Differential pressure gauges are vital instruments in a multitude of industrial applications, providing critical data that ensure both operational effectiveness and safety. These gauges measure the difference in pressure between two points, allowing technicians to monitor systems such as ventilation, fluid flow, and filtration processes.
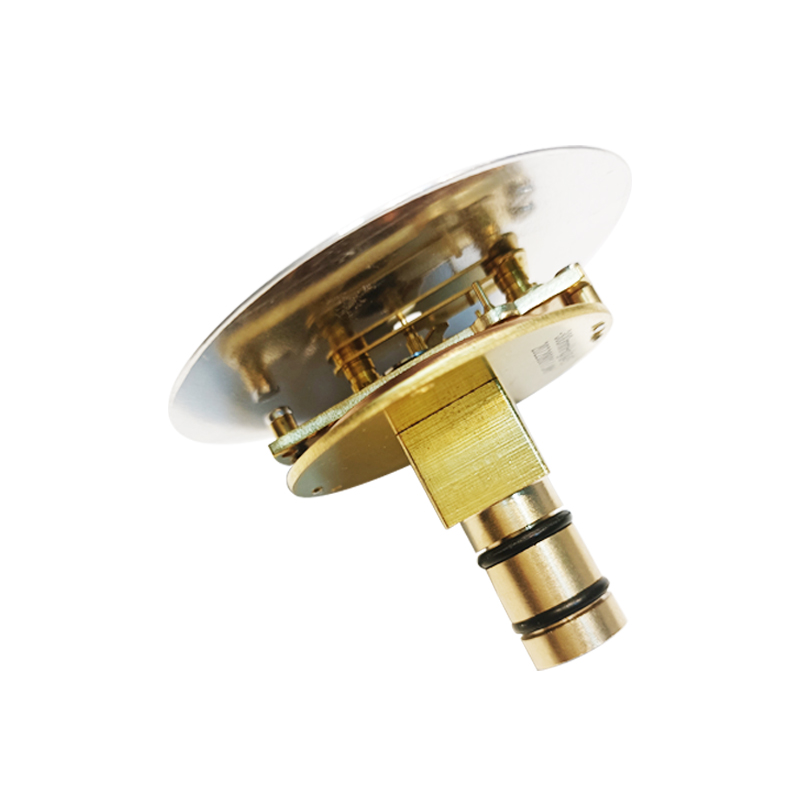
In the realm of differential pressure gauges, several types stand out due to their distinct features and suitability for different environments. Understanding the nuances of each type can greatly enhance decision-making processes when it comes to selecting the most appropriate tool for a specific application.
1.
Diaphragm Differential Pressure Gauges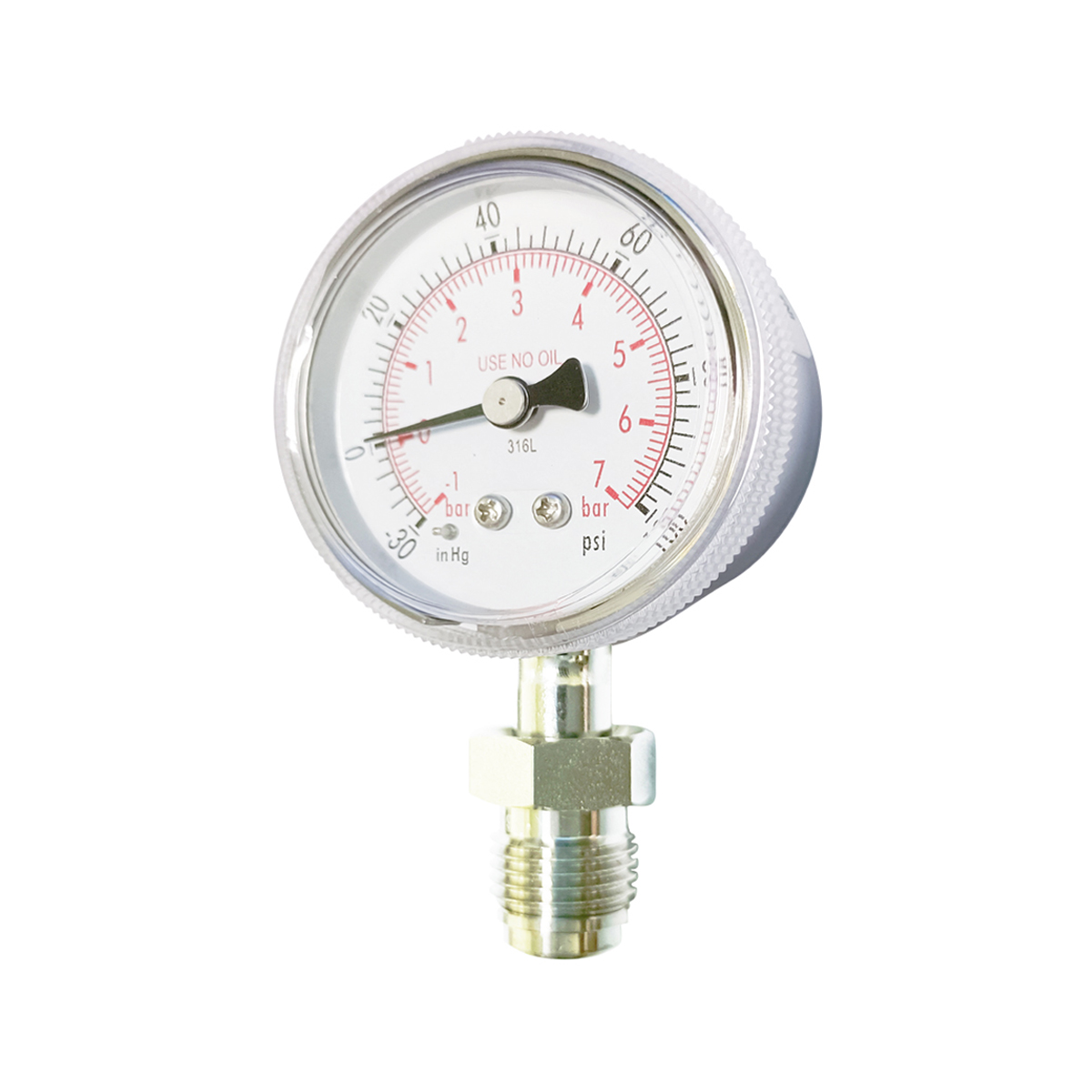
The diaphragm differential pressure gauge is celebrated for its simplicity and reliability. Typically, these gauges utilize a diaphragm that flexes in response to pressure differences, moving a dial that correlates to the pressure measurement. They are ideal for applications requiring minimal maintenance or where the media is too viscous or may crystallize. The diaphragm design is often resistant to wear and tear, providing superior durability in harsh environments such as those found in chemical processing plants.
2. Capsule Differential Pressure Gauges
Capsule differential gauges feature two chambers separated by a flexible diaphragm, making them well-suited for measuring low differential pressures with high precision. The sensitivity of capsule gauges allows them to detect even minute pressure changes, which is beneficial in applications like filter monitoring and HVAC systems. The double-capsule construction is particularly effective in maintaining accuracy over a wide range of pressures, providing unerring readings even in dynamic settings. The expert craftsmanship that goes into their manufacturing ensures consistent performance and longevity.
3. Piston Differential Pressure Gauges
Designed to withstand high pressure and harsh conditions, piston differential pressure gauges employ a piston mechanism, which ensures a robust performance. These gauges are capable of measuring higher differential pressures compared to diaphragm and capsule types, often found in hydraulic systems and applications where robust construction is paramount. They're highly valued for their resistance to shock and vibration, qualities that are enhanced by the precision engineering techniques used in their development. System reliability is substantially improved when accurate pressure calculations are consistently necessary.
types of differential pressure gauges
4. Bellows Differential Pressure Gauges
