Differential pressure gauges are indispensable tools in numerous industries, facilitating accurate measurement of pressure differences between two points. Leveraging years of industry knowledge, these gauges play a crucial role in ensuring optimal operational efficiency and safety in various applications such as filtration, flow measurement, and process control.
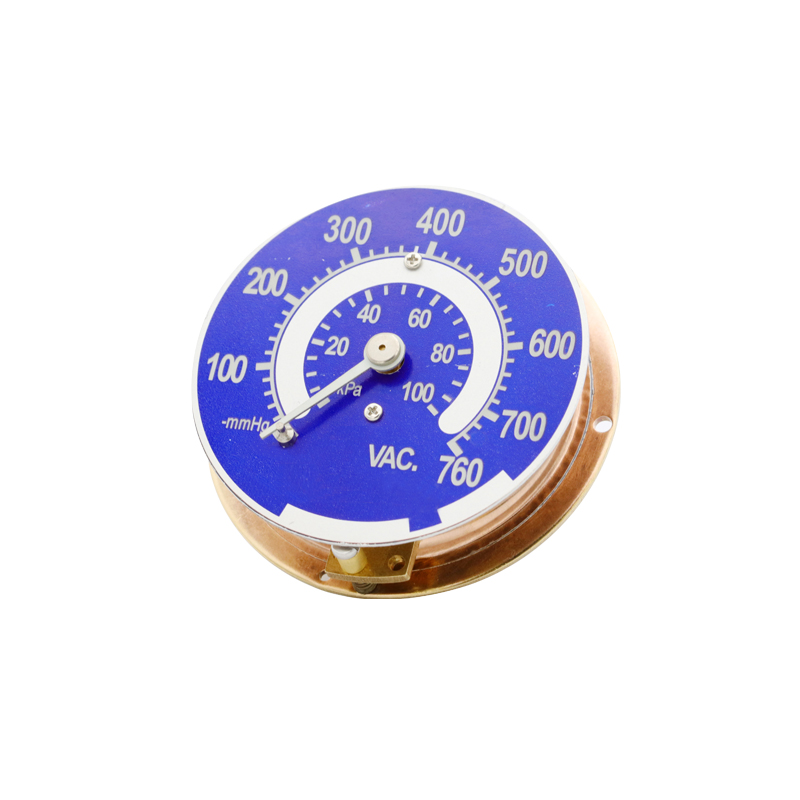
In numerous industrial scenarios, maintaining precise pressure levels is paramount. Differential pressure gauges, known for their reliability and precision, help monitor and control processes by indicating the difference in pressure across filters, pumps, or system components. These gauges contribute significantly to preventative maintenance strategies by providing early warnings of potential issues like blockages or leaks, thus avoiding costly downtimes.
The functioning principle behind differential pressure gauges involves two pressure inputs—high and low. The gauge measures the difference between these inputs, providing critical data that informs operational decisions. For instance, in filtration systems, a rising differential pressure may indicate clogging, prompting timely filter replacements. Such applications showcase the expertise required to efficiently interpret data from these instruments for enhanced operational performance.
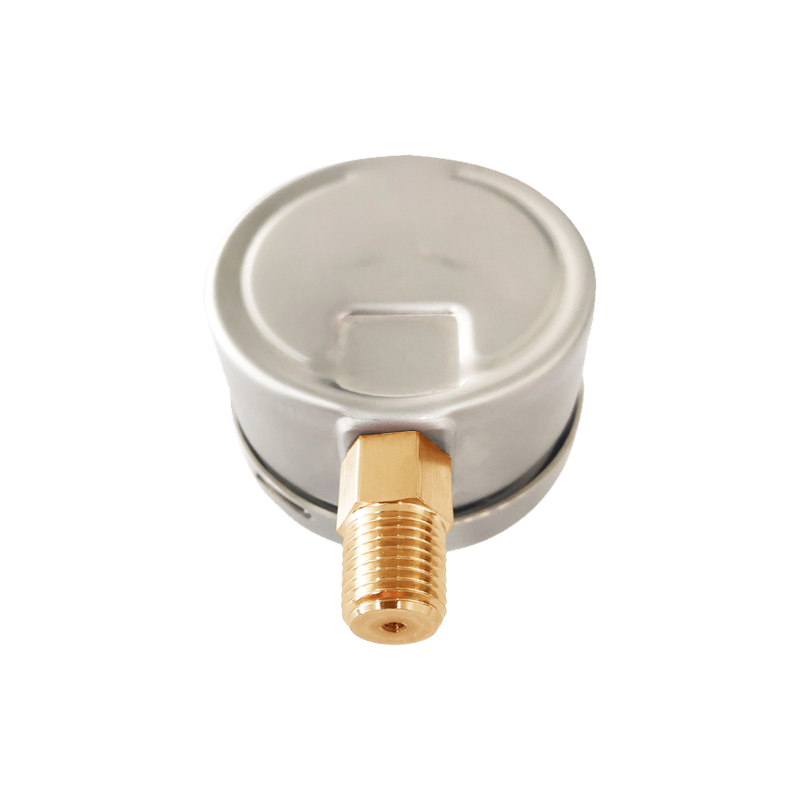
Accuracy and durability are defining features of a reliable differential pressure gauge. Leading manufacturers employ advanced design technologies that incorporate robust materials capable of withstanding harsh environmental conditions. Stainless steel and corrosion-resistant alloys are frequently used, ensuring the longevity of the gauges even in extreme settings. This reinforces the authority of differential pressure gauges in industries like oil and gas, where equipment reliability is non-negotiable.
differential pressure gauge,
Trustworthiness is a cornerstone of the relationship between suppliers of differential pressure gauges and their clientele. Providing calibration and maintenance services further enhances the trust in these tools. Regular calibration ensures that gauge readings remain accurate over time, maintaining the consistency necessary for critical industrial processes. Companies prioritizing calibration and maintenance solutions demonstrate commendable trustworthiness, as they ensure the reliability and safety of operational equipment.
Innovations continue to propel the differential pressure gauge industry forward, with digital advancements leading the way. Digital gauges equipped with smart features allow for remote monitoring and data logging, providing real-time insights and comprehensive analytics. This evolution not only enhances the user experience but also expands the expertise of system operators by facilitating data-driven decision-making.
Moreover, the integration of IoT technology into differential pressure gauges exemplifies the progressive strides towards smart industrial practices. IoT-enabled gauges offer seamless connectivity, integrating with broader industrial ecosystems to provide a holistic picture of system performance. Such technological advancements ensure these gauges remain authoritative instruments in modern industrial operations.
In conclusion, differential pressure gauges are essential, their advantages being multifaceted they enhance operational efficiency, support maintenance efforts, and adapt to technological advancements. Choosing the right gauge involves considering factors such as application requirements, environmental conditions, and service support—thus finding a perfect fit that assures process reliability and efficiency. By embracing the innovations in gauge technology, industries can pave the way for smarter, safer, and more efficient operations, underscoring the importance of these gauges as invaluable tools in the industrial toolkit.