In the realm of industrial measurement tools, the pressure gauge diaphragm type stands out as a sophisticated instrument tailored to meet the most stringent demands of various sectors, including chemical processing, pharmaceuticals, and food and beverage industries. Its unique attributes position it as a critical component in precision and reliability for pressure monitoring.
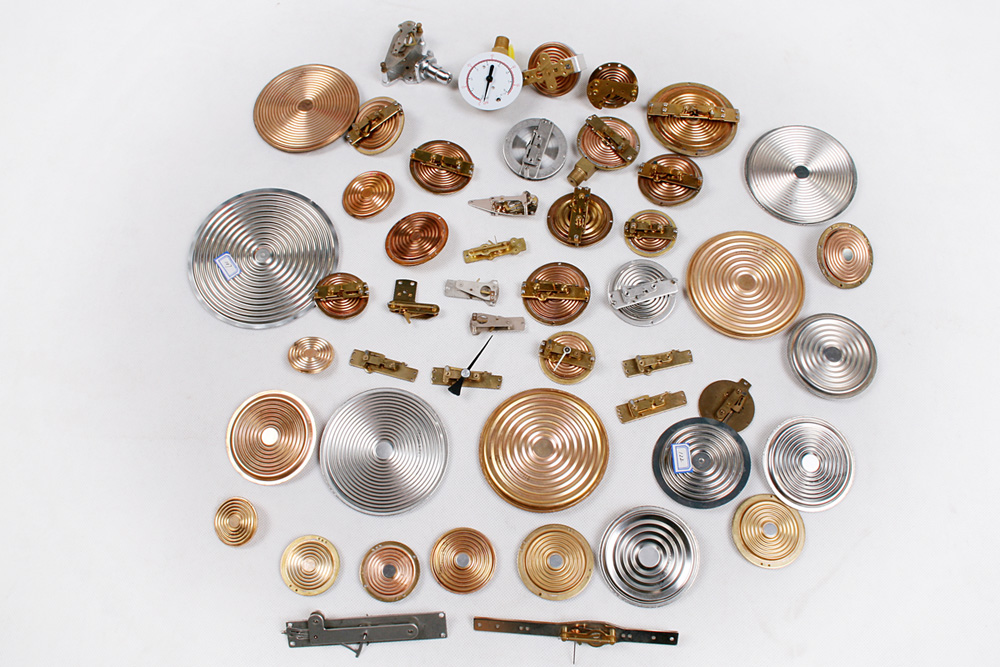
At its core, the diaphragm pressure gauge utilizes a thin, flexible membrane, typically made from robust materials like stainless steel or PTFE, which separates the measurement media from the pressure-sensing element. The membrane undergoes deformation proportional to the pressure difference across it, translating mechanical motion into an accurate pressure reading. This ingenious design not only facilitates precise pressure measurements but also enhances the longevity and safety of the gauge by preventing contact with corrosive or harmful media.
The expertise involved in the production and calibration of diaphragm pressure gauges is evident in the precision engineering and meticulous craftsmanship employed. Manufacturers like Wika, Ashcroft, and Endress+Hauser spearhead this space, offering a range of models tailored to specific operational needs. Their commitment to high standards is evident through rigorous testing and adherence to international standards like ASME B40.100 and EN 837. This rigorous approach ensures that each gauge provides consistent performance even in the most demanding conditions.
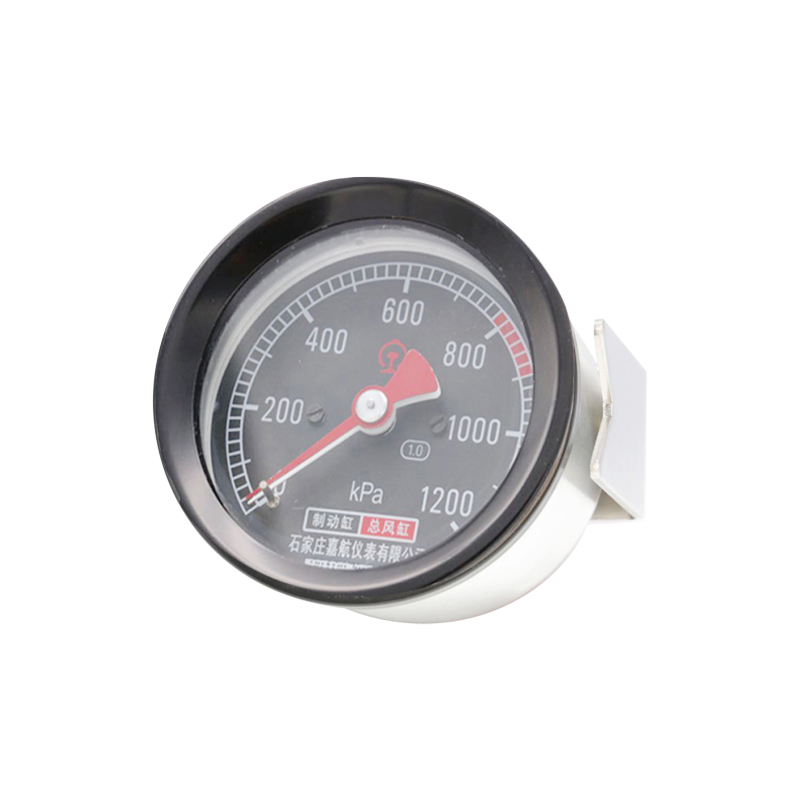
A diaphragm pressure gauge's authoritativeness is further reinforced by its widespread adoption across industries that prioritize safety and accuracy. In the pharmaceutical industry, for instance, these gauges are pivotal in maintaining sterile environments by isolating the pressure measuring element from the process fluid.
This prevents contamination, thereby safeguarding product integrity and patient safety.
pressure gauge diaphragm type
Trustworthiness of diaphragm pressure gauges is bolstered by their track record of reliability and accuracy. They are indispensable tools in critical applications such as ensuring the consistent and safe operation of steam systems, where precise pressure management is crucial to prevent catastrophic failures. The robustness of the diaphragm design means that even under extreme conditions, whether high pressure or aggressive media, the gauge remains steadfast, providing users with peace of mind and dependable data.
For engineers and technicians, the experience of using diaphragm pressure gauges translates into operational efficiency, reduced downtime, and significant cost savings. With features like overload protection and wide compatibility with various diaphragm seal types, these gauges optimize maintenance practices and enhance the workflow.
As pressure gauge diaphragm types continue to evolve, innovations like smart technology integration are setting new benchmarks. Modern variants now come equipped with digital displays and connectivity features, allowing for remote monitoring and data analysis. This smart functionality transcends traditional limitations and provides users with real-time insights, empowering more informed decision-making processes.
In conclusion, the pressure gauge diaphragm type epitomizes excellence in industrial pressure measurement, owing to its expert craftsmanship, authoritative presence across industries, and unwavering trustworthiness. It is a testament to engineering ingenuity and remains a cornerstone of safety and precision in modern industrial applications. As technology advances, its role is set to expand, promising even greater contributions to industrial efficiency and innovation.