In the complex world of industrial instrumentation, selecting the right pressure gauge can be a daunting task. The diaphragm capsule pressure gauge is one such device that stands out for its reliability, precision, and suitability in measuring low-pressure applications. As industries continue to evolve, understanding the dynamics and capabilities of diaphragm capsule pressure gauges is imperative for ensuring optimal performance.
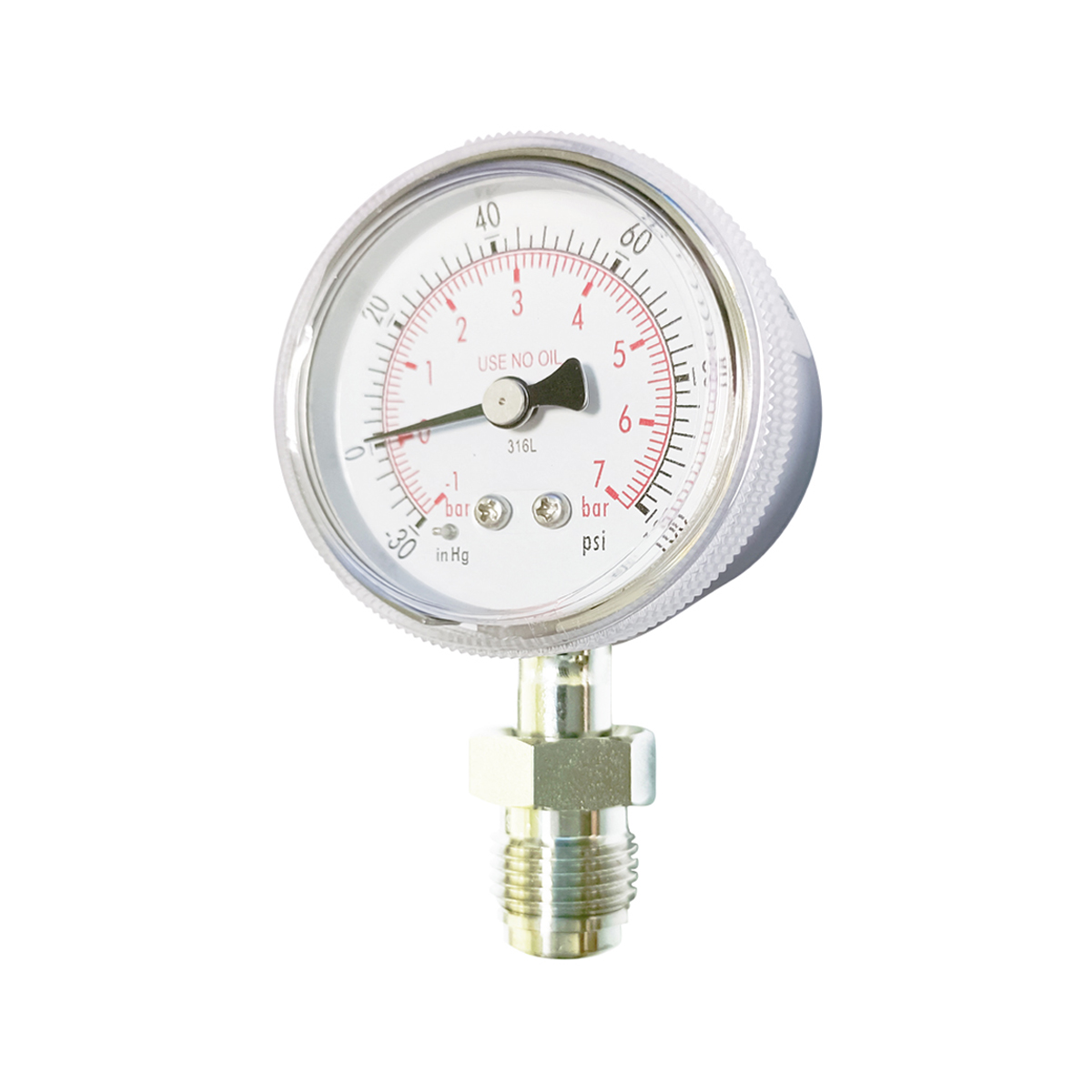
To unravel the expertise of using diaphragm capsule pressure gauges, it's essential to delve into their construction and operational framework. Unlike conventional pressure gauges, diaphragm capsule versions employ a twin-disk diaphragm mechanism. The diaphragm is usually made from corrosion-resistant materials such as stainless steel or Inconel, ensuring long-term durability and precision in harsh environments. The unique design allows these gauges to measure pressures from zero to a few hundred psi, which makes them ideal for low-pressure scenarios where accuracy is paramount.
