Differential and absolute pressure gauges are essential tools used in various industries to measure pressure differences and pressure relative to a perfect vacuum. Understanding the high-quality differences between these two types of gauges can guide professionals in selecting the right tool for specific applications, ensuring accuracy, efficiency, and safety.
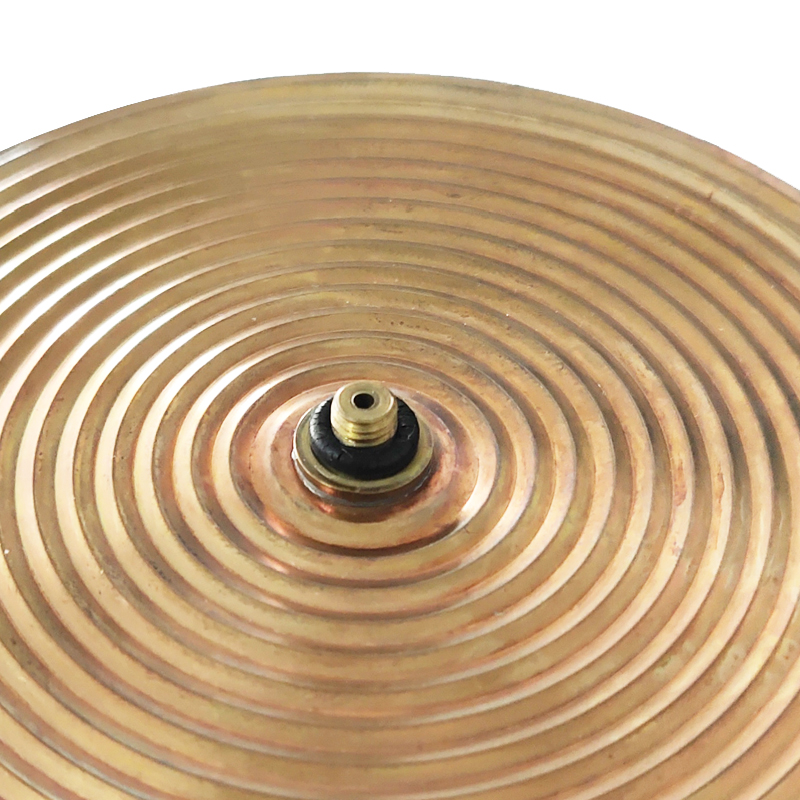
Differential pressure gauges measure the difference between two pressure points within a system, making them integral in applications where precise monitoring of pressure fluctuations is necessary. These gauges are critical in systems where maintaining a specific pressure differential is essential, such as in filtration processes. High-quality differential pressure gauges are often characterized by their ability to provide reliable readings in harsh conditions. They are constructed with robust materials such as stainless steel, which resist corrosion and withstand high temperatures and pressures. This ensures durability and longevity, even in demanding environments.
On the other hand, absolute pressure gauges measure pressure relative to a perfect vacuum, serving as a crucial tool in applications where atmospheric pressure changes could affect readings. They are widely used in meteorology, aeronautics, and certain manufacturing processes where precise pressure measurements are required irrespective of environmental changes.
A high-quality absolute pressure gauge is defined by its precision and stability. These gauges frequently employ advanced sensor technologies, such as ceramic capacitive sensors, which offer superior accuracy and stable performance over long periods. This technology minimizes the drift that can occur with temperature fluctuations or mechanical stress, ensuring consistent and accurate pressure measurements.
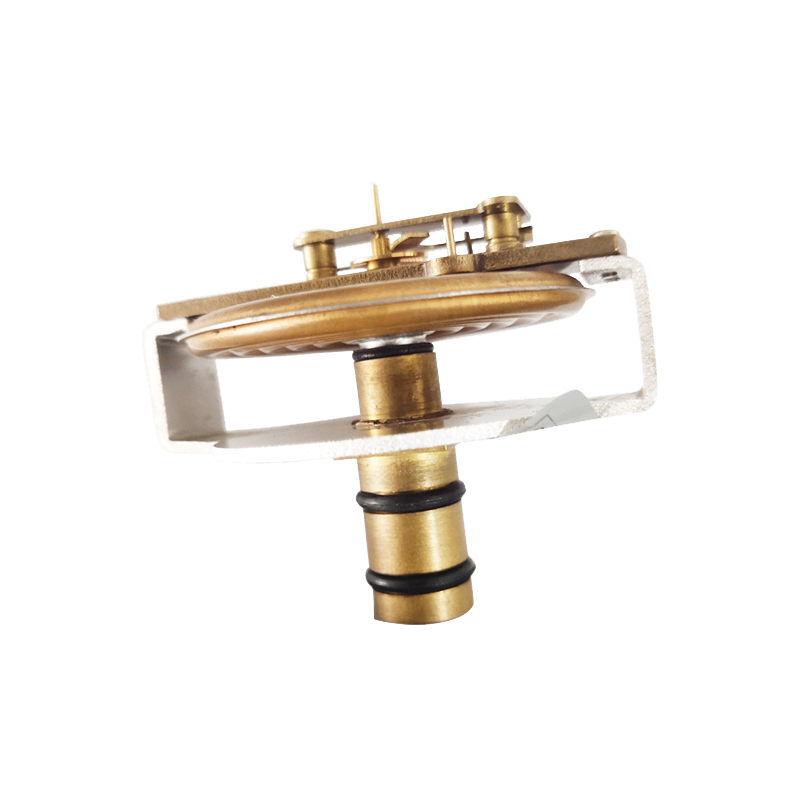
When considering the differences in functionality, differential pressure gauges excel in real-time monitoring and control of pressure variations in dynamic systems. For instance, in industrial processes where fluid flow maintenance is crucial, these gauges assist in identifying blockages or leaks by measuring the pressure drop across filters or pumps. This capability not only ensures system efficiency but also plays a pivotal role in preventive maintenance, thereby reducing downtime and operational costs.
high quality difference between differential and absolute pressure gauges
Conversely, absolute pressure gauges are indispensable in settings where external conditions vary and thus could influence gauge readings. Their ability to provide true pressure readings irrespective of ambient pressure changes makes them vital in research and development environments, where precise data is critical. For example, in the development of pressurized weather balloons or aerospace applications, absolute pressure gauges ensure that pressure measurements are unaffected by altitude-induced atmospheric pressure changes, thereby providing reliable data for scientific and engineering purposes.
In choosing between these two types of gauges, professionals should consider several factors the nature of the process, environmental conditions, and the specific requirements for accuracy and reliability. While both types of gauges are engineered for precision, their applications can differ significantly. For processes where differential pressure monitoring is required, selecting a high-quality differential gauge that can withstand environmental challenges while providing accurate readings is crucial. Meanwhile, for applications necessitating absolute pressure readings, an investment in high-quality absolute gauges equipped with advanced sensor technologies will ensure accuracy and longevity.
Expert opinions in the industry emphasize the importance of understanding the unique operational demands of each application before selecting a gauge. Engage with manufacturers and suppliers who offer customization and provide technical support to tailor the gauges to meet specific operational needs. Professionals should also seek out devices tested to international standards, such as those certified by the American Society of Mechanical Engineers (ASME) or the International Organization for Standardization (ISO), which ensure adherence to quality and safety standards.
Thus, selecting the appropriate pressure gauge—be it differential or absolute—based on an informed understanding of the distinct functional and high-quality attributes of each can significantly impact operational efficiency and safety across various industries. Making an informed decision supports not only the accuracy of measurements but also enhances the reliability and performance of complex systems.