Pressure diaphragms are integral components in various industrial applications, where precision and durability are paramount. These flexible membranes are used in a wide range of devices to separate two different environments while transmitting pressure. Their ability to convert pressure variations into mechanical deflection makes them indispensable in fields such as aerospace, automotive, medical devices, and industrial manufacturing.

In the realm of aerospace engineering, pressure diaphragms serve a critical role in ensuring the safety and efficiency of aircraft systems. With the necessity to manage and measure pressure changes in fuel systems and cabin environments accurately, diaphragms made from advanced polymers or metal composites are often employed. Their robust construction allows them to withstand extreme temperatures and pressures, making them reliable in the harshest conditions encountered at high altitudes.
The automotive industry also benefits significantly from pressure diaphragms, particularly in fuel injection systems and brake fluid regulation. These components ensure that vehicles perform optimally by maintaining the necessary pressure levels. The choice of diaphragm material is crucial here; typically, elastomers or stainless steel diaphragms are selected for their durability and resistance to chemical degradation. Engineers value the precision these diaphragms provide, translating into better fuel efficiency and safer braking systems.
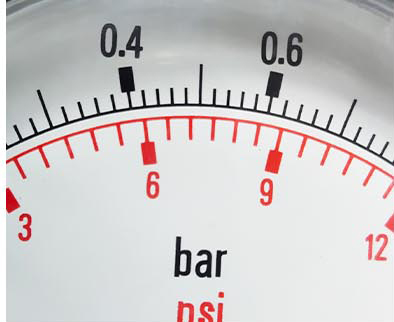
Medical devices, where precision and sterility cannot be compromised, also rely heavily on pressure diaphragms. In ventilators and infusion pumps, these membranes help control fluid or air flow with exact precision, providing patients with the right dosage of medication or the correct volume of air. The material selection in this sector leans towards biocompatible polymers, which offer both elasticity and resistance to sterilization processes.
Industrially, pressure diaphragms find their use in devices like pressure transmitters and switches. These are essential for process monitoring and control across many manufacturing domains. By converting pressure changes into readable electrical signals, these diaphragms allow for real-time monitoring and automation, crucial for maintaining product quality and operational efficiency. Manufacturers opt for diaphragms that exhibit excellent wear resistance and a low hysteresis error to enhance the reliability and accuracy of measurements.
pressure diaphragm,
The expertise required in designing and manufacturing pressure diaphragms cannot be understated. Engineers must consider factors such as material compatibility, environmental conditions, and required sensitivity. Innovations in material science have led to the development of composite diaphragms that offer superior performance characteristics. These advancements are critical for applications requiring miniaturized components, as seen in the burgeoning field of wearable technology.
Trust in the performance of pressure diaphragms comes from thorough testing and quality assurance. Industry standards such as ISO 9001 and material certifications ensure that each diaphragm meets the rigorous expectations of its specific application. Companies known for their high-quality pressure diaphragms typically maintain detailed documentation and traceability for their products, further establishing credibility and trustworthiness in the marketplace.
As industries continue to evolve, the demand for reliable pressure management solutions will grow, leading to further innovations in diaphragm technology. From enhancing the materials used to integrating smart sensors that provide real-time data analytics, the future of pressure diaphragms is poised to offer even greater precision and efficiency.
In conclusion, pressure diaphragms are a testament to advanced engineering and material science, offering essential solutions across diverse industries. Their evolution reflects an ongoing commitment to safety, efficiency, and technological advancement, making them indispensable in an era that values precision and reliability.