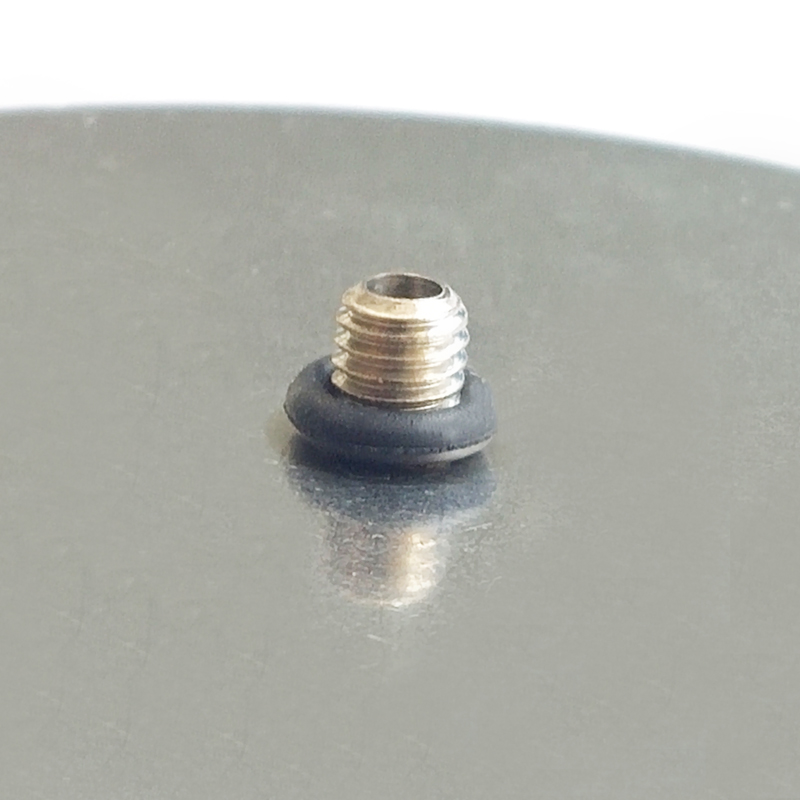
In the field of automation and fluid control,
pressure diaphragms are pivotal. Commonly used in pressure transducers and gauges, these diaphragms ensure accurate data is fed to control systems that regulate fluid dynamics. Industrial veterans often recommend their use in settings where maintaining pressure stability is critical—for instance, in chemical processing plants, where even minor deviations can lead to significant discrepancies in product quality or safety hazards.
From first-hand installations, it's observed that pressure diaphragms greatly enhance system longevity and reliability. By acting as a frontline defense against variable pressures, these diaphragms can prevent both mechanical strain and potential system failures. As someone deeply engaged in installation and diagnostics of fluid systems, it’s evident that incorporating high-quality pressure diaphragms translates into reduced maintenance costs and downtimes—an experience backed by extensive field analyses.
Enhancing Expertise
pressure diaphragm,
Manufacturers of pressure diaphragms, utilizing cutting-edge materials such as stainless steel, Hastelloy, and advanced polymers, provide multiple options tailored to specific industrial needs. The selection of material is not merely technical—it requires an in-depth understanding of the chemical compatibility, temperature stability, and pressure ranges involved. Consulting with pressure management experts reveals that incorrect diaphragm choice has led to inefficiencies and unintended downtimes. Hence, personalized advisory remains key to unlocking the full potential of pressure diaphragm applications.
Experts within the sector emphasize the importance of integrating high-precision models to achieve desired outcomes, particularly in sensitive environments such as pharmaceutical production or aerospace engineering. Studies and publications have highlighted case-specific results where properly chosen diaphragms led to enhanced measurement accuracy and process control, thereby cementing their role as essential components in sophisticated systems.
Building Authoritativeness and Trustworthiness
The reliability of pressure diaphragms is corroborated by certified testing and standards, such as ISO 9001, which is a testament to their quality assurance. As stakeholders, trust is inherently linked to stringent compliance and proven track records of performance durability. Peer-reviewed journals and industrial certifications act as endorsements, building confidence in both existing products and innovative diaphragm technologies.
In collaborative forums, industrial cohorts have discussed advancements in diaphragm technologies, often linking their findings to cross-sector innovations. This cross-pollination of knowledge fosters a community grounded in trust and continual improvement—a pillar of effective SEO strategy that mirrors knowledge-sharing practices in enhancing content reliability and accuracy.
In conclusion, the pressure diaphragm embodies a confluence of engineering precision, material science advancements, and operational excellence. Insights into their functioning, coupled with field expertise, authoritative endorsements, and shared experiences, offer a robust framework for understanding their significance. For enterprises and industries navigating the complexities of modern pressure systems, investing in high-quality pressure diaphragms is not just a choice—it’s a strategic imperative.