The transformative impact of the pressure diaphragm capsule element on industrial applications cannot be overstated. This small yet pivotal component serves as the backbone for a myriad of pressure measuring devices across various sectors. Understanding its functions and advantages not only underlines its necessity but also underscores its dominance in creating accurate measurements pivotal for operational success.
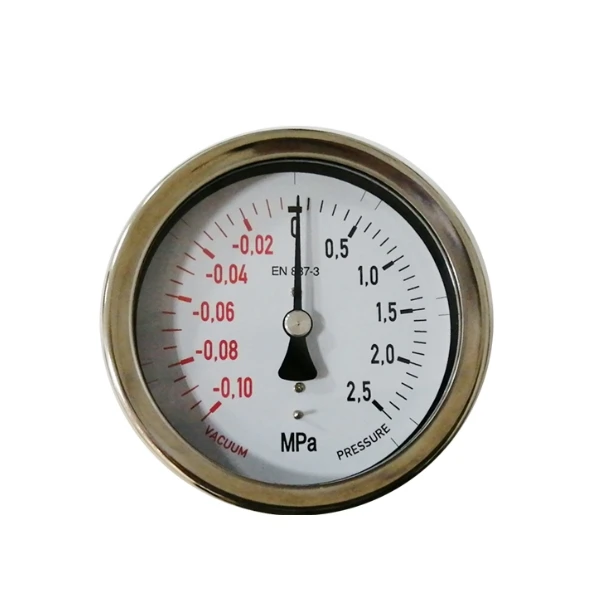
Pressure diaphragm capsule elements play a crucial role in the precision measurement of pressure changes in industrial settings. Their fundamental design is both simple and highly effective a thin membrane, often constructing from materials like elastomers, metals, or ceramics, undergoes displacement when exposed to pressure differences. This displacement transmits pressure variations to a sensing device—transforming mechanical deformation into an electrical signal—which can then be calibrated for precise readings.
The choice of materials used in manufacturing these pressure diaphragm capsule elements effects durability and performance. Metal diaphragms, such as those made of stainless steel, offer resistance to high-pressure environments and corrosive substances, making them ideal for use in harsh industrial conditions. Elastomer diaphragms, on the other hand, are prized for their flexibility and ability to maintain function under lower pressure ranges.
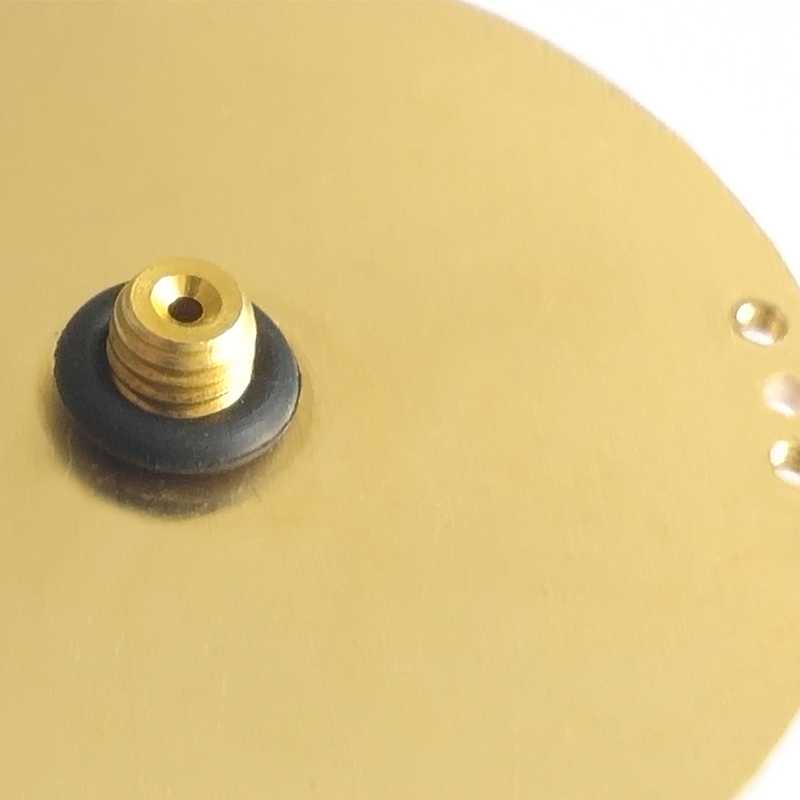
Industries such as oil and gas, chemical manufacturing, and aerospace heavily rely on the accuracy and reliability provided by these elements. For instance, in the oil and gas sector, where maintaining precise pressure levels is crucial for the safety and efficiency of drilling operations, the diaphragm capsule element is indispensable. It ensures that pressure levels within compressors or reservoirs do not exceed safety limits, preventing potential hazards.
pressure diaphragm capsule element,
Furthermore, the expertise involved in the production of pressure diaphragm capsule elements is evident in the continual advancements of their design. Developers now incorporate digital technologies for real-time data monitoring and analysis. Enhanced sensing capabilities, driven by micro-electromechanical systems (MEMS), offer significant improvements in sensitivity and resolution that were previously unattainable. This evolution highlights the industry's commitment to innovation and excellence.
Trust in pressure diaphragm capsule elements is further established through rigorous testing and compliance with industry standards. Certification from recognized authorities and adherence to international standards, such as those from the International Organization for Standardization (ISO), affirm their reliability and quality. Manufacturers consistently prioritize customer trust by ensuring all products meet stringent safety and operational standards.
To maximize the element's operational longevity and maintain accuracy, regular maintenance is crucial. Experts in field applications recommend periodic inspections and calibrations. These practices not only ensure consistent performance but also help identify potential wear and tear before they lead to device failure. Training personnel in the correct handling and maintenance procedures is also vital, assuring extended usage and reliability.
In conclusion, the pressure diaphragm capsule element is a cornerstone of modern industrial measurement technology. Its application spans countless fields where precision is the hallmark of operational success. By investing in quality materials, adhering to stringent standards, and embracing technological advancements, industries reinforce their commitment to safety and efficacy. With proper care and expertise, the utility of these elements continues to propel industrial capabilities forward, safeguarding their place as indispensable tools in the world of pressure measurement.