High quality precision instruments, particularly pressure gauges, serve as essential components across various industries, ensuring the reliable and accurate measurement of pressure in myriad applications. Given the indispensable role they play in maintaining operational efficiency and safety, understanding their use and the expertise behind their production is vital.
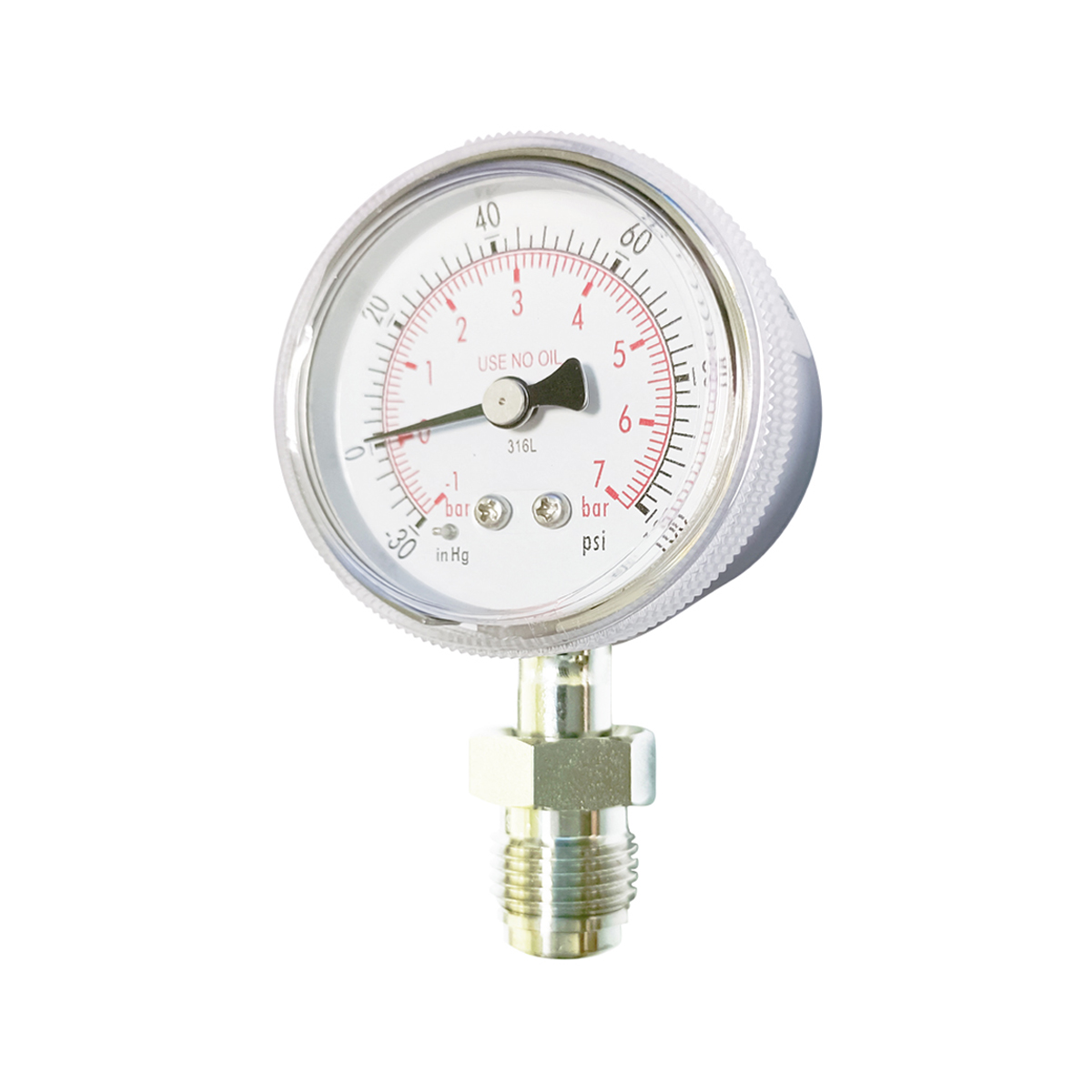
Pressure gauges, crafted with unparalleled precision, are quintessential for environments where meticulous monitoring and control are paramount. These precision instruments are not merely tools but are the backbone of operational stability in sectors like manufacturing, aerospace, and pharmaceuticals, to name a few.
