OEM analogue differential pressure gauges have emerged as indispensable tools in various industrial applications, offering precise measurements crucial for maintaining operational efficiency. With decades of engineering advancement behind these devices, their relevance continues to grow, driven by the need for accuracy and reliability in dynamic environments.
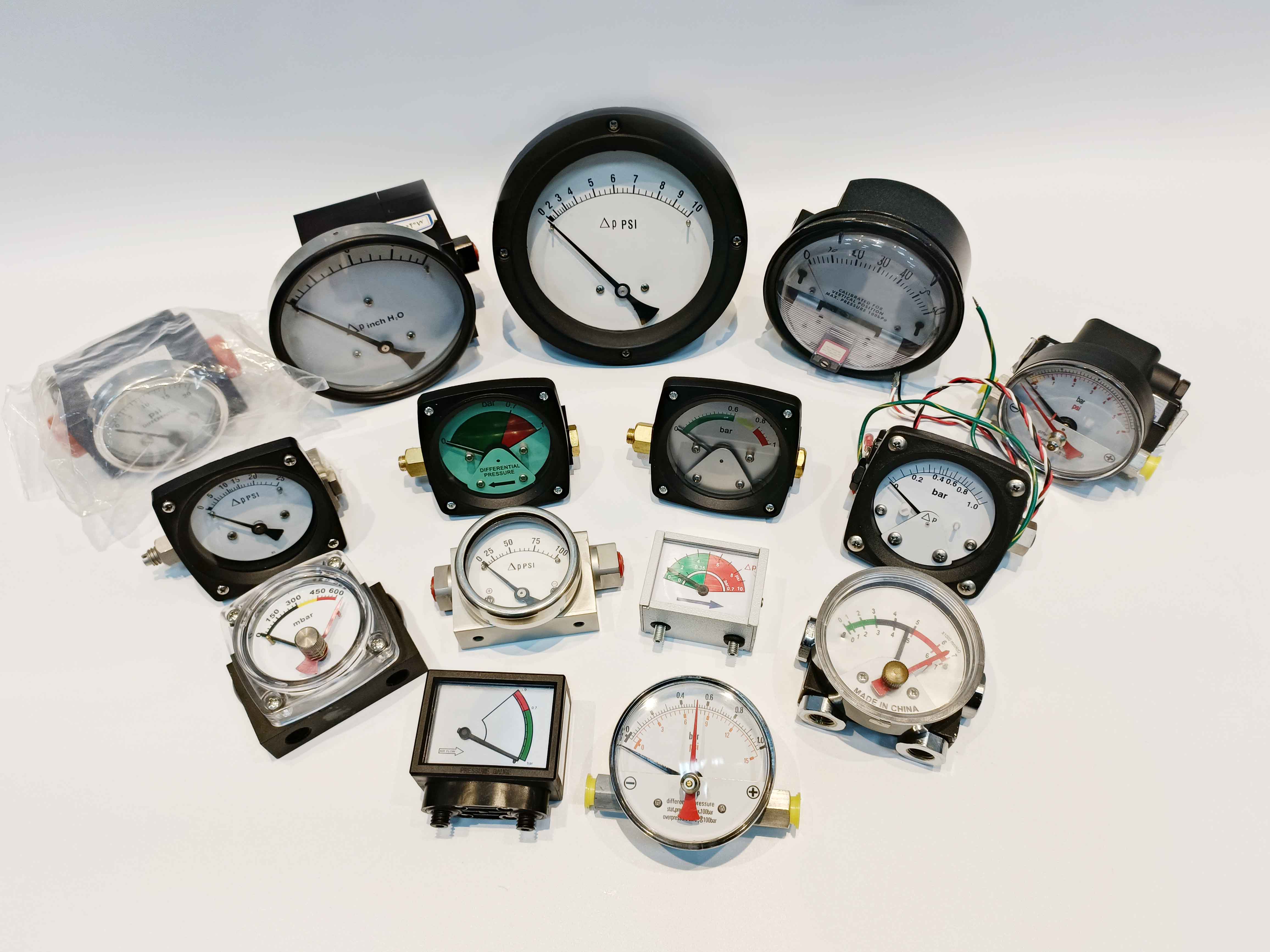
The effectiveness of analogue differential pressure gauges primarily hinges on their mechanical simplicity and ease of integration into existing systems. Unlike digital counterparts, analogue gauges provide a continuous readout, ensuring that operators can intuitively monitor pressure variations in real-time. This ability to deliver immediate feedback enhances decision-making processes in industries such as petrochemical, pharmaceutical, and HVAC (Heating, Ventilation, and Air Conditioning).
