Understanding the Parts of a Diaphragm Pressure Gauge in Factory Settings
A diaphragm pressure gauge is an essential tool in various industrial applications where precise pressure measurement is crucial. These gauges are specifically designed to measure low to moderate pressures and find wide usage in chemical, pharmaceutical, and food processing factories. To fully comprehend their functionality, it's vital to understand the different parts that make up this precision instrument.
1. **Diaphragm** The heart of the diaphragm pressure gauge is the diaphragm itself. It's a thin, flexible membrane that deforms under pressure. When pressure is applied to one side, the diaphragm flexes, causing a change in its position. This movement is directly proportional to the applied pressure and is used to indicate the pressure reading.
2. **Case** The sturdy case houses and protects the internal components of the gauge. It is usually made from materials like stainless steel or brass, providing resistance against corrosion and mechanical damage in harsh factory environments.
3. **Bourdon Tube** Although not present in all diaphragm gauges, some models incorporate a bourdon tube, a coiled metal tube that expands when pressurized. The expansion drives the pointer mechanism, converting mechanical movement into a readable pressure value.
4. **Pointer and Dial** The pointer is the visible element that moves across the dial as the pressure changes. The dial, marked with numerical values, indicates the pressure reading The dial, marked with numerical values, indicates the pressure reading
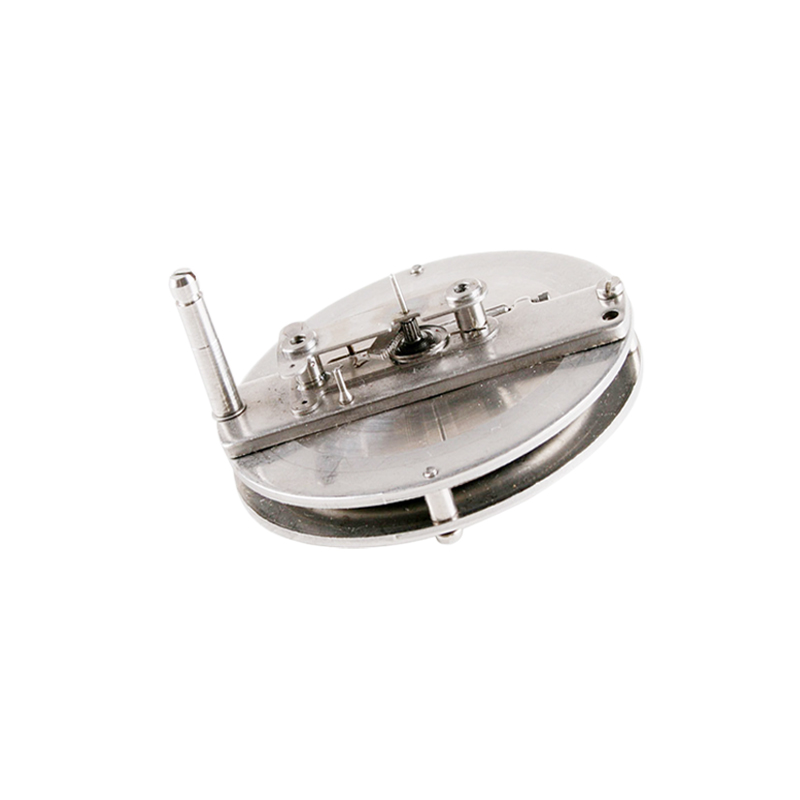
The dial, marked with numerical values, indicates the pressure reading The dial, marked with numerical values, indicates the pressure reading
parts of diaphragm pressure gauge factory. It's crucial for the pointer to be clear and accurate to ensure reliable readings in a factory setting.
5. **Connection Fittings** These are the points where the gauge connects to the system being monitored. They come in various sizes and types, such as NPT, BSP, or flare fittings, to adapt to different pipeline configurations in the factory.
6. **Movement Mechanism** This is the internal mechanism that translates the diaphragm's movement into the pointer's rotation on the dial. It typically includes a gear train that amplifies the small deflection of the diaphragm for more significant and accurate dial movement.
7. **Backplate and Seal** The backplate provides structural support for the internal components, while the seal ensures the integrity of the gauge by preventing any leakage or contamination between the measured medium and the gauge's internal mechanism.
8. **Compensating Springs** In some advanced designs, compensating springs are used to adjust for temperature changes, ensuring the accuracy of the pressure reading even in fluctuating factory conditions.
Understanding the parts of a diaphragm pressure gauge is critical for proper installation, maintenance, and troubleshooting. Regular inspection and calibration are necessary to maintain the gauge's accuracy and reliability in factory operations. With its precision and durability, the diaphragm pressure gauge remains an indispensable tool in monitoring and controlling pressure in various industrial processes.