Understanding the Best Differential Pressure Gauge for Optimal Performance
In the world of industrial instrumentation, a differential pressure gauge plays a pivotal role in measuring the difference in pressure between two points within a system. It's a critical tool for various applications, including fluid dynamics, HVAC systems, and process control. When it comes to selecting the 'best' differential pressure gauge, the focus should be on precision, reliability, and durability.
A differential pressure gauge essentially works by comparing the pressure on one side of its diaphragm or Bourdon tube to the pressure on the other side. This comparison provides valuable information about flow rates, filter clogging, level measurement, and more. The best differential pressure gauge, therefore, is one that can accurately and consistently provide this data under varying conditions.
One key factor to consider when choosing the best gauge is accuracy. Look for gauges with high precision, often indicated by an American National Standards Institute (ANSI) or International Organization for Standardization (ISO) certification. These certifications ensure that the gauge meets stringent standards for accuracy and reliability.
Durability is another crucial aspect. The gauge should be able to withstand harsh environments, extreme temperatures, and potential mechanical shocks. Stainless steel construction, for instance, offers excellent resistance to corrosion and physical damage, making it a popular choice for industrial-grade differential pressure gauges.
The gauge's range and sensitivity are also essential
The gauge's range and sensitivity are also essential
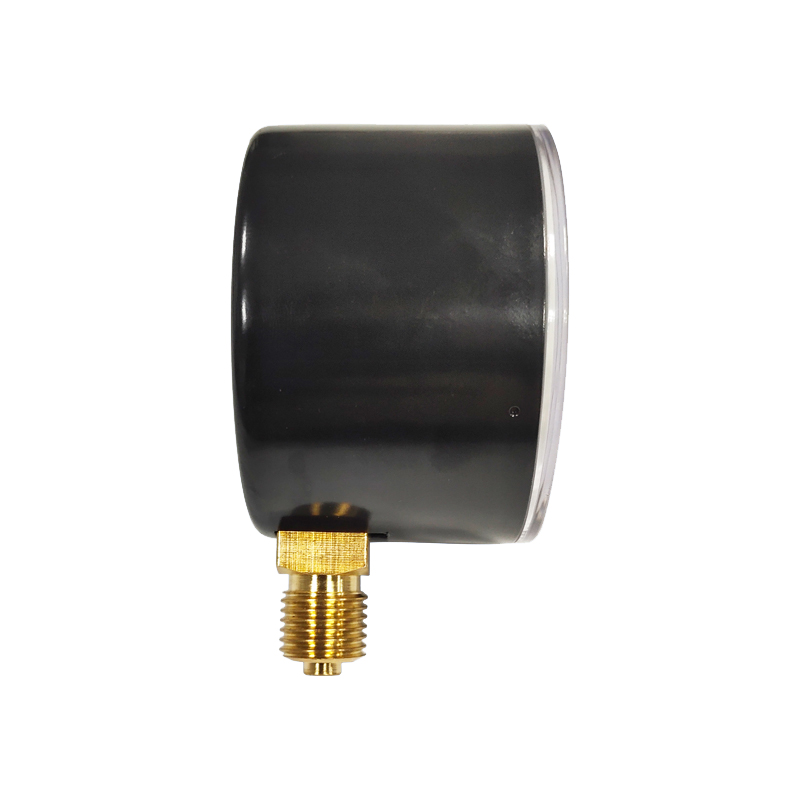
The gauge's range and sensitivity are also essential
The gauge's range and sensitivity are also essential
best wise differential pressure gauge. The range should be appropriate for the expected pressure differences in the application, while the sensitivity should allow for fine-tuned readings. Digital differential pressure gauges, with their advanced display features and ability to record and analyze data, can offer exceptional sensitivity and versatility.
Ease of use and maintenance are equally important. A user-friendly interface, clear visibility, and quick calibration procedures contribute to the usability of the gauge. Additionally, gauges with long service intervals and easily replaceable parts can minimize downtime and maintenance costs.
Furthermore, compatibility with different systems and integration with automation technologies can enhance the overall efficiency of the process. Modern differential pressure gauges often come with digital outputs, such as 4-20mA signals or wireless connectivity, allowing seamless integration into existing control systems.
In conclusion, the 'best' differential pressure gauge is not just about the highest price tag or most advanced technology. It's about finding the right balance between precision, durability, usability, and adaptability to meet specific application requirements. Always consider the operating conditions, required accuracy, and potential integration needs when making your selection. Remember, the right differential pressure gauge can make all the difference in ensuring optimal performance and efficiency in any industrial process.