Differential and absolute pressure gauges are integral instruments widely used in various industries to measure pressure. Despite their shared function of pressure measurement, they cater to distinct applications and exhibit notable differences in operation and design.
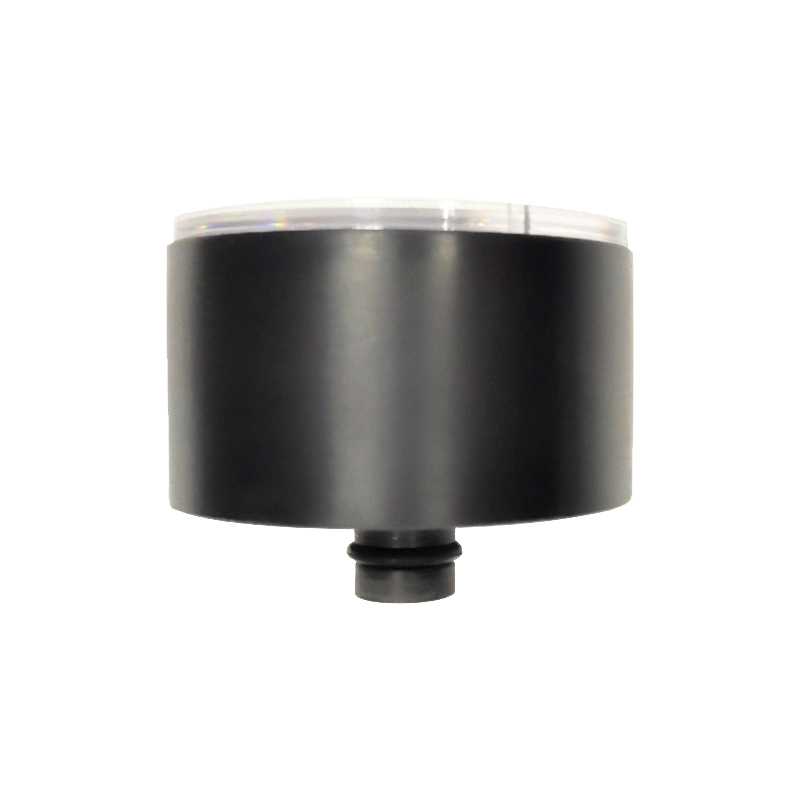
Differential pressure gauges measure the difference in pressure between two points, providing critical data needed in monitoring and control systems. They are crucial in applications where understanding the pressure drop across equipment, such as filters, pumps, or flow elements, is vital for efficiency and safety. For instance, in a filtration system, tracking the differential pressure across the filter helps determine when maintenance or filter replacement is necessary. These gauges are often preferred in systems where pressure comparison is more valuable than measuring a single point of absolute pressure.
On the other hand, absolute pressure gauges measure pressure relative to a perfect vacuum. They are essential in applications where atmospheric pressure changes could significantly affect the process, such as in vacuum systems or altitude-sensitive operations. Because they account for the pressure exerted by the atmosphere, absolute pressure readings remain constant regardless of elevation changes or weather variations, providing a more consistent and reliable measurement in specific environments. This feature is crucial for industries like aerospace and in laboratories where precise pressure measurements are necessary to avoid compromising experiments or operations.
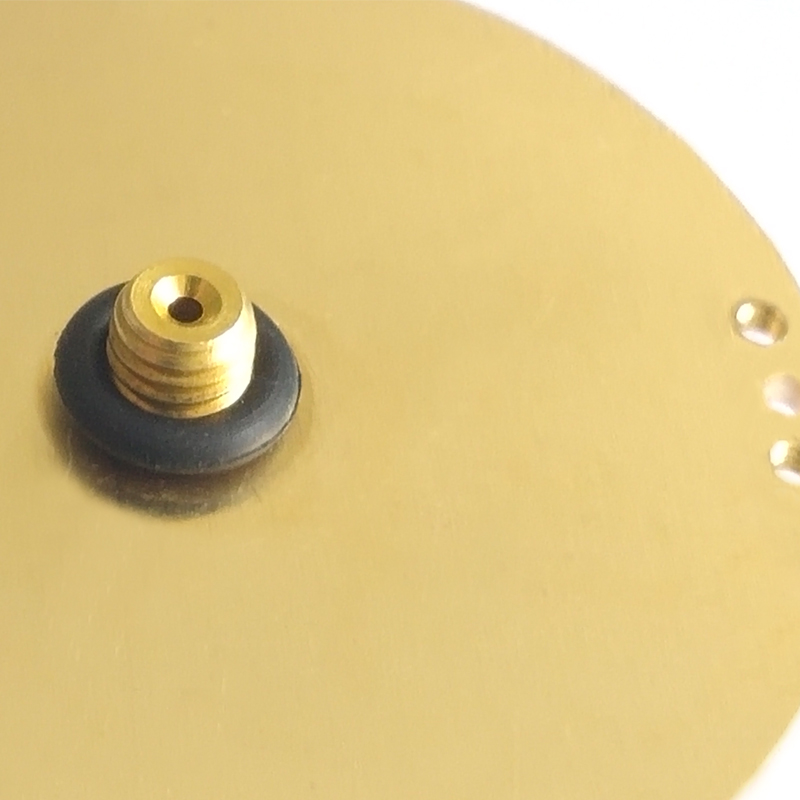
When selecting between differential and absolute pressure gauges, one must consider the application's demands. Differential pressure gauges are typically more suitable for closed systems and applications involving fluid dynamics, where pressure drops can indicate flow efficiency or filter status. They are designed with two ports for connection, enabling them to provide real-time information about pressure variations between two separate points. In contrast, absolute pressure gauges, with their ability to measure against a vacuum baseline, are ideal for open systems exposed to the external atmosphere, ensuring stable performance across varying environmental conditions.
The structural design of these gauges also differs to accommodate their specific functionalities. Differential pressure gauges often incorporate diaphragms, bellows, or bourdon tubes connected in opposition to maintain stability and improve measurement accuracy under different conditions. The complexity of these designs allows them to deliver precise readings even in high-pressure environments by balancing the force exerted on both sides. Meanwhile, absolute pressure gauges might include a sealed enclosure from which the reference vacuum is maintained, allowing them to offer stability and immunity to pressure fluctuations caused by atmospheric changes.
oem difference between differential and absolute pressure gauges
Trustworthiness and reliability push these devices to excel in their respective areas. For industries such as chemical manufacturing, oil and gas, and HVAC, the choice between differential and absolute pressure gauges directly impacts the efficiency, safety, and cost-effectiveness of operations. Regular calibration and maintenance practices are essential to ensure their viability, often involving rigorously adhering to manufacturer specifications and industry standards.
In terms of expertise, manufacturers usually provide detailed guidance on gauge selection based on the specific requirements of pressure range, process conditions, material compatibility, and desired accuracy. Industry professionals often rely on these specifications and consult with experts to ensure the optimal integration of pressure gauges within their systems. Furthermore, leveraging advanced technologies such as digital displays and wireless connectivity has become standard practice to enhance precise readings and remote monitoring capabilities.
Authoritativeness in selecting pressure gauges lies in understanding basic principles of pressure measurement and tailoring choices to specific industrial needs. With technological advancements, pressure gauges have evolved to become more sophisticated and application-specific, allowing for enhanced data analytics and predictive maintenance strategies.
In conclusion, distinguishing between differential and absolute pressure gauges boils down to application needs, environmental conditions, and accuracy requirements. By understanding these differences, industries can leverage the strengths of each gauge type to optimize system performance, ensure safety, and enhance operational efficacy.