Experience with these instruments has shown that their robustness and durability make them suitable for use in harsh environmental conditions where electronic devices might fail. For instance, in sectors dealing with high-temperature processes or corrosive materials, OEM analogue differential pressure gauges prove invaluable. They can withstand significant physical stress without compromising the accuracy of pressure readings, which is crucial for maintaining system integrity and preventing potential failures.
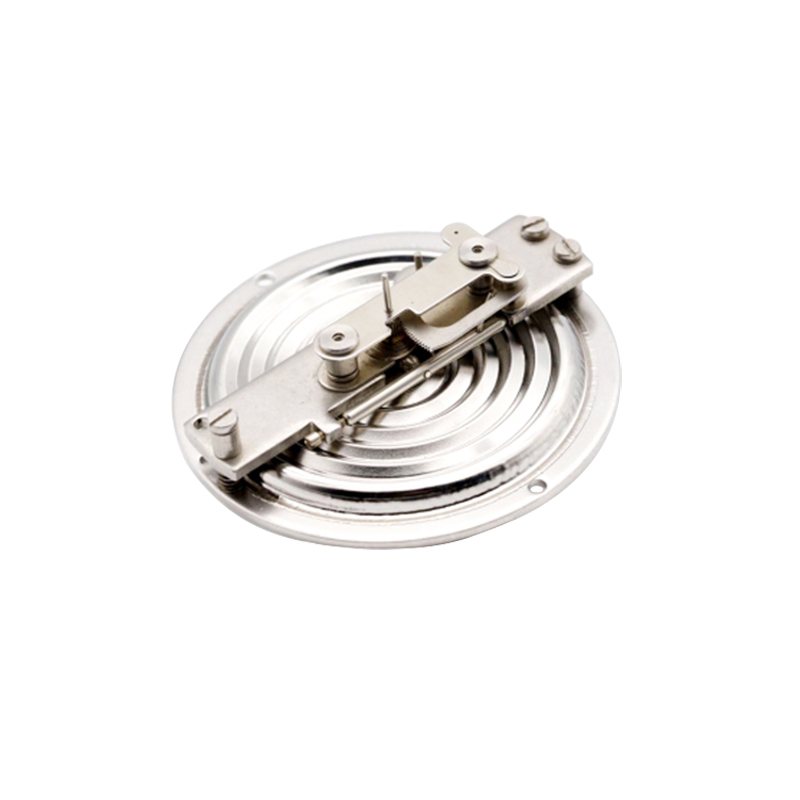
From a technical expertise standpoint, the precision engineering involved in the design of these gauges ensures high reliability. The core mechanism, often consisting of a bourdon tube or diaphragm, is crafted to respond accurately to pressure differences. Professionals in the field understand that selecting an OEM product implies that the gauge has been manufactured to meet specific standards and specifications. This assurance is particularly important for applications where precise pressure measurement can significantly impact product quality and safety.
Authoritativeness of OEM analogue differential pressure gauges is further reinforced by their widespread adoption across industries. Trusted manufacturers with a long-standing history of excellence provide these instruments, ensuring that they comply with international standards such as ISO 9001 for quality management systems. This compliance not only guarantees performance but also facilitates easier maintenance and calibration due to standardized processes and compatible parts.
oem analogue differential pressure gauge
Trustworthiness in the use of analogue differential pressure gauges is integral to their continued prevalence. Many industries depend on historical data accumulated over years of gauge usage to forecast trends and prevent operational anomalies. Users and operators have come to trust the consistency offered by analogue readings, appreciating that these gauges provide a level of reliability needed for critical operations.
In choosing OEM analogue differential pressure gauges, companies are investing in instruments that offer long-term value through unparalleled reliability and ease of use. When paired with expert installation and regular maintenance, these gauges can serve as a cornerstone of efficient operation and risk management in industrial settings.
As technology continues to advance,
the role of analogue differential pressure gauges remains significant. Their seamless integration with other industrial systems and resilience under challenging conditions ensure their position as a critical component in monitoring and maintaining industrial processes.
In conclusion, the continued reliance on OEM analogue differential pressure gauges is a testament to their effectiveness, reliability, and superior performance in real-world applications. Their ability to accurately measure, display, and withstand harsh conditions makes them a preferred choice across a spectrum of industries, supporting the smooth operation and safety of critical industrial processes.