In the world of industrial instrumentation and monitoring, the differential pressure gauge stands as a crucial component for ensuring effective process control and safety. This precision instrument offers an unparalleled method for measuring the pressure difference between two points, delivering vital data for industries ranging from petrochemical to water treatment.
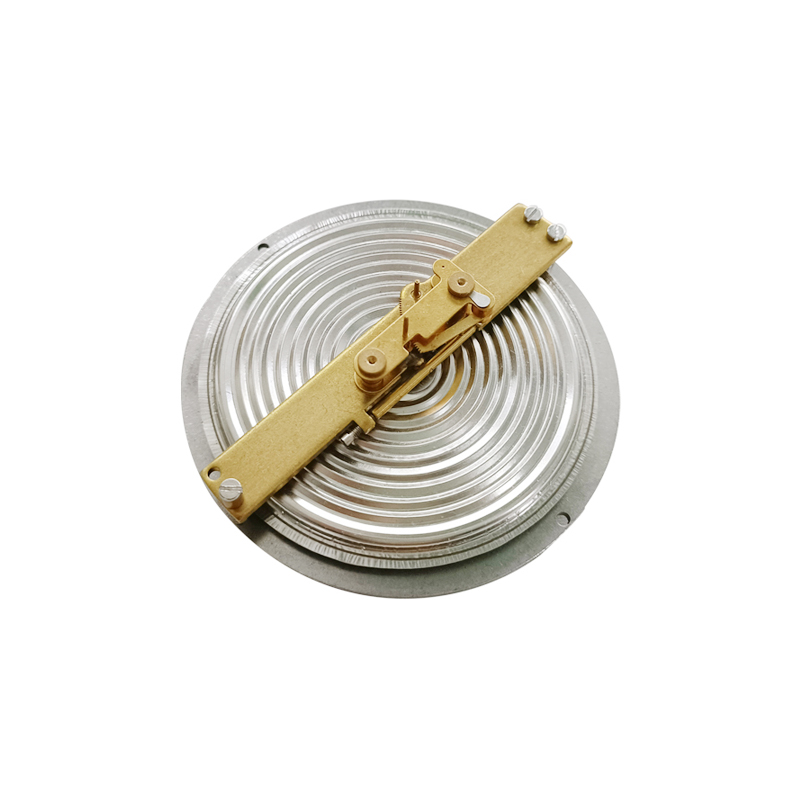
A differential pressure gauge operates on a relatively simple yet effective principle it measures the difference between pressures from two input sources. The gauge's design often incorporates diaphragm elements or bellows that respond to pressure changes, translating this force into a readable scale. A key advantage of using these gauges is their ability to provide continuous monitoring of filters, pumps, or process-critical operations without requiring an electrical power source, making them both efficient and reliable in diverse environments.
The expertise behind designing differential pressure gauges lies in understanding the specific requirements of various applications. For instance, when selecting a gauge for a corrosive chemical process, engineers might opt for materials such as stainless steel or Hastelloy, known for their resistance to harsh environments. Similarly, for ultra-precise applications,
a digital differential pressure gauge with high resolution and accuracy may be necessary. This careful consideration of application-specific factors ensures that the selected gauge offers optimal performance and longevity, reflecting the depth of expertise required in this field.
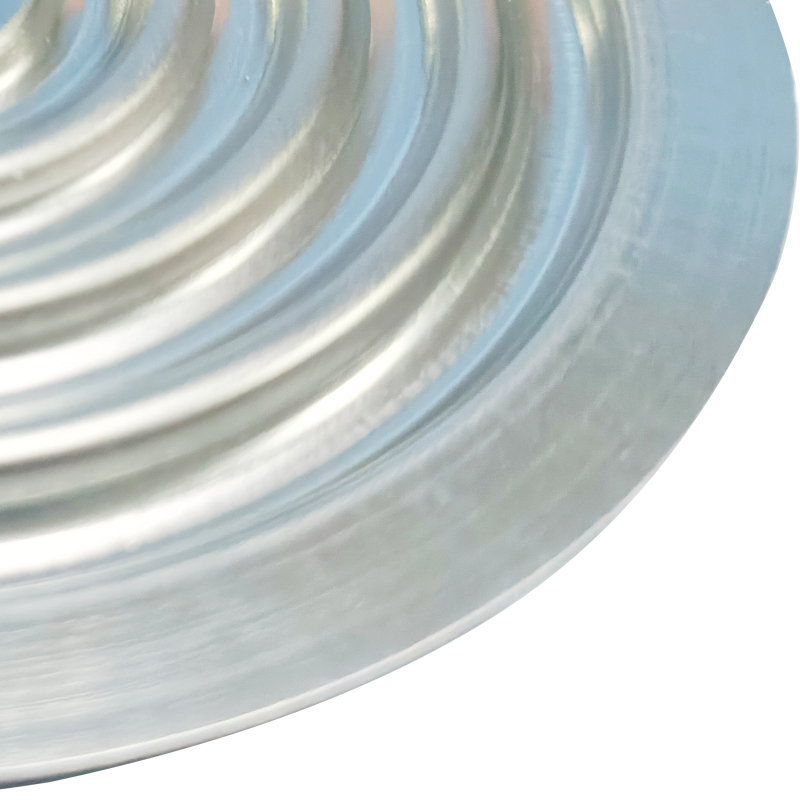
differential pressure gauge,
Authoritativeness in the realm of differential pressure gauges can be attributed to organizations that adhere to stringent manufacturing standards and industry certifications. Reputable manufacturers often comply with standards set by the American Society of Mechanical Engineers (ASME) or the International Organization for Standardization (ISO), ensuring that their products meet global benchmarks for accuracy and durability. These certifications provide end-users with confidence in the gauge's performance, fostering trust in the measurements they provide.
Trustworthiness of differential pressure gauges is further reinforced by their proven track record in enhancing operational efficiency and safety. In practical scenarios, these gauges have been pivotal in preventing catastrophic failures in systems where pressure imbalance could lead to equipment damage or safety hazards. For instance, in a chemical plant, monitoring the differential pressure across a filter allows operators to identify clogging quickly, thus circumventing potential process disruptions. Such real-world applications underscore the gauge's critical role in maintaining system integrity and demonstrate an inherent trustworthiness through consistent performance.
In conclusion, the differential pressure gauge is an indispensable tool in the industrial sector, embodying a fusion of experience, expertise, authoritativeness, and trustworthiness. Its ability to deliver precise and reliable pressure measurements under varying conditions makes it a preferred choice for industries aiming to maintain optimal operational standards. As technology evolves, so does the design and functionality of these gauges, promising even greater accuracy and ease of use. Those with a need for meticulous pressure monitoring can rely on the enduring reliability and innovative advancements of differential pressure gauges to meet their ever-expanding requirements.