Pressure diaphragms have emerged as integral components in various industries, providing not only precision but also reliability in pressure measurement and control. Their nuanced application spans from industrial machinery to sophisticated medical equipment, allowing for accurate pressure, flow, and level monitoring. Understanding the intricacies of pressure diaphragms reveals a rich tapestry of engineering excellence, fostering trust and reliability in these devices.
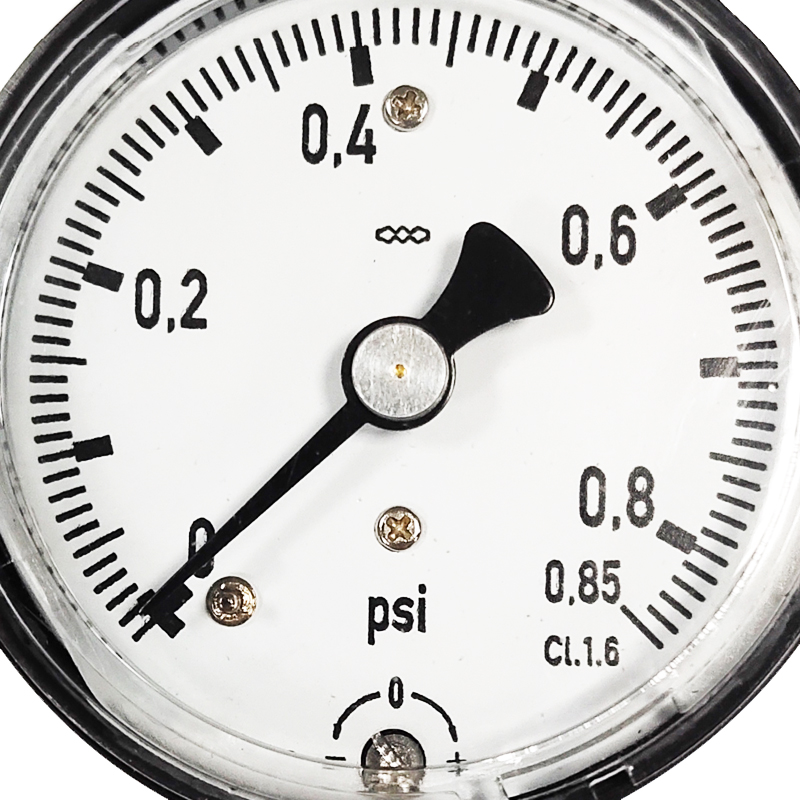
A pressure diaphragm, at its core, is a flexible membrane that responds to the pressure of gases or liquids. It acts as a superior barrier, isolating the pressure sensor from the process fluid. This isolation is crucial in corrosive, high-temperature, or hazardous environments, as the diaphragm ensures both safety and longevity of the pressure sensing elements. Such protection is vital, especially in chemical processing or pharmaceutical industries, where even minor exposure could lead to significant contamination or equipment failure.
The real-world experiences of industries utilizing pressure diaphragms highlight their indispensability. In the oil and gas sector, these diaphragms are fundamental for maintaining operational integrity in extreme conditions. Operators report that pressure diaphragms enable them to monitor pressure fluctuations with unparalleled accuracy, preventing leaks or bursts that could lead to catastrophic failures or environmental disasters.
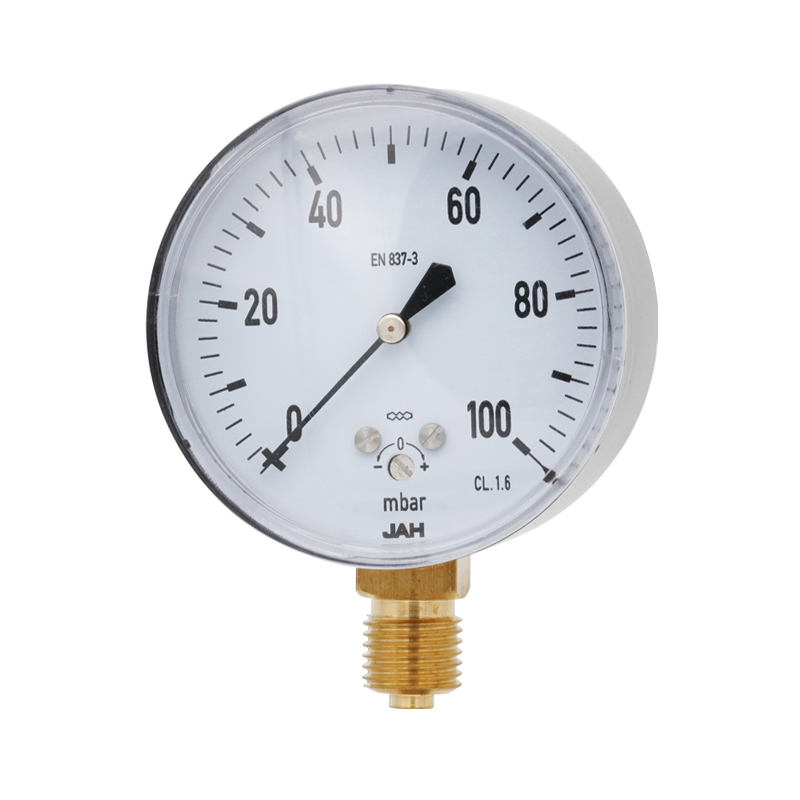
From an expertise standpoint, the development of pressure diaphragms involves cutting-edge materials and manufacturing processes. Polytetrafluoroethylene (PTFE), stainless steel, and even exotic alloys such as Inconel are often employed, chosen for their resilience against harsh chemicals and high pressures. Engineers and scientists collaborate to refine the diaphragm’s design, ensuring it meets specific industrial standards and performance requirements. This synergy between design and material science underscores the diaphragm's precision and reliability, inspiring confidence among users.
pressure diaphragm,
Authoritativeness in this field is bolstered by rigorous testing and certifications. Leading manufacturers subject pressure diaphragms to extensive fatigue testing, burst testing, and temperature cycling. Such testing is crucial for certifications from bodies like the American Society of Mechanical Engineers (ASME) and the International Organization for Standardization (ISO), which validate the diaphragm's performance under prescribed conditions. These certifications serve as a testament to the diaphragm’s reliability, influencing procurement decisions in sectors where safety and accuracy are paramount.
Trustworthiness of pressure diaphragms comes not only from their structural integrity but also from their ability to adapt to evolving technological needs. In the age of the Internet of Things (IoT), pressure diaphragms are integrated into smart systems, offering real-time data and analytics. Operators in industries such as water treatment and food processing benefit from this integration, as it allows for seamless monitoring and prompt response to pressure changes. This real-time capability minimizes downtime, enhances operational efficiency, and ensures product quality, aligning with industry standards and regulatory requirements.
In conclusion, the pressure diaphragm represents a fusion of engineering prowess, material science, and industry insight. Its application across diverse sectors testifies to its utility and reliability. By ensuring safety, precision, and adaptability, pressure diaphragms not only meet current industry demands but also pave the way for future innovations in pressure measurement and control systems.