A crucial advantage of diaphragm capsule pressure gauges is their versatility across various industries. From pharmaceuticals, where sterile conditions and precise measurements are crucial, to chemical processing plants, where exposure to aggressive media is inevitable, the applicability is vast. Their ability to provide accurate differential pressure readings without fluid fill, which could otherwise contaminate sensitive processes, makes these gauges indispensable in critical applications such as clean rooms or laboratories.
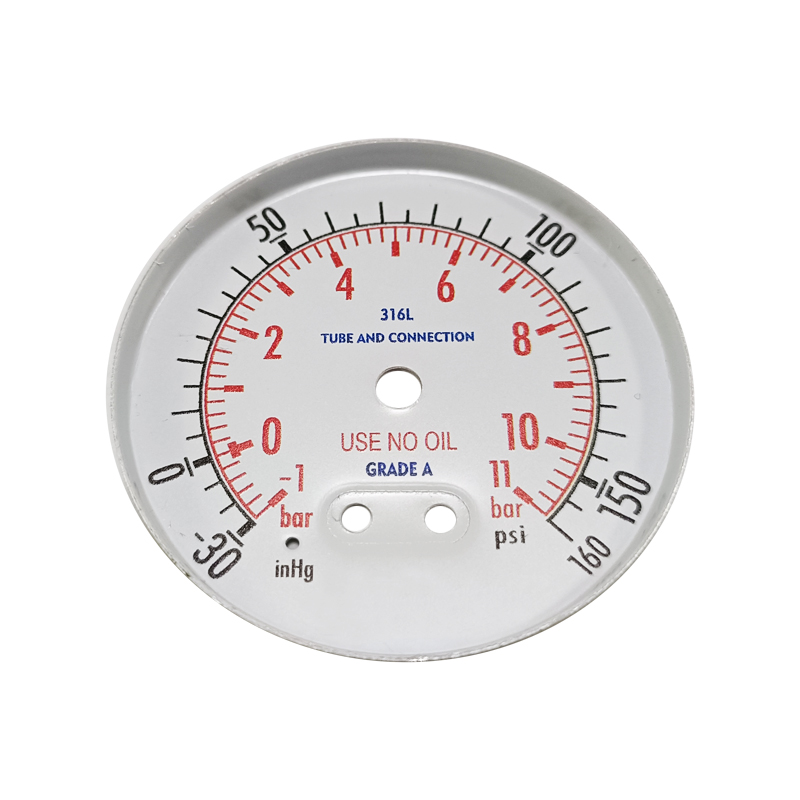
When considering the authoritativeness of diaphragm capsule pressure gauges, it is important to note their compliance with stringent industry standards, such as ASME B40.100. This standard ensures that the gauges deliver reliable readings and maintain consistency over extended periods. Furthermore, their design often incorporates overload protection, which prolongs the service life of the gauges by preventing damage from sudden pressure spikes.
diaphragm capsule pressure gauge,
Experience with diaphragm capsule pressure gauges reveals their low maintenance requirements and ease of integration into existing systems. Installation typically involves connecting the gauge to the process system using standard mounting options, and because they operate without need for external power, they provide an efficient solution for continual monitoring. Additionally, modern iterations of these gauges now incorporate digital display options, which enhance readability and allow for integration with digital monitoring systems, catering to the growing need for smart, connected industrial environments.
Trustworthiness is engendered through the accuracy and repeatability of readings provided by diaphragm capsule pressure gauges. Trusted manufacturers often offer calibration services to verify and fine-tune these instruments, further enhancing their reliability. Routine maintenance checks, including inspection of seals and the measuring element, are recommended to sustain performance.
In conclusion, diaphragm capsule pressure gauges offer an unparalleled combination of precision, durability, and adaptability across various sectors. While they excel in measuring low pressures accurately, their robust construction ensures they stand up to the challenges posed by today’s demanding industrial settings. For businesses seeking reliable pressure measurement solutions, diaphragm capsule pressure gauges represent a sound investment that aligns with the principles of experience, expertise, authoritativeness, and trustworthiness. By incorporating these gauges into their processes, companies not only enhance operational efficiency but also bolster the quality and safety of their output.