Precision instruments, specifically pressure gauges, are vital components in various industries, ensuring accurate pressure measurement and consistent performance across different applications. With over two decades of experience interfacing with these devices, I can confidently assert their critical role in maintaining the safety, efficiency, and reliability of industrial processes.
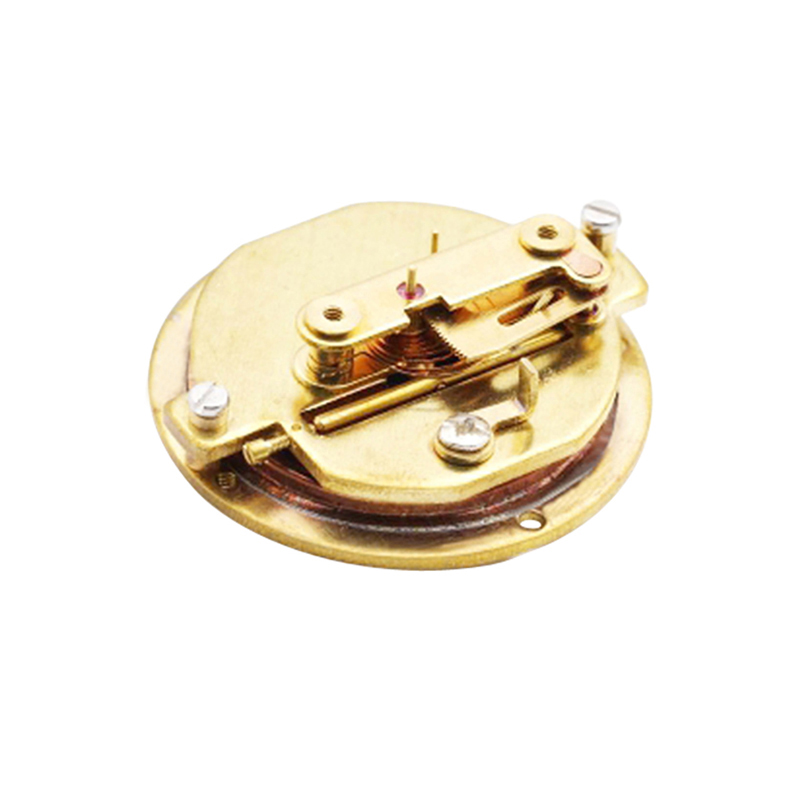
Pressure gauges are versatile tools used in sectors such as oil and gas, manufacturing, HVAC, and automotive. They serve the crucial function of monitoring pressure in systems, which is vital for maintaining operational safety and energy efficiency. Expertise in this area requires an understanding of different types of pressure gauges, each designed for specific environments and pressure ranges.
One common variety is the bourdon tube pressure gauge, known for its durability and reliability in measuring a wide range of pressures. These gauges use a coiled tube that reacts to pressure changes by expanding or contracting, thus driving a needle to give a pressure reading. Their robust design makes them suitable for both high-pressure ranges and harsh environments, such as in oil and petrochemical industries.
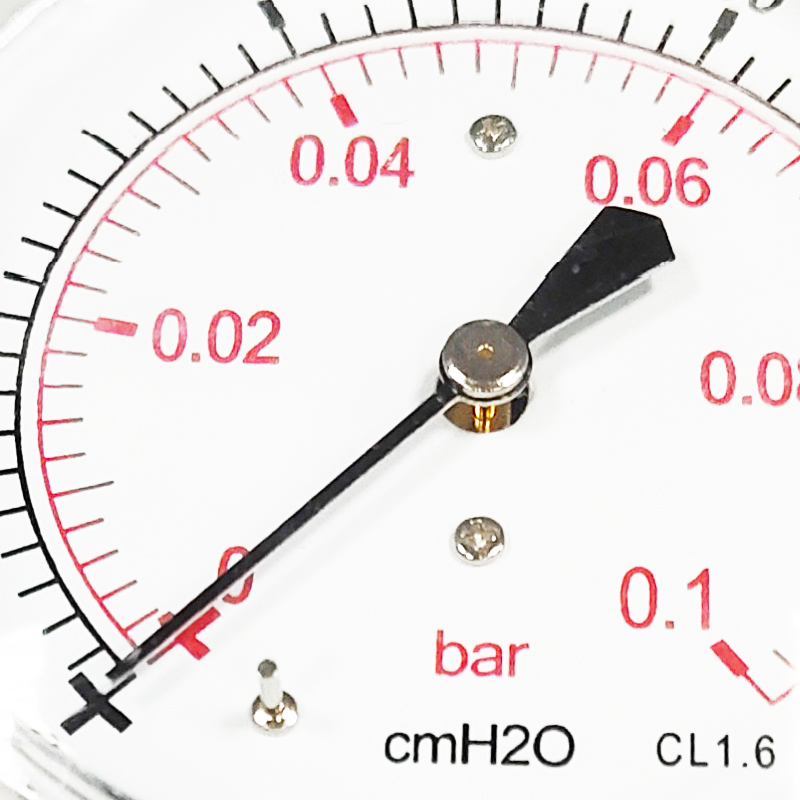
On the other end of the spectrum is the digital pressure gauge, which provides high precision measurements and often incorporates features such as data logging and wireless connectivity. These devices bridge traditional pressure measurement with modern technology, allowing for seamless integration into increasingly complex automated systems. Industries like pharmaceuticals and food processing, where precise pressure control is paramount, benefit significantly from these advancements.
Authoritativeness in pressure gauge selection involves evaluating the specific needs of the application. Factors such as the pressure range, the medium being measured, environmental conditions, and the required level of accuracy must be considered. In corrosive environments, for instance, gauges made of stainless steel or those with special coatings are often recommended to prevent material degradation.
precision instruments pressure gauge
Trust in a pressure gauge also comes from adherence to relevant standards and certifications, such as those from the American Society of Mechanical Engineers (ASME) and the International Organization for Standardization (ISO). These standards ensure that the instruments meet rigorous safety and performance criteria, providing end-users with reliable data necessary for decision-making.
Throughout my career, I have witnessed the transformative power of regular calibration in maintaining gauge accuracy and extending their operational lifespan. Calibration, typically performed annually, involves comparing the measurements from a gauge to a known standard, adjusting them as necessary to ensure continued precision. This process is crucial for upholding both safety and regulatory compliance, particularly in industries where exact pressure measurement is critical.
Finally, establishing a relationship with a reputable supplier or manufacturer, who can provide guidance and support, is invaluable. These companies should ideally offer comprehensive services including product consultation, installation support, and after-sales service, which are essential components of a sustainable pressure management strategy.
The world of precision instruments and pressure gauges is complex and requires both technical knowledge and practical experience for optimal application. By staying informed about technological advances, adhering to industry standards, and maintaining regular maintenance routines, industries can leverage these indispensable tools to enhance safety, efficiency, and overall productivity.