Bellows differential gauges are distinguished by their extensive range of motion, which allows for precise and accurate measurements over a broad spectrum. The bellows, often crafted from metallic materials, expand and contract in response to pressure changes. This type of gauge is particularly useful in environments where high or fluctuating pressures are a concern. The high-quality construction and materials used in bellows gauges make them resistant to corrosive elements, a critical factor in ensuring operational integrity in aggressive chemical processing environments.
5. Electronic Differential Pressure Gauges
As the industrial landscape evolves with technological advances, electronic differential pressure gauges offer enhanced capabilities through digital readouts and integrate with other systems for improved data collection and analysis. These gauges provide real-time monitoring and the ability to transmit data remotely, which is beneficial for operations requiring continuous oversight. The inclusion of advanced sensor technology ensures high levels of precision, making these gauges ideal for complex environments such as aerospace or telecommunications. Their implementation offers unmatched accuracy and adaptability, reflecting modern industry's move towards more intelligent and interconnected systems.
Selecting the most appropriate differential pressure gauge necessitates a thorough understanding of the application's specific requirements. Factors such as the type of media, operating pressure range, environmental conditions, and necessary accuracy levels should all significantly influence the decision-making process. Consulting with specialists who offer authoritative advice and sector-specific expertise can aid in choosing a gauge that not only meets but exceeds operational expectations. These experts, with their deep knowledge and experience, often provide insights that can preemptively address potential complications, ensuring that the gauge will function optimally over its lifespan.
Trustworthiness is further enhanced through collaboration with reputable manufacturers and suppliers who adhere to stringent quality standards and industry regulations. Their commitment to reliability and safety guarantees that the gauges are not only effective but also compliant with the latest industry benchmarks.
Ultimately, the careful selection and implementation of differential pressure gauges can dramatically impact system efficiency, safety, and reliability. Making informed decisions, backed by expertise and robust data, ensures that the chosen device is indispensable in the sophisticated toolkit of modern industrial operations.