A high-quality pressure gauge is intricately designed to deliver pinpoint accuracy. The craftsmanship involved echoes extensive expertise and a deep understanding of the demands posed by different industry segments. Engineers and designers work in concert, employing cutting-edge technology and advanced materials to enhance the durability and performance of these gauges.
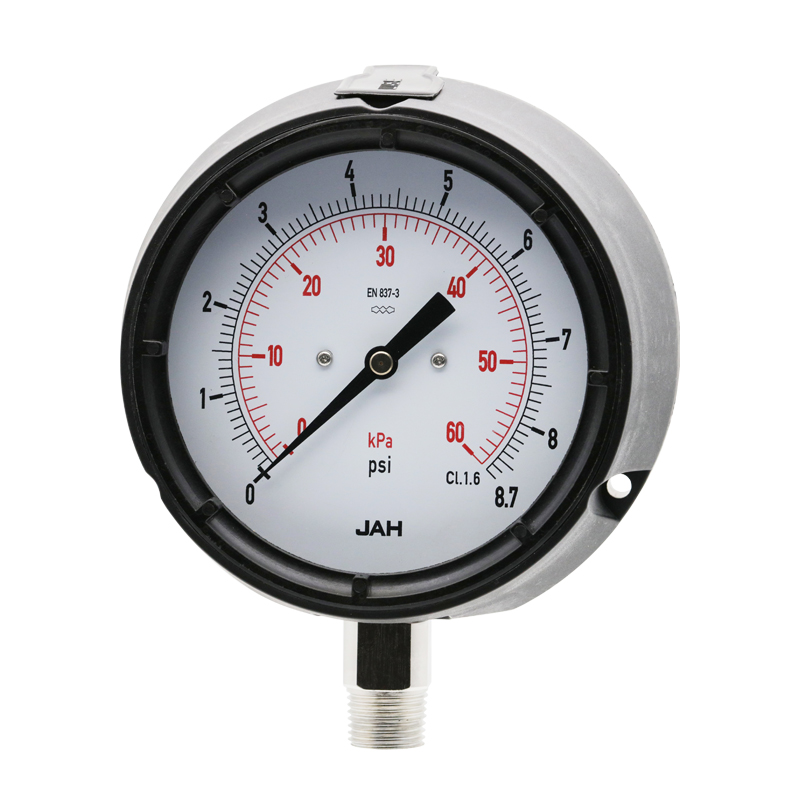
Central to the efficacy of pressure gauges is their ability to provide reliable readings under extreme conditions. In aerospace applications, for instance, the need for precision is heightened by the stakes involved. Here, a subtle deviation in pressure measurement could lead to catastrophic outcomes. The precision instruments used must boast exceptional resistance to environmental variables while maintaining accuracy in their readings. Manufacturers of high-quality pressure gauges invest heavily in research to innovate materials and designs that withstand such intense conditions.
The pharmaceutical industry also relies heavily on these precision instruments. Ensuring the correct pressure conditions in pharmaceutical processes is crucial for maintaining the integrity of products and regulatory compliance. The gauges used must exhibit not only precision but also a high degree of repeatability and reliability. This requirement underscores the importance of expertise in their design and manufacture—a process that integrates technological advancement with rigorous testing protocols to meet strict industry standards.
high quality precision instruments pressure gauge
Authoritativeness in the realm of precision instruments is not attained overnight. It is the result of decades of research, development, and continuous refinement. Manufacturers establish authority by adhering to global standards such as ISO 9001 and other industry-specific certifications that vouch for quality and reliability. Furthermore, they often collaborate with industry bodies and partake in developing new standards that push the boundaries of precision and quality.
Trustworthiness in pressure gauge manufacturing is cemented through transparent practices and a customer-centric approach. This involves providing detailed post-sales support and warranties that assure clients of the gauge's longevity and performance. Companies also invest in building a knowledgeable workforce capable of addressing technical queries that clients might encounter.
Moreover, customer testimonials and case studies serve as powerful testimonials to a gauge's performance, offering potential buyers a glimpse into real-world applications and the benefits reaped from choosing high-quality precision instruments. The narrative of reliability extends into the supply chain, where manufacturers optimize processes to ensure the swift and safe delivery of products worldwide.
In summary, high-quality precision instruments like pressure gauges represent an intersection of unparalleled expertise, cutting-edge technology, and rigorous quality control. They are the lifeline in many industries, providing the necessary precision that ensures safety, compliance, and operational efficiency. The pursuit of excellence in their manufacture is a testament to the importance placed on experience, authority, and trustworthiness, underscoring their role as indispensable tools in the modern industrial landscape.