OEM differential pressure gauges are instrumental in industrial and commercial applications, providing essential data for systems reliant on precise pressure measurements. These devices operate by measuring the difference in pressure between two points and are crucial for optimizing performance, ensuring safety, and maintaining efficiency in various systems. Leveraging years of expertise in industrial instrumentation, this article delves into the intricacies of OEM differential pressure gauges to enhance understanding and appreciation among industry professionals, contributing to a reliable and authoritative source of knowledge.

Differential pressure gauges find their applications in diverse sectors such as HVAC, filtration systems, and fluid mechanics. Their capability to provide accurate pressure readings is vital for processes where maintaining specific pressure ranges is necessary for operational integrity. For instance, in HVAC systems, these gauges ensure that air conditioning units operate efficiently by monitoring airflow and detecting blockages. Their role in filtration systems is similarly essential, as they signal when filters require replacement, therefore maintaining optimal performance and preventing system damage.
The design of OEM differential pressure gauges is tailored to meet the specific requirements of equipment manufacturers. Such customization ensures seamless integration into existing systems, enhancing the overall functionality without requiring significant modifications. OEM gauges are built with precision engineering, showcasing a commitment to reliability, durability, and accuracy. This precision engineering is a testament to the expertise behind their design and manufacture, contributing to the gauges' trusted status in high-stakes environments.
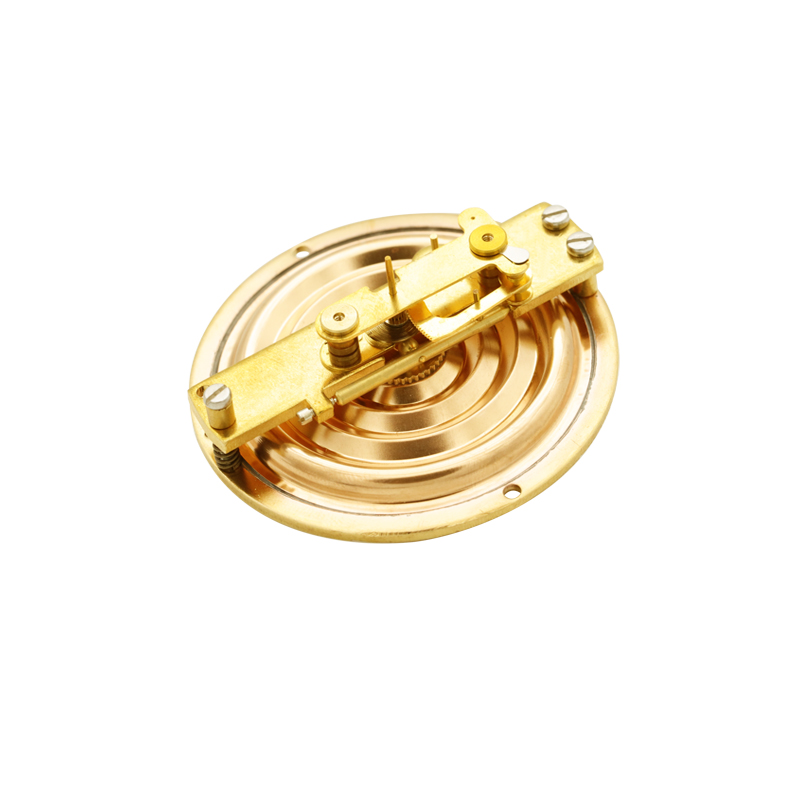
Selecting the appropriate OEM differential pressure gauge involves understanding the unique demands of the application. Factors such as pressure range, media compatibility, and environmental conditions play a pivotal role in choosing the right gauge. Modern gauges are constructed with robust materials to withstand harsh conditions, including extreme temperatures and corrosive substances. This resilience is crucial for gauges used in demanding industries like oil and gas, where equipment performance can significantly impact safety and operational efficiency.
Operational accuracy is a vital consideration for OEM differential pressure gauges, driving manufacturers to employ advanced technologies in their production. High-precision sensor technologies, such as capacitive and piezo-resistive sensors, are integrated into the design, offering unparalleled measurement accuracy. These technologies ensure that measurements are not only precise but repeatable, an essential factor for maintaining trust and reliability over time.
oem differential presure gauge
The authority of OEM differential pressure gauges is further emphasized through compliance with international standards. Adhering to standards such as ISO, ASME, and CE attests to their quality and reliability. These certifications are not merely formalities but robust validations of the gauges' performance and safety control, facilitating trust among end-users and industry professionals.
Equally important is the trustworthiness associated with the manufacturers of these gauges. Established OEMs with a proven track record in the industry often possess extensive portfolios showcasing successful implementations across multiple sectors. These manufacturers provide comprehensive customer support, technical assistance, and product warranties, ensuring confidence in the performance and longevity of their gauges.
Custom feedback from industry use cases further enriches the credibility and expertise of OEM differential pressure gauges. End-users report enhanced operational efficiency, improved system reliability, and reduced maintenance costs as direct benefits of implementing these gauges. Such testimonials are invaluable, offering real-world proof of the gauges' effectiveness and fostering an environment of trust and dependability.
Moreover, the evolution of digital technologies has revolutionized OEM differential pressure gauges, incorporating features like wireless connectivity and data logging. These advancements provide users with real-time monitoring and diagnostics, enabling prompt decision-making and minimizing downtime. The integration of IoT platforms allows for seamless data acquisition and analysis, further cementing the gauges' role as crucial components in a digitalized industrial landscape.
In conclusion, OEM differential pressure gauges represent a culmination of technical prowess, comprehensive industry experience, and unwavering commitment to quality. Their indispensable role across various sectors underscores their importance, making them vital tools in modern industrial applications. By delivering precise pressure measurements, ensuring system safety, and optimizing operational efficiency, these gauges empower industries to achieve their potential, backed by expertise that is trusted and recognized globally.