In the realm of precision measurement and control systems, the pressure diaphragm capsule element stands out as a critical component. Its application spans various industries, including aerospace, automotive, medical, and industrial automation. Offering unparalleled sensitivity and accuracy, these elements are crucial in ensuring systems operate within designated parameters.
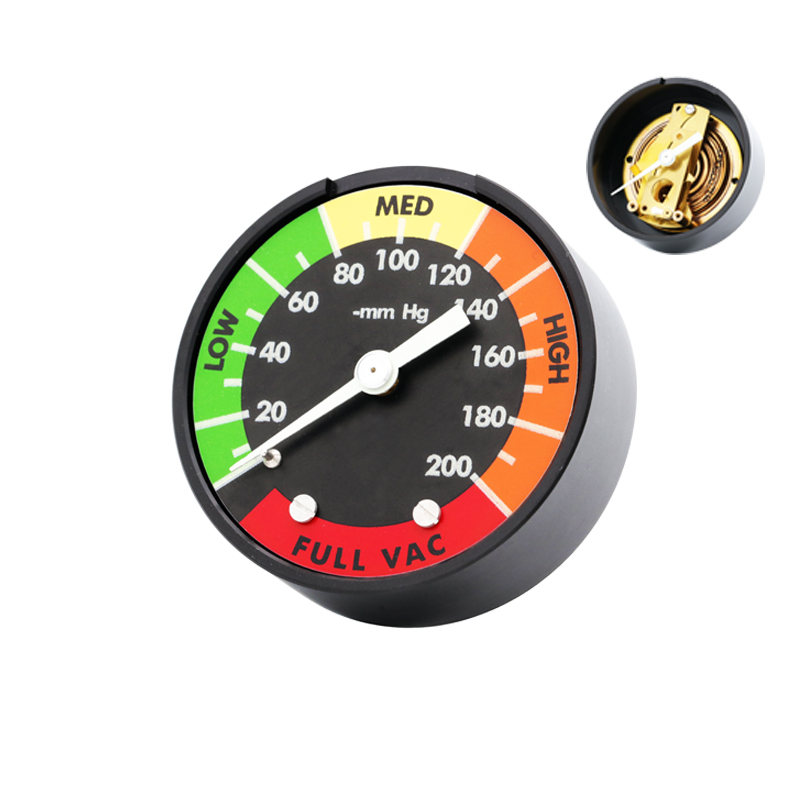
A pressure diaphragm capsule element operates on a simple yet effective principle. It consists of a diaphragm, often made of stainless steel or other robust materials, that deflects under pressure. This deflection is converted into an electrical signal that is then processed and interpreted. Its ability to measure minute pressure variations makes it indispensable for applications where even marginal changes could have significant implications.
In industries such as aerospace, precision is paramount. The pressure diaphragm capsule element assists in maintaining the balance and control of aircraft systems. By providing accurate pressure readings, it ensures that any deviation is quickly corrected, enhancing safety and performance. Moreover, its robustness under high-pressure conditions makes it ideal for such high-stakes environments.
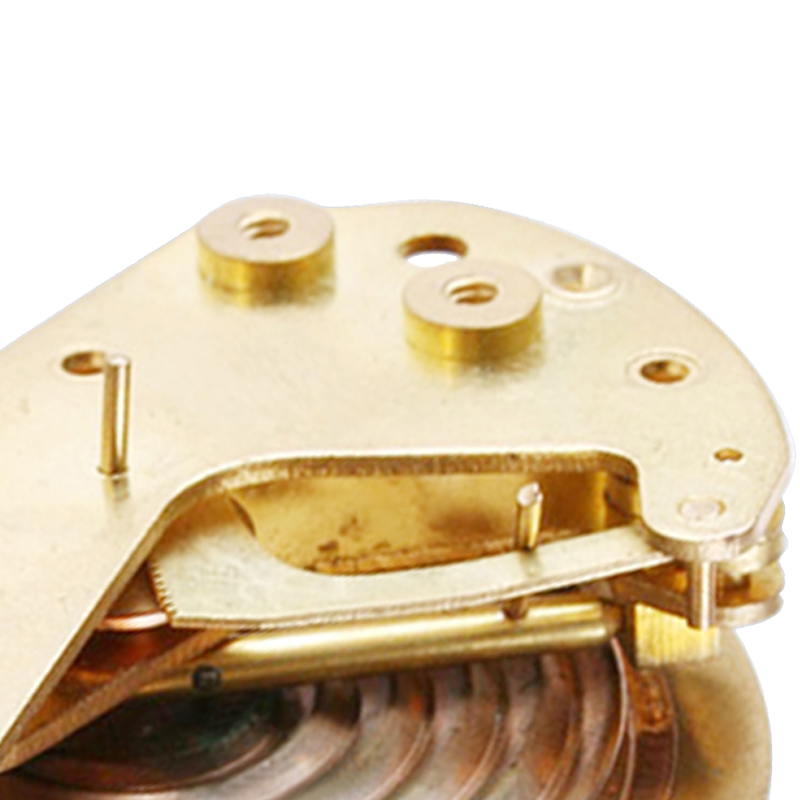
The automotive industry benefits significantly from this technology, particularly in emission control systems and engine management. Modern vehicles rely on an array of sensors to optimize performance and reduce emissions. Pressure diaphragm capsule elements play a vital role by delivering precise pressure data that guides these systems in making real-time adjustments, thus achieving higher fuel efficiency and lower emissions.
In the medical field, the need for accurate, reliable pressure measurement cannot be overstated. Devices such as blood pressure monitors and ventilators depend on pressure diaphragm capsule elements for their functionality. These elements ensure that the devices deliver accurate readings and perform correctly under various conditions, which is crucial for patient care and safety.
pressure diaphragm capsule element,
When it comes to industrial automation, the pressure diaphragm capsule element is a cornerstone component. Process industries, such as oil and gas, chemical, and food processing, utilize these elements to monitor and control processes. This ensures that operations remain efficient, safe, and in compliance with regulatory standards. The sensors provide real-time data, allowing for immediate adjustments and optimizations, reducing wastage and enhancing productivity.
The expertise required in manufacturing pressure diaphragm capsule elements underscores their complexity and importance. Precision engineering and advanced materials science are integral to their development, ensuring that the products not only meet but exceed industry standards. Manufacturers must exhibit superior craftsmanship and technological prowess, ensuring the elements can withstand diverse operating conditions while maintaining their accuracy and reliability.
Trustworthiness and authoritativeness in this domain stem from years of rigorous testing and validation. Reputable manufacturers subject their products to extensive testing protocols to ensure their reliability and durability. Such rigorous processes ensure that these elements can be trusted to perform under the most challenging scenarios, reinforcing their role as an authoritative solution in pressure measurement technology.
Innovations continue to emerge, enhancing the capabilities and applications of pressure diaphragm capsule elements. Research into new materials and sensing technologies promises to expand their application range further and enhance performance metrics. As the demand for more accurate and efficient systems grows, these elements will undoubtedly remain at the forefront, driving advancements across multiple sectors.
To summarize, the pressure diaphragm capsule element is crucial for various critical applications across several industries. Its proven performance, built on a foundation of expertise, trustworthiness, and technological authority, ensures its place as an indispensable component in modern measurement and control systems. As technology progresses, these elements will continue to evolve, meeting the challenges and opportunities that lie ahead.