Differential pressure gauges are critical instruments used across various industries to measure the difference in pressure between two points. They play a vital role in maintaining system integrity, improving efficiency, and ensuring the smooth operation of processes. As a seasoned expert in the field, I have amassed considerable experience working with these instruments, and I am committed to sharing insights that enhance both the understanding and utilization of differential pressure gauges.
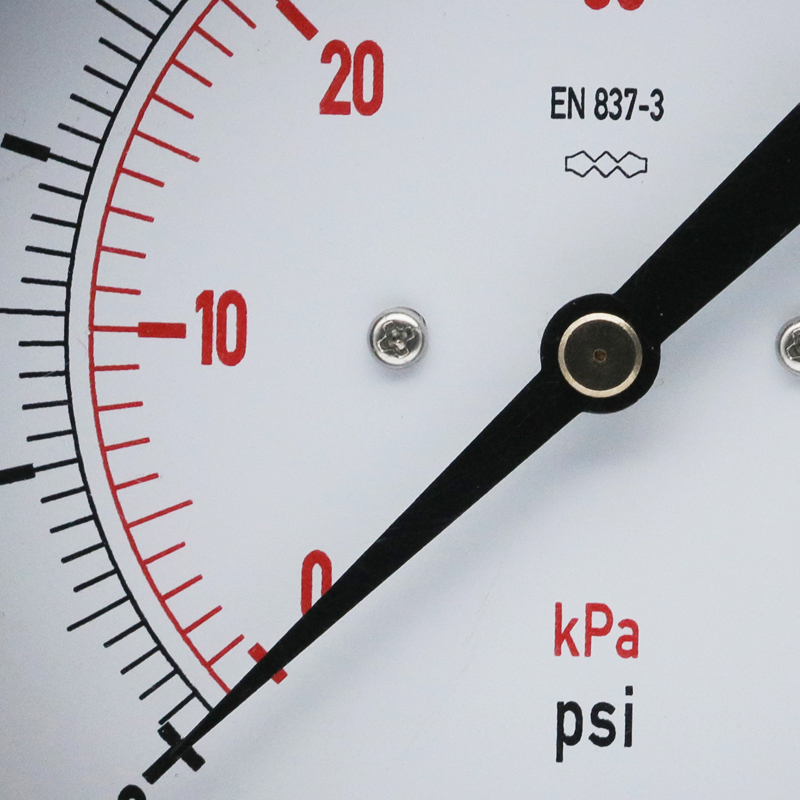
Differential pressure gauges are primarily used in versatile applications such as filtration, flow measurement, and level measurement. Industries ranging from HVAC, chemical processing, oil and gas, to water treatment, heavily rely on these devices to monitor and control differential pressure for enhanced process outputs.
Experience with these gauges reveals their indispensable role in filtration systems. For instance, they indicate when a filter is clogged and requires cleaning or replacement. By continuously measuring the pressure difference across the filter, they provide real-time data, preventing system inefficiencies or failures. My practical experiences have demonstrated that an optimally functioning differential pressure gauge reduces downtime, prolongs equipment lifespan, and supports predictive maintenance strategies.
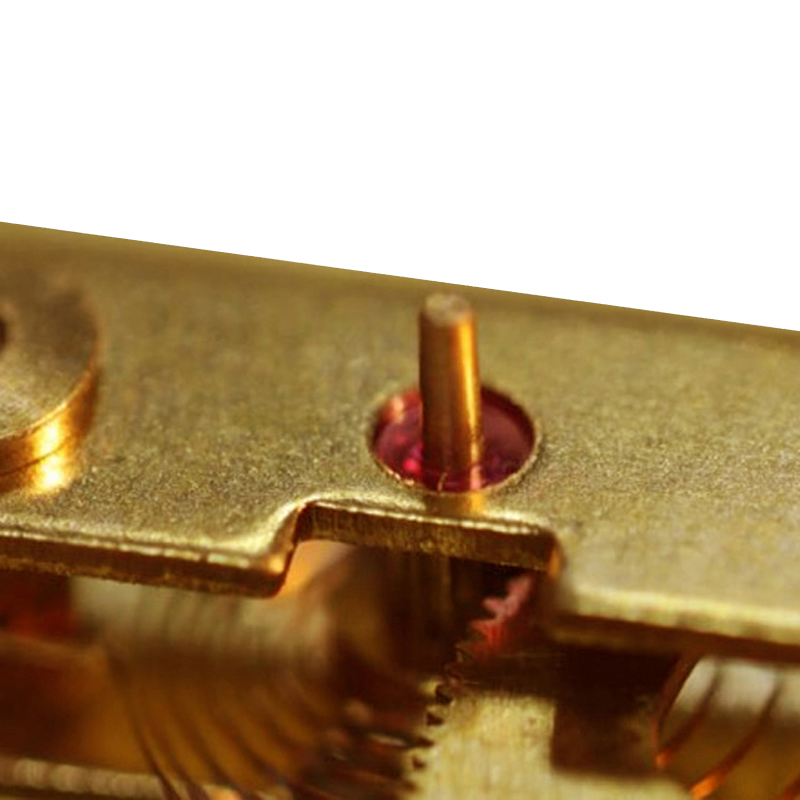
From an expertise standpoint,
selecting the right differential pressure gauge is crucial. Factors such as pressure range, fluid compatibility, and environmental conditions should be meticulously evaluated. There are various types of differential pressure gauges available, including piston, diaphragm, and bellows types, each suited for specific applications. Diaphragm-type instruments, for example, are widely preferred in applications involving corrosive fluids due to their robustness and durability.
differential pressure gauge,
Authoritativeness in the field of differential pressure measurement is established by comprehending the intricate details of these instruments. An in-depth understanding of their construction and operation enhances their applicability and efficacy. Typically, these devices consist of two inlet ports connected to the high and low-pressure sides. A pointer moves in response to the differential pressure, providing a visual indication on the scale. For digital versions, electronic transducers offer even greater precision and adaptability.
Building trust in the realm of differential pressure gauges derives from reliable performance and accuracy. Investing in high-quality instruments from reputable manufacturers is imperative. These gauges must meet stringent industry standards such as those set by the American Society of Mechanical Engineers (ASME) and should undergo regular calibration to maintain accuracy. Real-world applications in chemical and pharmaceutical industries demand uncompromised accuracy, where even minor discrepancies can lead to significant safety hazards or financial losses.
Furthermore, enhancing the trustworthiness of differential pressure gauges involves staying abreast of technological advancements. The Internet of Things (IoT) integration, for example, empowers these instruments with remote monitoring capabilities and advanced data analytics, providing valuable insights and proactive solutions.
In conclusion, differential pressure gauges are invaluable assets to industrial operations. Through comprehensive expertise, unwavering accuracy, and reliable performance, these instruments safeguard processes, promote efficiency, and uphold safety standards. A focus on experience, coupled with an authoritative approach, ensures optimal gauge selection and application, ultimately fostering trust and reliability in every industrial setting. Understanding these aspects is not just about operating effectively; it's about pushing the boundaries of what's possible in industrial measurement and control.